With the improvement of environmental awareness and standards, refractory bricks for cement kilns have been replaced by magnesia-iron spinel refractory bricks instead of direct-bonded magnesia-chrome refractory bricks to reduce the impact of Cr6+ on the environment. However, compared with direct-bonded magnesia-chrome bricks, magnesia-iron spinel bricks have disadvantages such as high thermal conductivity and poor kiln skin performance, resulting in problems such as short service life, high cylinder temperature and red kiln. After continuous adjustment and optimization, the firing zone magnesia-iron-aluminum spinel bricks have achieved a safe operation performance of 2 years. RS Refractory Brick Manufacturer, supplying high-quality refractory brick lining materials for cement kilns, contact Rongsheng for detailed information.
A brief description of the use of refractory bricks in a rotary kiln
The Φ4.6m×68m rotary kiln with a 4000t/d clinker production line is equipped with three types of cement kiln refractory bricks: magnesia-alumina spinel, magnesia-iron spinel and silica-molybdenum bricks. Amorphous refractory materials are used at the kiln mouth and kiln tail. Magnesia-alumina spinel and magnesia-iron spinel are used in the firing zone to replace directly bonded magnesia-chrome bricks. Compared with the two, magnesia-alumina spinel and magnesia-iron spinel have poor kiln skin performance and high thermal conductivity. In production, high-temperature spots often appear in the firing zone refractory bricks after 6 to 8 months of use, concentrated at both ends of the firing zone, 0.8 to 3m and 18 to 23m away from the kiln mouth. Every year, digging and patching are required to barely maintain the annual overhaul, affecting the continuous operation of the kiln.
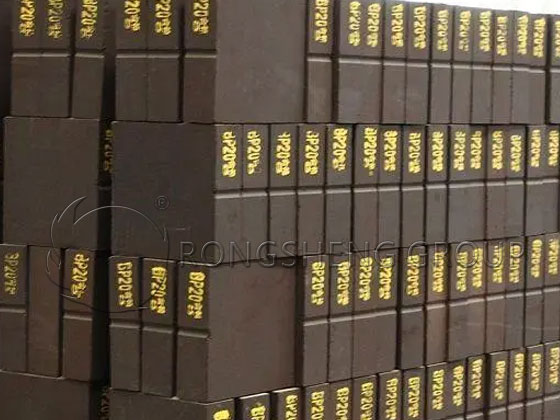
Analysis of problems with refractory brick lining of rotary kiln
-
Analysis of the cause of damage at 0.8~3m of kiln mouth
Every time the kiln mouth has high temperature and the red kiln is shut down for maintenance, it is found that the kiln skin here is a thin layer, and the overall refractory bricks are severely peeled off, generally about 5cm. There are even no bricks in some parts, and the cylinder is visible without dislocation. Analysis shows that this place is located at the junction of the burning zone and the cooling zone, the temperature fluctuates greatly, the kiln skin is unstable, and it rises and falls frequently. In addition, the wear of the kiln clinker causes the refractory bricks to peel off and damage, and the bricks need to be adjusted.
-
Analysis of the cause of damage at 18~23m
Because the magnesium oxide content of limestone in the mine is high, the average magnesium oxide content of clinker is about 5.0%. The liquid phase volume of clinker reaches 29.29%, and the crust value reaches 40.82%, both exceeding the upper limit of the optimal control value (the upper limits are 26% and 37% respectively). The kiln has thick kiln skin and ring formation at 16~17m. This is located in the post-firing zone, where the temperature is relatively low and the kiln skin is not very stable. In addition, there is a ring in front, and the wear of clinker here exacerbates the damage of refractory bricks.
Measures taken
Considering that the current situation of high magnesium oxide in limestone in mines cannot be improved, the optimization of brick matching and brick indexes should be formulated based on the performance of magnesia-alumina spinel and magnesia-iron spinel refractory bricks. The measures are as follows.
