The main crystal phase of magnesia bricks is periclase, which has the typical characteristics of general alkaline refractory products. According to different use requirements and production processes, magnesia refractory bricks such as magnesia bricks also include many other types. One of them is directly combined with magnesia-chrome bricks, which are named according to the production process. Rongsheng refractory brick manufacturer can provide direct bonded magnesia chrome bricks of the magnesia brick series, quote for free prices, and samples.
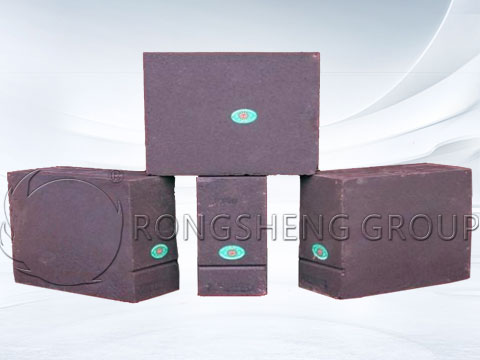
Grades and Applications of Direct Bonded Magnesia Chrome Brick
Magnesia bricks are widely used. Among them, the high-temperature industrial kiln is direct bonded magnesia chrome brick, which are divided into four grades: ZMGe-8, ZMGe-12, ZMGe-16, and ZMGe-20 according to physical and chemical indicators. It has the characteristics of high-temperature structural strength, high load softening temperature, and strong chemical corrosion resistance. Main application: Widely used in cement rotary kiln firing zone, glass melting furnaces, steelmaking electric furnaces, converters, non-ferrous metal smelting furnaces, etc.
Performance and Production Process of Directly Combined Magnesia-Chrome Bricks
Directly bonded magnesia-chrome bricks have fewer impurities. After high-temperature and ultra-high-temperature firing, the glass phase is concentrated in the triangular area of the crystal phase, and the crystal phase and the crystal phase are directly combined. This type of magnesia-chrome brick has low porosity, high compressive strength, strong wear resistance, good corrosion resistance, thermal shock resistance, and spalling resistance.
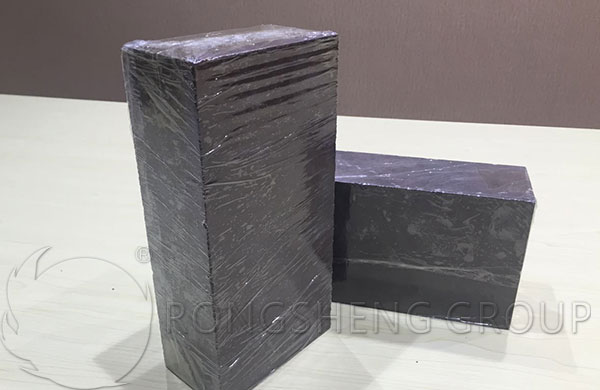
When it comes to the production process of direct-bond magnesite chrome bricks, firstly start from direct-bond magnesite chrome brick, it refers to refractory products that are directly combined with periclase and magnesite chrome spinel as the main crystal phase. The brick is made of high-purity sintered magnesia and chromite with SiO2 less than 2% as raw materials and sintered at high temperatures. Direct bonded magnesia chrome bricks are products made from high-purity or sub-high-purity sintered or fused magnesia and chrome concentrate. Direct bonding refers to a bond produced by direct contact between solid-phase grains. The brick is made of high-purity sintered magnesia and chrome concentrate with SiO2<2% as raw materials and is sintered at high temperatures. The degree of direct bonding of the product increases with the decrease of SiO2 content and the increase of firing temperature.
When producing directly bonded magnesia-chrome bricks, chrome ore with low SiO2 content should be selected as much as possible, because low SiO2 content is beneficial to improve the high-temperature performance of such refractory bricks. By comparing the properties of various magnesia-chrome bricks, it is found that the load-softening temperature of directly bonded magnesia-chrome bricks produced by selecting high-purity SiO2 (low content) chrome ore is high. Of course, magnesia-chrome bricks with low SiO2 content also need to be fired at high temperatures or low temperatures. As many research works have pointed out. Although there is no obvious dividing line between silicate-bonded (ceramic-bonded) magnesia-chrome bricks and direct-bonded magnesia-chrome bricks, there is actually no direct bonding in magnesia-chrome bricks fired below 1500 °C. Only when the firing temperature exceeds 1550 °C, their direct bonding will increase.
Since the current magnesia-chrome bricks are all fired above 1500°C, they are only different in the degree of direct bonding. This shows that the primary condition for the production of direct bonded magnesia-chrome refractory bricks is firing at high temperatures or low temperatures. For example, magnesia-chrome bricks containing 1.5% SiO2 are fired at 1800 ° C, compared with other magnesia-chrome bricks, because the amount of direct bonding of the high refractory phase increases. However, too high a firing temperature will also cause deformation and upside-down of such magnesia-chrome bricks and increase the amount of waste refractory bricks.
