In the 21st century, SiC series silica mullite bricks based on Al2O3 appeared in China. In some pre calcining kilns, the use of the transition zone (the back end of the upper transition zone) and the decomposition zone where the kiln material melt appears has achieved better results. A number of varieties have been formed, and their representative products are silica mullite brick (Al2O3>60) and silica mullite red brick (Al2O3>65). Freely to get more details by email.
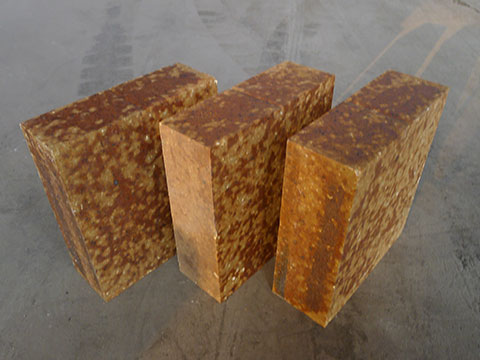
Application characteristics of SiC series silica bricks
The advantages of silica mullite red brick are uniform expansion, good thermal shock stability, high load softening point temperature, and the low high temperature creeps value. It also has the characteristics of high hardness and strong chemical resistance. It has been widely used in some pre calcining kilns with low alkali sulfur content in some kiln materials. Its advantage is that the thermal conductivity is lower than that of magnesia alkaline bricks, the temperature of the cylinder is lower, the heat dissipation loss is less, and the price is also lower. However, the high-temperature part is limited because the softening temperature is lower than that of alkaline bricks.
Judging from the actual production situation, the silica mullite red brick is mainly composed of mullite, and the temperature of the working condition is subject to certain restrictions. The stability requirements for production operations should be minimized as much as possible to reduce the excessive temperature caused by the fluctuation of raw fuel composition and the change of working conditions to cause large-scale damage to the lining brick. Another point is the content of SiC in the silica mullite brick. Generally speaking, the content of SiC in silica mullite brick is about 6%, which has a certain strength of alkali corrosion resistance. The disadvantage is that the temperature of the cylinder is high and the heat dissipation loss is large. But judging from the temperature of the upper cylinder of a 5000t/d-class kiln that uses silica mullite red bricks and silica mullite bricks. The surface temperature of the cylinder body where the silica-molded red brick is set between 32.3~45.7m from the kiln mouth is 310~345℃ (mostly more than 320℃), and the silica-molded brick with a lower flue gas temperature is 45.7~58m from the kiln mouth. The temperature of the cylinder exceeds 360℃. It shows that the SiC content of the silica mullite brick is lower than that of the silica mullite brick, and the thermal conductivity is also lower.
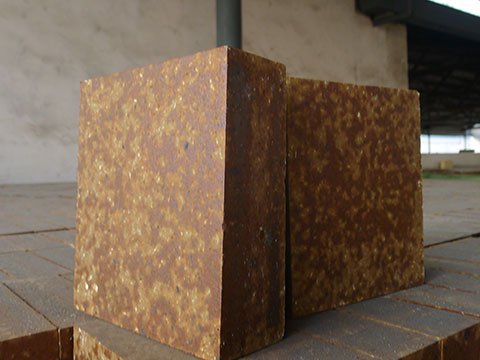
In another case, when the cement kiln is in production, the loop formation and long thick kiln skin after the alkali-sulfur circulation occurs are located at 39-44m. However, the silica mullite bricks with low SiC content are difficult to withstand the corrosion of sulfur alkali for a long time. The sulfur and alkali in the raw fuel of the kiln are all within the specified requirements. In addition, the temperature of the cylinder caused by the silica mullite brick exceeds 350℃, which will increase the heat dissipation loss of the cylinder. Of course, a kiln can only illustrate a trend, but not a complete description of the problem. During the production operation, the temperature of the cylinder changes with changes in process equipment and raw fuel properties. The emergence of a kind of lining brick can only be used under a large number of different working conditions, and it is optimized and improved during use. At the same time, the heat dissipation of the cylinder and other materials should be compared with other materials, and then a realistic view can be obtained. Compared with the above two kinds of bricks, in addition to the advantages of silica mullite series bricks, aluminum-carbon wear-resistant bricks have more advantages in wear resistance and low thermal conductivity.