One kiln one design, optimize brick matching, and give full play to the performance of various types of refractory materials
According to the actual brick matching situation of customers who have used refractory manufacturers for a long time, the brick matching in the kiln was adjusted. Magnesia-alumina spinel bricks at the kiln mouth were replaced with silica-molybdenum bricks 1680 and magnesia-iron spinel bricks. Combined with the high magnesium oxide of clinker, the kiln skin is unstable. In addition, the performance of magnesia-iron spinel bricks hanging on the kiln skin is not as good as that of directly combined magnesia-chrome bricks, and the fired zone bricks are reduced by 1m. Considering energy saving, low thermal conductivity and anti-stripping refractory bricks are used in the rear transition zone. At the same time, some physical and chemical indicators of magnesia-iron spinel bricks have been partially adjusted, and magnesia-iron spinel refractory bricks are recommended. Taking into account the advantages of magnesia-iron spinel and magnesia-alumina spinel, the performance foundation of hanging kiln skin is guaranteed, and the strength and wear resistance of bricks are improved.
The kiln mouth and kiln tail kiln mouth castables are 0.8m~2.4m (silicon-molybdenum bricks 1680) with a brick ring size of 40×60mm, a spacing of 15mm, and are composed of 12 sections. There are 94 rings of magnesia-iron-aluminum spinel bricks, 18.8m (3.2~22m) F3∶MF4=87∶10; there are 95 rings of silicon-molybdenum bricks 1680, 19m (22~41m) MF1∶MF238m; there are 131 rings of low thermal conductivity anti-stripping bricks, 26.2m (41~67.2m) AM1∶AM2=47∶91; the kiln tail castable is 0.79m.
Optimize the batching scheme, promote the flatness of the kiln skin, and enhance the performance of the kiln skin
The quality of the kiln skin determines the service life of the refractory bricks in the firing zone. Under the protection of the kiln skin of normal thickness, the surface temperature of the alkaline bricks can be reduced from 1400~1450 ℃ to 600~700 ℃. The lining bricks are in a safe state, and even the kiln skin with a thickness of only 23mm can reduce the brick surface temperature from 1450 ℃ to about 1230 ℃. Under the protection of the kiln skin, the temperature gradient in the alkaline bricks is significantly gentle, the infiltration layer in the bricks is significantly thinner, and the deterioration and damage of the bricks are also light.
The amount of clinker liquid phase is the basic factor in the formation of the kiln skin. The melting of C2S promotes the increase of the kiln skin strength. Fe2O3 can significantly reduce the sintering temperature and liquid phase viscosity. All three promote the formation of the kiln skin. When the crust value is <30%, the kiln skin is often difficult to form. When the crust value is 33%~37%, the kiln skin is easier to form. When the crust value is >40%, large lumps and rings will be formed. The crust value can be calculated by the following formula: crust value = liquid phase amount + 0.2C2S + 2Fe2O3. It can be seen that Fe2O3 in clinker has a dual effect. Reducing the Fe2O3 component can reduce the liquid phase amount and the crust value at the same time. It is also easier to adjust the ingredients and has strong operability. Therefore, a low-iron ingredient scheme is adopted, and the crust value is controlled in the middle value of the interval (35.43%).
Formulate a cooling curve
The cement industry has formulated a heating curve for heating, but less attention is paid to cooling. From the crust value formula, it can be seen that C2S is the key to promoting the strength of the kiln lining. However, C2S minerals have a crystal transformation. When cooling slowly at 400~600 ℃, it is easy to transform into γ type, destroy the kiln lining, and cause the refractory bricks to peel off. Therefore, when temporarily shutting down, pay attention to the cooling rate in this interval, formulate a cooling curve, protect the kiln lining, and extend the service life of the bricks.
The purpose of the cooling curve is to control the cooling rate, prevent the transition zone silicon-molybdenum bricks from peeling off and the kiln lining from falling off, which causes the magnesia-iron-aluminum spinel bricks to peel off, thereby promoting the service life.
