Due to the chrome pollution, currently, Europe, Japan, the United States, and other countries and regions have basically no chrome-containing materials due to government mandatory regulations. However, most of the basic refractories for non-ferrous kilns produced by domestic enterprises are still chrome-containing refractories, which has also attracted great attention from the national government. The implementation of chrome-free refractories is an inevitable trend. Currently, chrome-free alkaline refractory materials used in kilns include chrome-free alkaline composite spinel bricks, Magnesia Alumina Zirconia Brick, and so on.
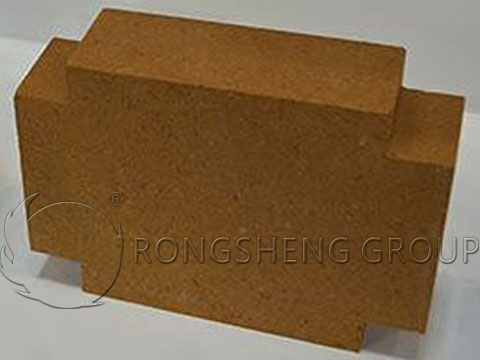
Magnesia Alumina Zirconia Brick
ZrO2 is a weakly acidic oxide, which has a remarkable resistance to acid or neutral slag erosion. MgO has high resistance to alkaline slag. And MgO·Al2O3 has good corrosion resistance. The composite Magnesia Alumina Zirconia Brick can resist the non-ferrous smelting slag with large changes in alkalinity.
Magnesia Alumina Zirconia Bricks are made by directly adding 2% desiliconized zirconia to magnesia oxide and Magnesia Alumina spinel. Unconventional particle grading is used to reduce the difference in particle level and increase the ratio of fine powder and ultra-fine powder for batching. It not only follows a certain “principle of close packing of particles”, but also reduces the difference in particle size and weakens the damage to the reasonable structure of bricks caused by the stress concentration caused by large particles.
It is formed by a high-stroke 630-ton friction brick press. The blank size is 230×114×65mm and the density is not less than 3.05g.cm-3. The green body is dried by a tunnel dryer at a temperature not lower than 120℃, loaded with bricks in the width direction as the compression direction, and sent to a 110m ultra-high temperature natural gas tunnel kiln. It is fired at four different temperatures and kept for 6 hours.
The Physical and Chemical Indexes of Magnesia Alumina Zirconia Brick
Item | MAZ-90A | MAZ-90B |
Magnesia Alumina Zirconia Bricks | ||
MgO % | 90 | 85 |
Al₂O₃ % | 5 | 5 |
SiO₂ % | 1.0 | 2.0 |
ZrO₂ % | 1-3 | 1-3 |
Cr₂O₃ % | – | – |
Apparent porosity % | 18 | 18 |
Bulk Density g/cm³ | 2.95 | 2.9 |
Cold Crushing Strength Mpa | 50 | 50 |
Refractoriness under load of 0.2Mpa(℃) | 1700 | 1700 |
Thermal shock resistance
(1100℃ water quenching cycle)> |
9 | 8 |
Thermal Conductivity (1000℃) W/m.k | 3.4 | – |
Thermal Expansion Rate (1400℃) % | – | – |
Magnesia Alumina Zirconia Brick Fused Cast Refractories
Magnesia-alumina-zirconia fusion refractory is made of light-burned magnesia powder, fused magnesia powder, aluminum powder, and zirconia oxychloride powder by heating and melting. After testing, the refractoriness can reach 2600-2800℃, the strength is 300MPa, the bulk density is 3.5g/cm3, the porosity is close to zero, and the thermal shock stability is also high. This product is used for steelmaking furnace lining, which can increase the service life of magnesia carbon brick by more than ten times. Maintenance is reduced, turnover is accelerated, the output is increased, quality is improved, and costs are reduced. Using this refractory material for converter lining can reduce the 100-ton converter lining brick from 335 tons to 155 tons, double the output, and the benefits are extremely significant. Using the refractory material as the furnace lining can reduce the inclusions in molten steel by 90% and improve the quality significantly. The refractory material can be used for converter lining, ladle lining, tundish lining, tapping opening, and series of functional components, such as sliding water outlet.
Magnesia Alumina Zirconia Composite Brick for the Nickel-iron Rotary Kiln
The rotary kiln requires a high temperature for the direct reduction of nickel. Most of the materials in the high-temperature zone are in a semi-melted or fully molten state and have the characteristics of high slag content, low viscosity, and large fluctuations. As a result, the working environment of refractory materials in the kiln is very harsh. At present, the service life of alumina-chrome bricks and magnesia-chrome bricks used in the market is short, and there are serious chrome pollution problems. Combining the characteristics of working conditions in the high-temperature zone of the nickel-iron rotary kiln and the damage mechanism of refractory bricks, a new type of magnesia-alumina-zirconia composite brick was developed. The magnesia-aluminum-zirconia composite brick realizes the complementary advantages of the magnesia-zirconia brick and the magnesia-aluminum-spinel brick by introducing a zirconia source into the magnesia-aluminum-spinel brick. It has low porosity, good room temperature, high-temperature mechanical properties, excellent thermal shock resistance, and alkali slag corrosion resistance. The application of multiple rotary kilns proves that the use effect is good. It is a new high-performance long-life chrome-free refractory product suitable for use in the high-temperature zone of nickel-iron rotary kiln.
Magnesia Alumina Zirconia Bricks for Non-ferrous Industry
Using fused magnesia, high-purity magnesia, and magnesia-rich fused spinel as raw materials, adding appropriate ZrO2, using inorganic composite binders, a new type of magnesia alumina-zirconia brick was prepared. The results show that the MgO-based composite spinel brick with 2% (w) desiliconized zirconia has good slag corrosion resistance, thermal shock resistance, and mechanical properties. It is expected to become a substitute for magnesia-chrome refractories for non-ferrous smelting.
Rongsheng Refractory Bricks Manufacturer
Rongsheng is a refractory bricks manufacturer with rich production and sales experience. Provide customers with high-quality refractory materials, solve the problem of refractory lining of thermal equipment, and save customers the greatest possible production cost. Rongsheng’s refractory projects have spread to more than 60 countries around the world, for example, Thailand, UAE, Turkey, Kuwait, South Africa, Malaysia, Vietnam, Netherlands, Philippines, Singapore, Egypt, Russia, etc. For more information about Rongsheng refractory bricks manufacturers, or if you want to purchase refractory materials products, please contact us. We will provide you with services according to your specific needs.