Carburizing refers to the process of infiltrating carbon atoms into the surface layer of a workpiece. Gas carburizing is a carburizing process in which the workpiece is placed in a closed carburizing furnace, and a gaseous infiltrant (methane, ethane, etc.) or liquid infiltrant alcohol, acetone, etc. is introduced to decompose active carbon atoms at high temperature and infiltrate the workpiece surface to obtain a high-carbon surface layer. Nut carburizing technology is a common heat treatment process, especially with good mechanical properties under heavy pressure, impact, corrosion, etc. Surface carburizing technology can effectively improve the corrosion resistance, oxidation resistance and contact fatigue strength of nuts.
The long-term operating temperature of the nut carburizing furnace production line is 930℃, and the carburizing process uses methanol atmosphere as carrier gas and acetone as enriched gas. Carburizing in a nitrogen-methanol atmosphere cleans the surface of the parts, and the surface carbon concentration can be ideally infiltrated into the surface tissue, which is beneficial to strengthen the surface. Due to the reducing atmosphere of the carburizing furnace, the structure using traditional high-temperature refractory fiber modules as the furnace lining is very likely to cause high-temperature pulverization of the fiber, thereby affecting the thermal insulation performance in the furnace. The problem of fiber high-temperature pulverization can be solved by simply using insulation bricks to build furnace linings. However, due to the inherent disadvantages of insulation bricks, such as large heat storage capacity and high thermal conductivity, the heating power of the heating furnace will be too large and the heating time will be slow. In order to solve the above problems, impermeable silicon carbide bricks were selected and they were used continuously for 2 years in a reducing atmosphere and the production was normal. However, the silicon carbide bricks used recently have whitened surfaces during use, so further analysis is required.
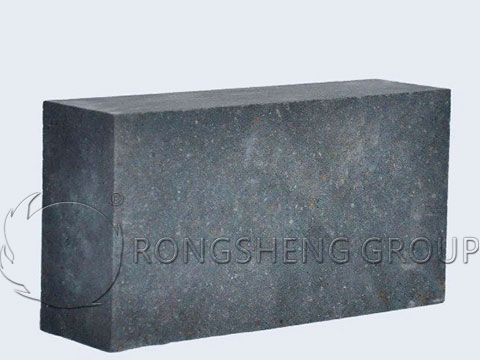
The First Aspect of Silicon Carbide Bricks Being Damaged
The carburizing furnace is a cylindrical cross-section furnace. High-temperature radiation tubes are used on both sides of the furnace to heat the workpiece in the furnace. Its maximum working temperature is 930℃. In this carburizing atmosphere, the following reactions mainly occur in the furnace:
CH3OH→CO+2H2
CH3COCH3+H2→CH3—CH—COOH|OH
Both C and H2 have strong reducing properties, which can easily lead to the reduction of iron oxides in silicon carbide bricks, produce new substances such as Fe, Fe3C, C (carbon black), and expand the volume, thereby causing masonry damage. This is also the first reason why the surface of silicon carbide bricks turns white when used.
SiC + 2CO→SiO2 + 3C
The Second Aspect of Silicon Carbide Brick Damage
The production of silicon carbide bricks involves selecting silicon carbide raw materials with a SiC content of more than 90%, adding a binder, and sintering at high temperature. It has high strength and thermal conductivity, but the disadvantage is that it is easy to oxidize and difficult to use in an oxidizing atmosphere. Although the oxidation product of SiC, the SiO2 protective film, can prevent further oxidation, at about 800℃-1140℃, the SiO2 film will change in volume due to phase change, making its structure loose and the oxidation protection effect suddenly reduced. In addition, under certain conditions, the SiO2 protective film cannot be formed. This will lead to a decrease in the performance of silicon carbide materials and affect their service life. Based on the loose structure of the white surface of the silicon carbide bricks damaged on site, it can be determined that it is secondary oxidation in a reducing atmosphere. Although the working principle of the carburizing furnace is a reducing atmosphere, it can be concluded from the above viewpoints that the CO and H2 in the carburizing furnace atmosphere come from the decomposed fuel, and then react with the SiC of the silicon carbide bricks to form SiO2 in the form of gas and leave the silicon carbide bricks. The following is the reaction formula:
SiC + 2CO→SiO2 + 3C
If the temperature is high enough or the oxygen partial pressure is low, SiC will be converted into volatile SiO2 and corroded by the environment. This will cause the silicon carbide material to be rapidly oxidized, that is, active oxidation will be produced.
In summary, ① In order to prevent the generation of new substances such as Fe, FeC, and C (carbon black) in the furnace lining, anti-carburization refractory materials with very low FeO content and very little S content must be used in the selection of furnace lining materials. ② In the working atmosphere of the carburizing furnace, try not to use easily oxidized silicon carbide bricks instead of products with low thermal conductivity and good thermal insulation performance, such as lightweight corundum bricks or alumina hollow ball bricks.