Commonly used refractory materials for building fluidized bed furnace lining mainly include refractory bricks and unshaped refractory castables. Among them, shaped refractory bricks include high alumina bricks, clay bricks, clay insulation bricks, and diatomite insulation bricks. In addition to the above-mentioned 4 furnace refractory bricks products, ceramic fiber products, and a large number of refractory castables, refractory castable preforms, refractory mortar, anticorrosive coatings, etc. are also used in the lining of the Fluidized Bed furnace. These refractory products must be strictly implemented in accordance with national standards or industry standards in the process of material purchase, construction, and quality acceptance.
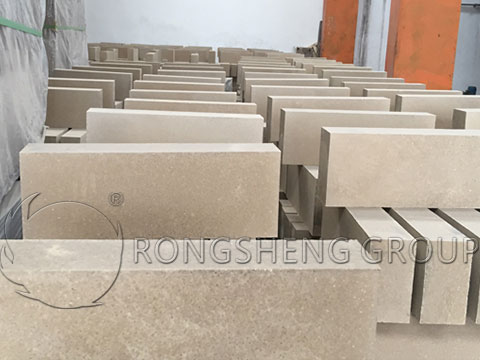
Laying Refractory Materials for the Lining of Fluidized-Bed Furnaces in Different Parts
The refractory brick body of the combustion channel of the boiling furnace. Above the boiling layer of the fluidizing roaster, there are 1 to 4 burners depending on the diameter of the furnace, which is used for the oven and the furnace to heat the charge. Because the Fluidized Bed Furnace is a cylindrical furnace wall, and the frustum-shaped combustion channel is inclined to the surface of the boiling layer, the combustion channel bricks are all special-shaped refractory bricks, which brings great difficulties to the design and manufacturing. Moreover, the number of bricks for each brick type is limited, and the price of special-shaped refractory bricks is high. Therefore, most designs are cast on-site with aluminate cement refractory castable, which brings convenience to the design, manufacture, and site construction of furnace refractory bricks.
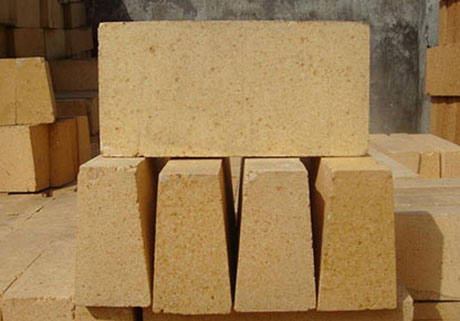
The refractory brick body of the furnace wall of the boiling furnace. The furnace wall is generally lined with clay refractory bricks. In recent years, the newly built large-scale Fluidized Bed Furnace is built with high-aluminum refractory bricks. On the outside of clay bricks or high-alumina refractory bricks, masonry insulation bricks (diatomite refractory bricks or high-strength lightweight clay bricks) are built. Fill the insulation material (asbestos board, diatomite) between the insulation brick and the furnace shell steel plate.
The roof structure of the boiling furnace. The spherical top of the Fluidized Bed Furnace is made of refractory brick masonry or cast refractory. The thickness of the dome made of refractory bricks is often 230mm, 250mm, or 300mm. Depending on the diameter of the furnace, the shape of the refractory bricks needs to be configured with several special-shaped refractory bricks according to the diameter of the dome. Matched with masonry or one brick for each ring, the commonly used furnace refractory bricks material is refractory clay brick or high alumina brick. Approximately 200mm insulation material is laid outside the top of the refractory brick ball. Insulation materials often choose light clay bricks, diatomaceous earth, slag wool, vermiculite, and expanded perlite.
Refractory Materials for Fluidized Bed Furnaces must Meet the Requirements for Winter Construction
Refractory materials, whether it is shaped refractory bricks or unshaped refractory castables, etc., during the winter construction process, the harsh climate environment is an important factor affecting the quality of product construction. In actual operations, corresponding heating measures must be taken to ensure that the materials can perform their due performance.