In order to reduce the waste products caused by firing deformation, the measures taken in the process technology are to reduce the SiO2 content in the ingredients (especially the SiO2 content in the chrome ore). The amount of direct bonding in magnesia-chrome bricks increases significantly with the decrease in SiO2 content. This is because when the SiO2 content is reduced, the silicate layer in the material is replaced by the direct combination between the crystals of the high refractory phase.
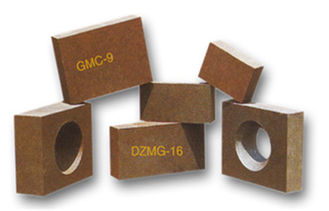
The difference between directly combined magnesia chrome bricks and ordinary magnesia chrome bricks
- Ordinary magnesia-chrome bricks contain MgO 55~80%, Cr2O3 ≥8% (generally 8~20%). The main minerals are periclase and chromium spinel, and the silicate phase is forsterite and forsterite. If the Cr2O3 content is as high as 18~30%, MgO 25~55%, it is called chrome-magnesia brick. (Note: Cr2O3≥20%, is equivalent to adding more than 50% of chromite in the batching, and Cr2O3≥8%, is equivalent to adding more than 20%).
- Directly bonded magnesia-chrome bricks can be used in large kilns with a kiln temperature above 1700°C. Ordinary magnesia-chrome bricks are no longer competent, and the direct combination of magnesia-chrome bricks is a high-quality magnesia-chrome refractory developed to adapt to large-scale cement production.
Directly combined with the main minerals of magnesia-chrome bricks, periclase, and spinel are mostly directly combined. Although there is a small amount of silicate phase matrix, the direct binding rate is high. Therefore, the high-temperature performance of the refractory brick body is greatly improved. Directly bonded magnesia-chrome bricks are made of high-quality magnesite ore and chromite ore, which are first fired into light-burnt magnesia. According to a certain gradation, it is formed into balls under high pressure and fired at a high temperature of 1900°C to produce dead-burned magnesia. Add a certain proportion of chromite ore and press molding. It is calcined in a tunnel kiln at 1750~1850℃. Those fired at 1750~1800°C are high-temperature directly bonded magnesia-chrome bricks. Those fired at 1800~1850°C are directly bonded magnesia-chrome bricks.
Why is the load-softening temperature of directly bonded magnesia-chrome bricks smaller than that of directly bonded magnesia bricks?
Due to the different raw material purity and ratio of magnesia brick products, the load is also different. These performance indicators of magnesia-chrome bricks can be customized according to customer needs, so as to realize the actual use requirements of the refractory lining of thermal furnaces.
Magnesia-chrome bricks are divided into ordinary magnesia-chrome bricks, direct bonded magnesia-chrome bricks, semi-bonded magnesia-chrome bricks, fused magnesia-chrome bricks, electric fused semi-bonded magnesia-chrome bricks, and unfired magnesia-chrome bricks. The difference between magnesia-chrome bricks and directly bonded magnesia-chrome bricks is that
- The purity of magnesia (raw material).
- Sintering temperature. The sintering temperature of ordinary magnesia-chrome bricks is 1550 ℃ ~ 1600 ℃, and the sintering temperature of direct magnesia-chrome bricks is above 1700 ℃. Because when it is above 1700 ° C, the microstructure of magnesia-chrome bricks changes. Periclase is directly combined with chrome ore, so it is called directly combined magnesia-chrome brick. The properties of directly combined magnesia-chrome bricks are better than ordinary magnesia-chrome bricks.
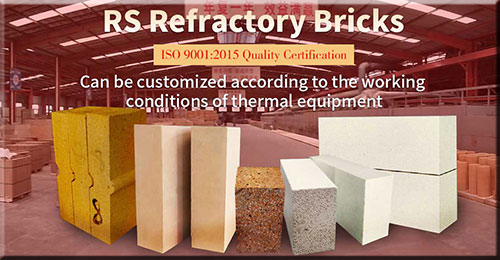
Rongsheng Magnesia Chrome Refractory Manufacturer
Directly bonded magnesia-chrome bricks are mainly used in the refining part of the smelting industry, non-ferrous smelting, reaction furnace, and heat storage part of the glass industry. The product specifications of the magnesia-chrome refractory bricks of Rongsheng refractory brick manufacturers can reach 380*150*75/65 (mm). Rongsheng refractory brick manufacturer is a powerful refractory brick manufacturer and seller. Rongsheng’s refractory bricks have been sold to more than 70 countries and regions around the world. And it has a good effect on the customer’s industrial furnace, prolonging the service life of the refractory lining. Received high praise and praise from customers. The magnesia, magnesia-chrome, and chrome-corundum refractory bricks produced by Rongsheng refractory manufacturers are widely used in non-ferrous metallurgy, steel plant electric furnaces, rotary kilns, and other high-temperature kilns. Contact us for free price information for directly bonded magnesia chrome bricks. More opportunities to obtain free construction plan design and sample services.