Maintenance of kiln mouth castable
The kiln mouth castable is in contact with the first row of silicon-molybdenum bricks. It was found in production that when the kiln mouth castable is damaged, the first row of silicon-molybdenum brick castable side will peel off in a short time, and even faults and broken corners will occur, resulting in the shutdown of the red kiln. Damage to the kiln mouth castable often causes the entire diameter to fall off, and no residual rake nails are found at the falling off. After analysis, it is believed that some rake nails are not welded firmly, or the welding rod has been on site for a long time, and absorbs water after drying, causing the local castable to fall off, and the surrounding castables to fall off. Therefore, a new rake nail structure and castable open construction process are adopted.
The rake nails are composed of a block base and a U-shaped steel bar, both of which are made of heat-resistant steel, and the block base is fully welded. Compared with the original rake nails, the welding surface is increased and more solid. The U-shaped steel bar is inserted into the central circular hole of the block base, spot welded and connected to eliminate stress. The kiln radial circumference is divided into 24 equal parts, 600mm spacing, fixed with steel plates on both sides, and pouring kiln mouth castables. After pouring and initial setting, exhaust holes are arranged on the working surface, and then insulation and maintenance are carried out. After completion, the next piece of construction is carried out, and so on. The open construction process, although the progress is slow and the surface is uneven. However, from the production practice, there has been no whole ring falling off in one year of use, and the quality is good.
Maintenance of coal injection pipe
The coal injection pipe has a great impact on the kiln bricks, and two accidents have occurred. One is that the size of the spare parts of the internal cyclone head of the manufacturer is deviated, resulting in too fast internal wind speed, scattered flames, and deep grooves around the kiln silicon bricks. The other is that there are three large-scale deep pits in the kiln silicon bricks. Analysis shows that the ratio of internal and external wind is improper, the flame is unstable, and it is weak and floating. It may also be improper positioning. It is recommended that the position of the coal pipe and the shape of the flame should be based on the premise of ensuring the safe operation of the refractory bricks. It is advisable to make conservative fine adjustments as much as possible, start with details, and carefully maintain to extend the life of the refractory bricks.
Before opening the kiln, it is necessary to keep the end face of the coal pipe clean, measure and verify its size, check the flatness of the end face castable, and the positioning data must be accurate. The correspondence between the position in the kiln and the scale of the external (X and Y axis) of the coal pipe should be recorded and marked. During operation, the coal injection pipe must be cleaned of coking on the end face once per shift to stabilize the flame shape. Clean the accumulated material on the upper part of the coal injection pipe and the beard on the lower part to prevent the head from bending and deforming for a long time and changing the direction of the flame.
On the whole, the use of magnesia-iron-aluminum spinel refractory bricks takes into account the advantages of magnesia-iron spinel and magnesia-iron spinel, and increases the strength and wear resistance of the bricks while keeping the kiln skin performance unchanged. Optimizing the physical quality of bricks and the brick matching in the kiln is the basis, and the maintenance of the kiln skin is the key. In daily production, attention should be paid to the crust value to ensure that the kiln skin is flat and avoid process accidents such as ring formation and egg formation. At the same time, attention should be paid to the heating and cooling process, as well as the operating status of the castable and coal pipe. Starting with details and careful maintenance can increase the service life of the refractory bricks in the kiln firing zone.
Advantages of Magnesia-Fe-Spinel Bricks in Cement Kilns
Magnesia-Fe-Spinel Bricks have the advantages of chromium-free environmental protection, good thermal shock stability, good “kiln skin” hanging ability, good erosion resistance, low thermal expansion and low thermal conductivity, and good structural flexibility. In actual application, the service life of this brick exceeds 1 year, the kiln skin is hung quickly after firing, the kiln skin thickness is uniform and stable, and there is no large collapse of refractory bricks. There is no refractory brick peeling when the kiln is stopped, the kiln body temperature is low, and the heat energy loss is small. Compared with similar products, the magnesia-Fe-Spinel Bricks of RS Refractory Brick Manufacturer have the advantages of short order cycle, low price, small spare quantity, and convenient after-sales service.