Alumina Bubble Bricks are heat-insulating refractory products made of alumina hollow balls as the main raw material. They are mainly used in the lining of high-temperature industrial kilns below 1700°C and the insulation layer of thermal equipment of high-temperature thermal equipment. The method of making alumina hollow ball bricks is to add alumina raw materials into a dumping electric furnace and melt them into a liquid. Then the furnace is tilted at a certain angle to make the solution flow out of the pouring trough at a corresponding speed, and the liquid flows through a flat nozzle with a 60°-90° angle with the flow. Alumina hollow balls are blown away and formed by a high-speed airflow with a pressure of 0.6-0.8MPa. Alumina hollow balls, sintered alumina fine powder, and binder are then mixed, formed, dried, and fired, and Alumina Bubble Bricks are obtained according to a certain proportion.
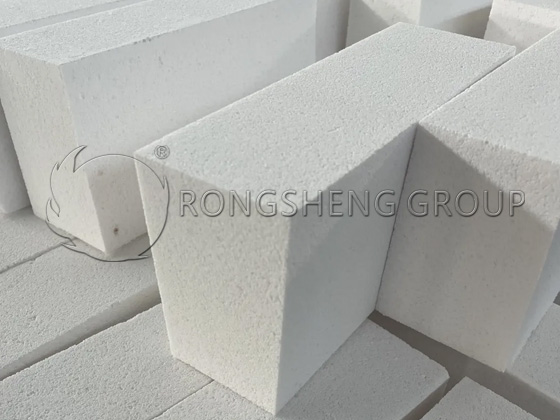
High Temperature Insulation Alumina Bubble Brick
Alumina Bubble Bricks is a new type of high-temperature insulation material with the following advantages:
High operating temperature: up to 1750 degrees or more, good thermal stability, small reburning line change rate, and longer use.
Optimize structure and reduce furnace weight: High temperature resistant materials are now heavy bricks with a volume density of 2.6-3.0g/cm³. Alumina Bubble Bricks are only 1.1-1.5g/cm³. For the same cubic meter volume, the use of alumina hollow ball bricks can reduce 1.1-1.9 tons of weight.
Save materials: To achieve the same operating temperature, if heavy bricks are used, the price is comparable to that of Alumina Bubble Bricks, and considerable insulation layer refractory materials are required. If alumina hollow ball bricks are used, 1.1-1.9 tons of heavy bricks can be saved per cubic meter, and 80% of refractory insulation materials can be saved.
Energy saving: Alumina hollow balls have obvious heat preservation properties and low thermal conductivity, which can achieve a good heat preservation effect. It can reduce heat dissipation and improve thermal efficiency, thus achieving the purpose of energy saving. The energy saving effect can reach more than 30%.
Physical Properties of Alumina Bubble Bricks
α-Al₂O₃ content: α-Al₂O₃ content in alumina reflects the degree of alumina roasting. The higher the degree of roasting, the more the α-Al₂O₃ content. The hygroscopicity of alumina deteriorates with the increase of α-Al₂O₃ content. Therefore, alumina used for electrolysis requires a certain amount of α-Al₂O₃. However, the solubility of α-Al₂O₃ in electrolyte is worse than that of Υ-Al₂0₃.
Bulk density: The bulk density of alumina refers to the weight of a unit volume of material in a natural state. Usually, alumina with a small bulk density is conducive to dissolution in the electrolyte.
Particle size: The particle size of alumina refers to its coarseness. The particle size of alumina must be appropriate. If it is too coarse, it will dissolve slowly in the electrolyte and even precipitate. If it is too fine, it will easily fly and lose.
Specific surface area: The specific surface area of alumina refers to the total surface area of the material per unit weight and the sum of the surface area of the inner pores. It is an important indicator of the activity of a substance. Alumina with a large specific surface area has good solubility in electrolytes and high activity, but is easy to absorb moisture.
Wear coefficient: The so-called wear coefficient is the percentage change in the particle size content in the sample after alumina is rubbed on a fluidized bed under certain conditions. The wear coefficient is a physical indicator that characterizes the strength of alumina.
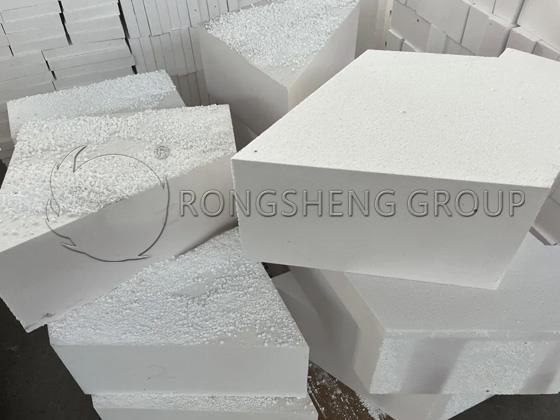
Application of Alumina Bubble Bricks in High-Temperature Kiln Equipment
Lightweight refractory materials have the advantages of low density, low thermal conductivity, and small linear changes after reburning. They can fully reduce the construction cost of thermal equipment such as industrial kilns, reduce the heat loss of kilns, and are widely used in the insulation layer of high-temperature kiln equipment. Among them, alumina hollow balls are an ideal lightweight aggregate, which has important practical significance for the use of Alumina Bubble Bricks and castables made of alumina hollow balls.
Alumina Bubble Bricks use alumina hollow balls as the main material, corundum ultrafine powder as an additive, and organic matter as a binder. Alumina hollow ball bricks are formed and dried and fired in a high-temperature kiln at 1750℃, which belongs to the category of lightweight corundum insulation bricks.
This material has the characteristics of low thermal conductivity and high compressive strength of insulation bricks. It can be used as a lightweight insulation brick normally at 1700℃. Alumina Bubble Bricks have excellent high-temperature resistance and thermal insulation performance. They can be directly used for the working lining of high-temperature kilns, and have achieved significant results in reducing the weight of the furnace body, modifying the structure, saving materials, and saving energy.
The research and development of alumina hollow ball bricks and their application in industrial kilns and equipment have greatly improved some shortcomings of lightweight thermal insulation materials. Although the refractory properties of commonly used refractory bricks such as high alumina bricks, silicon carbide bricks, and clay refractory bricks exceed 1700℃, their thermal conductivity is too high and they are not suitable as insulation layers, so they can only be used as refractory layers. The insulation layer of most kilns usually uses insulation bricks or insulation materials, which not only increases the thickness of the masonry, but also increases the risk of use, and the long-term operation of the furnace lining is not ideal. If light insulation materials are directly selected as refractory materials for kiln and equipment linings, the load softening temperature and acid and alkali corrosion resistance of light insulation materials need to be fully considered. The long-term use temperature of insulation materials generally does not exceed 1200℃, and the compressive strength is relatively poor, generally 3-5MPa, and the acid and alkali erosion resistance effect is not ideal. Therefore, the use of lightweight insulation materials alone can be masonry in low-temperature kilns without pressure and chemical erosion, and high-temperature kilns must be built with refractory bricks. The manufacturing and production of Alumina Bubble Bricks not only solves the problem of high thermal conductivity, but also solves the problem of use temperature and compressive strength in lightweight insulation materials. It has been well verified in high-temperature energy-saving downdraft kilns, shuttle kilns, molybdenum wire furnaces, tungsten rod furnaces, induction furnaces, nitriding furnaces, and other equipment.