Diatomaceous earth bricks refer to insulation products made of porous diatomaceous earth. The main raw material is natural porous diatomaceous earth, and a small amount of combined clay and combustible materials are added. Rongsheng refractory brick for sale, The bulk density of diatomite bricks is 0.7g/cm3, and the compressive strength at room temperature is 1~2MPa. The thermal conductivity at 400°C is 0.13~0.20W/(m·K). The apparent porosity is greater than 70%, the thermal expansion coefficient (at 1280°C) is 0.9×10-6°C-1, and the refractoriness is greater than 1250°C. Diatomite brick is mainly used as thermal insulating refractory materials for industrial kilns and other thermal equipment and thermal pipelines. Generally, the temperature of the hot surface is about 1000℃.
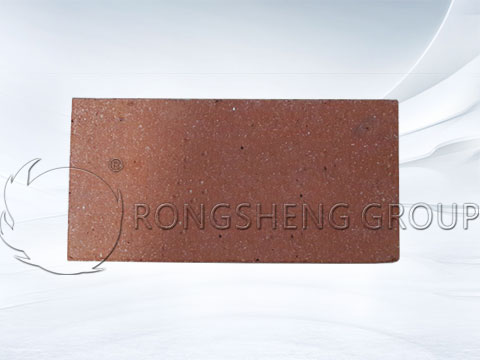
Classification of Diatomite Bricks
Diatomite bricks are made by adding a small amount of combined clay and combustibles to diatomite, then wetting, mixing, forming, and firing to make refractory products of different shapes. According to the complexity of the shape, it is divided into standard type, general type, special type, and special type. Divided into 6 types according to bulk density, the range of bulk density: 0.4~0.7g/cm3.
Diatomite insulation brick
Diatomite bricks are also called diatomite insulating bricks. Its definition refers to insulating refractory products made of diatomaceous earth as the main raw material. Diatomite insulation bricks have fine closed pores, high porosity, good thermal insulation performance, but low mechanical strength, especially after being damp, the strength is significantly reduced. Its main chemical composition is SiO2, followed by Al2O3, and impurities such as iron, potassium, sodium, calcium, and magnesium oxides.
Diatomite Insulating Brick
- Subject: Metallurgical Engineering
- Field: Energy
- Range: Refractory
- Interpretation: Refractory products made of diatomite as the main raw material
Physical and Chemical Indexes of High-Strength Diatomite Bricks
Items | GG-0.7A | GG-0.7 | GG-0.6 | GG-0.5 | GG-0.4 |
Bulk Density g/cm3≤ | 0.7 | 0.7 | 0.6 | 0.5 | 0.4 |
Cold Crushing Strength Mpa≥ | 2.5 | 1.2 | 0.8 | 0.8 | 0.8 |
Test temperature ℃ (Reburn Line Changes ≤2%, Moisturizing 8h) | 900 | 900 | 900 | 900 | 900 |
Thermal Conductivity W/m.k (300℃) ≤ | 0.20 | 0.20 | 0.17 | 0.16 | 0.13 |
The Production Process of Diatomite Thermal Insulation Brick
Including 5 parts of raw materials and their processing, ingredients, and mixing, forming, and firing. The specific operation process is as follows:
Raw Material Selection and Processing
The main raw materials for the manufacture of diatomite insulation bricks are diatomite, fly ash, sawdust, and waste insulation refractory brick return materials. Diatomite has a certain degree of plasticity. The finer the particles, the better the plasticity. The diatomite used for making bricks should meet the following requirements:
- SiO2 content is greater than 65%;
- The content of Al2O3 is less than 18%;
- Fe2O3 content is less than 7%;
- The burn is reduced to 14%.
In order to improve the plasticity of diatomaceous earth and remove some soluble salts and (impurities) to improve its physical and chemical properties, there should be a certain weathering period before use.
For the processing of raw materials, different methods are adopted according to the quality and technological requirements of diatomite. Some have to be broken to less than 1.5mm, some are made of weathered pieces, some of the newly mined diatomaceous earth needs to be stirred into small mud with a trowel, and some are moistened with water. The moisture content of fly ash in thermal power plants should be less than 26%. The moisture content of the sawdust should be less than 50%, and the waste products and recycled materials with a particle size of less than 1mm should be crushed and sieved. The waste products should pass through a 1.5mm sieve, and the recycled materials should pass through a 1mm sieve. Finally, mix into the brick material in proportion. In order to make bricks have better molding and sintering properties, some production plants add binders and mineralizers, such as iron scales, lime milk, and sulfite pulp waste liquid, to the bricks.