In order to reduce the heat dissipation loss of the cylinder body caused by the high temperature of the rotary kiln cylinder body when the silica mullite brick is used. Use a variety of specifications of high-aluminum clinker and a small amount of silicon carbide, and add an appropriate amount of porous clinker and alumina hollow balls. The added silicon carbide can significantly improve the wear resistance and corrosion resistance of the refractory bricks, and the hollow alumina spheres and porous clinker can significantly reduce the bulk density and thermal conductivity of the refractory bricks. The highest control temperature for calcination is 1350~1400℃. The temperature physical properties of the manufactured low thermal conductivity wear-resistant bricks are: normal temperature wear ≤8.7cm3, thermal conductivity at 800°C of hot surface ≤1.25W/(m.K). It can be used in the low-temperature part and decomposition zone of the transition zone of the rotary kiln. Such products are in line with the development direction of energy saving, but the ability to resist alkali and sulfur corrosion needs further practice.
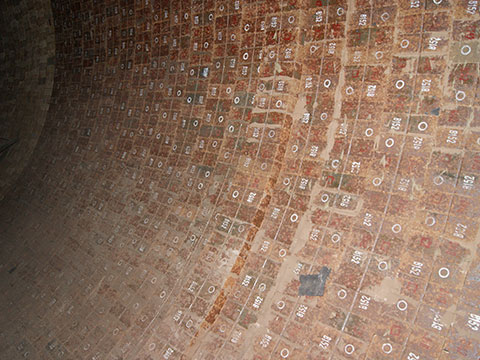
Characteristics of SiC Series Silica Mullite Bricks
SiC Series Silica Mullite Bricks can withstand higher temperatures than alkali-resistant materials with SiO2 as the main component, and have stronger wear resistance and excellent skinning resistance. This type of refractory is used for the higher temperature parts of the firing system. Laboratory experiments have confirmed that in the silica-alumina series products when the SiC content is about 5% to 32%, a highly viscous protective layer will be formed during the production process. Therefore, the content of SiC to prevent alkali corrosion for the production of cement clinker calcination is mostly within this range.
The advantages and disadvantages of refractory bricks used in cement kilns
There are several types of refractory bricks commonly used in cement kilns. The following is a brief introduction to the disadvantages of these refractory bricks.
- Dolomite bricks have good kiln-hanging performance and good corrosion resistance. But it is easy to hydrate, difficult to transport and store, and it is less used in production.
- Magnesia chrome bricks are good for hanging kiln skins and are mostly used for firing zones. The disadvantage is poor thermal shock resistance.
- Phosphate bricks have low refractoriness, but high strength and good thermal shock. It is mostly used for kiln head cover etc.
- Silicon carbide brick, high-temperature resistance, about 1800 degrees, load softening temperature in 1620-1640. The coefficient of thermal expansion is small, and the abrasion resistance of rapid cold and rapid heat is good, suitable for the cooling zone and kiln mouth.
- Silica brick has good thermal shock resistance, high strength, good wear resistance, suitable for excessive belting.
- Spinel bricks are mostly used for transition zones. Good seismic performance and reduction resistance. But the refractoriness is slightly worse.
- High alumina bricks, with Al2O3 content greater than 75, higher refractoriness than clay bricks, and good resistance to acid and alkali corrosion. Suitable for cement kiln burning zone, etc., with long service life but high price.
- Anti-stripping brick, this brick contains a small amount of ZrO, and Markov phase transformation occurs during the heating-process to form fine cracks. It has strong alkali resistance, good peeling resistance, and slag resistance.
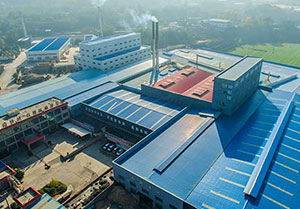
Rongsheng refractory brick manufacturer
Rongsheng refractory brick manufacturer has rich experience in the production and sales of refractory bricks. Rongsheng’s refractory products have been recognized by customers in more than 60 countries around the world. For example, Thailand, UAE, Turkey, Kuwait, South Africa, Malaysia, Vietnam, Netherlands, Philippines, Singapore, Egypt, Russia, etc. Rongsheng’s hot-selling products include magnesia bricks, magnesia-chrome bricks, silica mullite bricks, SiC series silica mullite bricks, etc., which are very suitable for refractory lining materials for cement kilns. For more product information and prices, please contact us. We will provide you with services according to your specific needs.