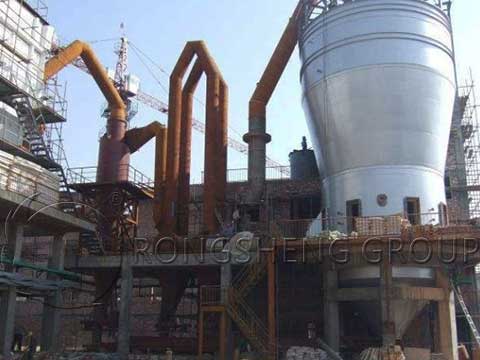
During the winter masonry construction of the boiling furnace, when the outdoor ambient temperature is lower than 5°C for 5 consecutive days, it shall be regarded as the winter construction of the boiling furnace. Strictly speaking, a Fluidized Bed Furnace is not suitable for construction in winter. However, if construction is necessary due to urgent production and engineering needs, in addition to complying with the rules and regulations in the industry standards, the following requirements should also be observed.
- After the refractory products such as refractory bricks and refractory castables used in masonry enter the site, they should not be stored in the open environment to avoid snow or freezing.
- Heating measures must be taken when building. The construction environment temperature must be above 5℃.
- The temperature of refractory products must meet the requirements of Table 1.
- During the mixing process of refractory castables, the water temperature varies according to the different binders. Aluminate cement refractory castable ≤30℃, water glass refractory castable ≤60℃. In the heating process, only the aggregate is heated, and the cement is not allowed to be directly heated. It should be heated by a warm shed, and direct flame heating is strictly prohibited.
- The curing of sodium silicate refractory castable can be done by heat storage method or heating method, the heating temperature is less than 80℃. The curing of phosphate refractory castable should adopt the dry heat method, and its heating temperature is less than 60℃.
- After the Fluidized Bed Furnace is built, in principle, the furnace should be baked in time. If the furnace cannot be put into production in time, drying or anti-freezing and heat preservation measures should be taken, and the temperature around the masonry should be kept above 5°C.
Table 1 Temperature Requirements During Refractory Construction | |||||
Items | Refractory bricks, Refractory Preforms | Refractory Mortar | Cement-bonded Castable | Chemically Bonded Castable | |
Water Glass Bonded | Phosphate Bonded | ||||
Product Temperature | ≥ 0 ℃ | – | |||
Construction Temperature | – | ≥ 5 ℃ | ≥ 5 ℃ | ≥ 10 ℃ | ≥ 10 ℃ |
In the above regulations, the temperature involved should be measured and recorded every 2h.
Oven-Drying after Completion of Fluidized-Bed Furnace Refractory Bricks Masonry
After the kiln refractory bricks are completed, there will be a baking process. The purpose of the oven is to discharge the water vapor or moisture contained in the masonry refractories to form a dry body. Refractory bricks generally choose wet or dry masonry. The refractory mud used in the construction of refractory bricks is mixed with binders such as water or gelling agents, so the refractory bricks must be baked after the construction is completed to remove the moisture in the furnace refractory bricks lining. Avoid floating the water vapor in the refractory bricks after normal use, causing the bricks to loosen. After the lining of refractory bricks is completed, there is no stipulation on how long the oven must be baked. If the furnace does not need to be used immediately after the masonry is completed, the furnace can be dried just before use. However, it should be noted that during this period, the kiln must be in a state of natural ventilation. In addition, the furnace lining must not see water, especially refractory bricks.
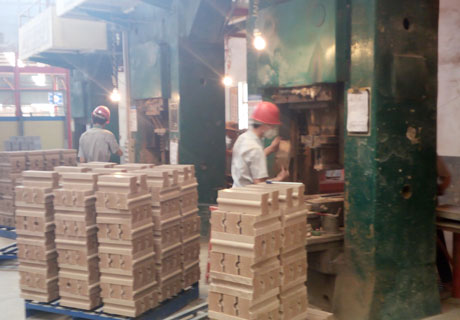
The construction and drying of furnace refractory bricks lining are the key steps before the high-temperature kiln starts. They all directly affect the service life of refractory brick linings of high-temperature kilns. Therefore, Rongsheng kiln refractory material manufacturers remind customers to pay attention to the correct construction and maintenance of the kiln refractory lining. This can reduce the number of shutdowns and repairs as much as possible, save production costs, and improve economic benefits.