In the world of industrial manufacturing, kilns play a pivotal role in processes such as cement production, ceramics, metallurgy, and more. At the heart of every efficient kiln line lies a critical component: refractory bricks. These specialized bricks are engineered to withstand extreme temperatures, mechanical stress, and chemical corrosion, ensuring the longevity and efficiency of kiln operations. In this article, we will explore the importance of refractory bricks in kiln lines, their properties, types, and applications.
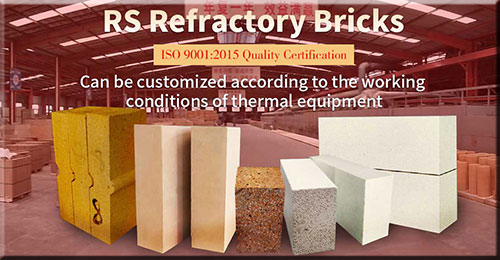
What Are Refractory Bricks?
Refractory bricks are high-temperature-resistant materials designed to line the interiors of kilns, furnaces, and other thermal processing equipment. They are composed of refractory ceramics, which include materials like alumina, silica, magnesia, and zirconia. These materials are chosen for their ability to maintain structural integrity under extreme heat and harsh conditions.
Why Are Refractory Bricks Essential for Kiln Lines?
Kiln lines operate at temperatures that can exceed 1,000°C (1,832°F), making them one of the most demanding environments in industrial settings. Refractory bricks serve several critical functions in kiln lines:
- Thermal Insulation: Refractory bricks act as insulators, reducing heat loss and improving energy efficiency. This ensures that the kiln maintains consistent temperatures, which is crucial for product quality.
- Heat Resistance: These bricks can withstand extreme temperatures without melting, cracking, or degrading. This property is vital for the continuous operation of kilns.
- Mechanical Strength: Kiln lines are subject to mechanical stress due to the weight of materials and thermal expansion. Refractory bricks provide the necessary strength to withstand these forces.
- Chemical Resistance: Many industrial processes involve corrosive materials or gases. Refractory bricks are designed to resist chemical erosion, ensuring a longer lifespan for the kiln lining.
Types of Refractory Bricks Used in Kiln Lines
Refractory bricks are classified based on their composition and properties. The most common types used in kiln lines include:
- Fireclay Bricks: Made from fireclay, these bricks are cost-effective and suitable for moderate-temperature applications. They are commonly used in the preheating and cooling zones of kilns.
- High-Alumina Bricks: Containing a high percentage of alumina (up to 90%), these bricks offer superior strength and resistance to abrasion. They are ideal for the burning zone of cement kilns.
- Silica Bricks: Composed primarily of silica, these bricks are highly resistant to thermal shock and are often used in glass-making kilns.
- Magnesia Bricks: Made from magnesia, these bricks are highly resistant to alkaline environments and are commonly used in steel-making kilns.
- Insulating Bricks: These lightweight bricks are designed to reduce heat loss and improve energy efficiency. They are often used as a secondary lining in kilns.
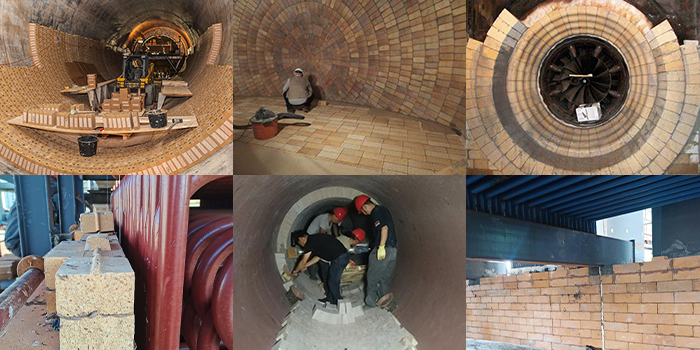
Applications of Refractory Bricks in Kiln Lines
Refractory bricks are used in various sections of kiln lines, each with specific requirements:
- Preheating Zone: In this zone, raw materials are heated gradually. Fireclay bricks are often used here due to their moderate heat resistance and cost-effectiveness.
- Burning Zone: This is the hottest part of the kiln, where chemical reactions occur. High-alumina bricks are preferred for their ability to withstand extreme temperatures and chemical corrosion.
- Cooling Zone: After the burning process, materials need to be cooled slowly to prevent cracking. Refractory bricks with good thermal shock resistance, such as silica bricks, are used in this zone.
- Transition Zone: This area connects the preheating and burning zones. Magnesia bricks are often used here due to their resistance to thermal and mechanical stress.
Advantages of Using Refractory Bricks in Kiln Lines
- Extended Lifespan: Refractory bricks significantly increase the lifespan of kiln linings, reducing the need for frequent repairs and replacements.
- Energy Efficiency: By minimizing heat loss, refractory bricks help reduce energy consumption, leading to cost savings and a smaller environmental footprint.
- Improved Product Quality: Consistent temperatures and reduced contamination from chemical reactions ensure higher-quality end products.
- Versatility: With a wide range of refractory bricks available, manufacturers can choose the best type for their specific kiln line requirements.
Challenges and Considerations
While refractory bricks offer numerous benefits, selecting the right type and maintaining them properly are crucial. Factors to consider include:
- Operating Temperature: The bricks must be chosen based on the maximum temperature of the kiln.
- Chemical Environment: The presence of corrosive materials or gases may require specialized bricks.
- Thermal Shock Resistance: Rapid temperature changes can cause cracking, so bricks with high thermal shock resistance are essential.
- Installation and Maintenance: Proper installation and regular maintenance are necessary to maximize the performance and lifespan of refractory bricks.
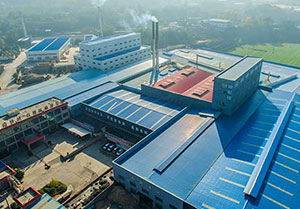
RS Refractory Fire Bricks Factory
Refractory bricks are indispensable components of kiln lines, providing the necessary heat resistance, mechanical strength, and chemical stability required for efficient and reliable operation. By understanding the properties and applications of different types of refractory bricks, manufacturers can optimize their kiln lines for improved performance, energy efficiency, and product quality. At RS Refractory Fire Bricks Factory, we specialize in producing high-quality refractory bricks tailored to meet the unique demands of your kiln line. Contact us today to learn more about our products and how we can help enhance your industrial processes.
This article provides a comprehensive overview of refractory bricks used in kiln lines, highlighting their importance, types, applications, and benefits. Whether you are in the cement, ceramics, or metallurgy industry, understanding the role of refractory bricks can help you make informed decisions for your kiln line operations.