Ingredients and Mixing
In order to reduce the shrinkage and cracking of the green body during drying and firing, a certain proportion of fly ash and clinker are added to the ingredients. When producing low-density products, a certain proportion of sawdust is added to the ingredients. The proportion of various materials needs to be determined according to the product brand, quality requirements, molding method, and firing conditions, and other process conditions. Kneading is carried out in a twin-shaft mixer or kneading machine. When the temperature is low, hot water and steam should be introduced. The moisture of the mud varies depending on the molding method and grade, generally 35%-50%.
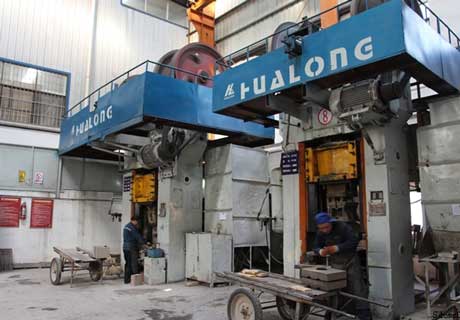
Forming
Diatomite bricks are generally formed by extrusion molding, press molding, and manual molding.
- Extrusion molding. The mud is fed into the extruder to extrude the mud sticks of the specified size and then cut into the required thickness or length with a cutting machine.
- Press molding. It is pressed in a brick press with a nominal name of 15-300kN, but during the pressing operation, spalling and cracking due to elastic after-effects should be prevented.
- Manual molding. The quantity is small, the shape is complicated and the large-scale products are formed by hand using wooden molds.
Dry
In a fire pit or tunnel dryer. Due to the high forming moisture of the bricks, low temperature and slow drying should be used to avoid cracks. When a tunnel dryer is used for drying, the brick inlet temperature should be controlled at 40-50°C, the outlet temperature should be around 150°C, and sufficient airflow should be ensured. The residual moisture of the dried bricks should be controlled below 3%, and large or complex-shaped products should be controlled below 1%.
Firing
Kiln installation mostly adopts the “well” code method, and the stacking height does not exceed 1.5m. When firing is in the low-temperature stage (below 200°C), it is mainly to remove physical water, and the temperature should not be too fast. Adjust the fire gate during operation to increase the suction force in the kiln to increase the ventilation. After 200°C, the crystal water and compound decomposition begin to be eliminated. When the temperature is 500-600℃, the sawdust and other organic matter in the brick will burn, and the oxidizing atmosphere should be maintained in the kiln to facilitate the full combustion of the organic matter. The final firing temperature can be controlled at about 900°C. Some of the fired products need to be reshaped to become the final product.
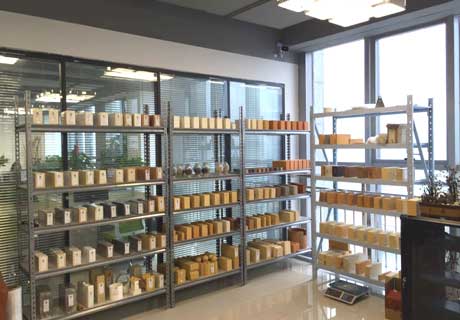
Rongsheng Refractory Brick Manufacturer
Rongsheng is an experienced refractory brick manufacturer. Rongsheng’s refractory products have been sold to more than 60 countries and regions all over the world. For example, India, Pakistan, Kuwait, South Africa, Malaysia, Vietnam, Netherlands, Philippines, Singapore, Egypt, Russia, etc. Rongsheng’s refractory brick manufacturers are very satisfied with customers in terms of product quality and customer service. Rongsheng produces a variety of insulating fire brick for sale, such as alumina bubble bricks, lightweight silica bricks, mullite insulation bricks, diatomite insulation bricks, etc. No matter what kind of insulating refractory bricks you need, Rongsheng’s technical team can provide you with refractory brick products that best suit your production needs. For more information on refractory bricks for sale, please leave your specific needs on our website page, and we will reply to you within 24 hours.