Refractory bricks, as furnace lining materials at high temperatures, from a chemical point of view, all single substances and compounds with high melting points can be used as raw materials for their production. From a mineralogical point of view, all minerals with high refractoriness can also be used as raw materials. So the finished product is called refractory bricks. Common refractory bricks have different shapes, and the strange shapes can be formed by raw material blending and mold making. The different brick sizes of refractory brick products have different effects. Rongsheng Refractory Bricks Factory is a powerful manufacturer and seller of refractory materials. For customized refractory bricks 230*114*40, please contact Rongsheng.
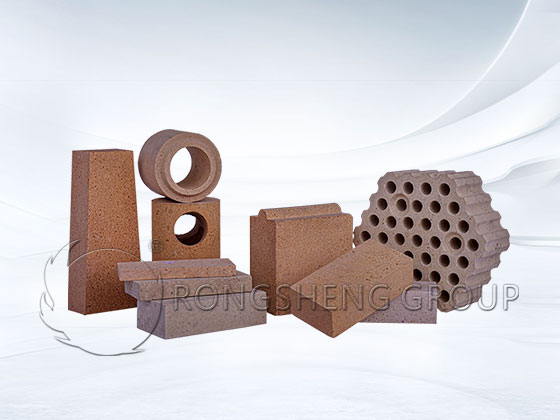
Types and Sizes of Refractory Bricks
The types of refractory bricks are classified by material, including clay refractory bricks, high alumina bricks, silica bricks, magnesia bricks, magnesia-chrome bricks, high alumina lightweight bricks, etc. According to shape, they include straight bricks, thick wedge-shaped bricks, vertical thick wedge-shaped bricks, vertical wide wedge-shaped bricks, arch foot bricks, etc. According to specification type, they are divided into standard, general, special and special refractory bricks.
The sizes of refractory bricks include standard refractory bricks, usually 230mm×114mm×65mm. For general refractory bricks, the external dimensions are within the range of 1:4, the unit weight of clay bricks is 2-8kg, silica bricks are 2-6kg, high alumina bricks are 2-10kg, and magnesia or magnesia-alumina bricks are 4-10kg. For special-shaped refractory bricks, the external dimensions of clay and high alumina special-shaped bricks are within the range of 1:6, and the weight is 2-15kg; the external dimensions of silica special-shaped bricks are within the range of 1:5, and the weight is 2-12kg. Special refractory bricks, clay, high alumina special bricks, the size ratio is within the range of 1:8, weight 1.5-30kg; silica special bricks, the size ratio is within the range of 1:6, weight 1.5-25kg. Other common sizes: 250mm×123mm×65mm, 230mm×113mm×55mm-65mm, 250mm×123mm×55mm-65mm, 114×65/35×230mm, 132×114×230×33mm, etc.
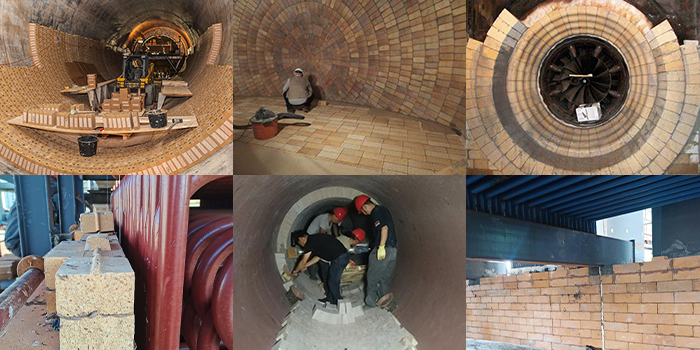
Different Use Effects of Different Brick Shapes and Sizes of Refractory Bricks
The brick type of refractory bricks used in the lining of high-temperature kilns is very important. If it is too small, the mortar joints are large and numerous, and the insulation effect is reduced. If it is too large, although there are fewer mortar joints, the brick type is too large, the thermal expansion coefficient will be large, and the refractory bricks will break and fall off in a large area.
The weight of refractory bricks exceeds 15kg. During use, the brick body will expand or shrink in a large proportion under the unstable factors of heating and cooling, and the internal thermal stress will also change continuously. When the brick shape is too large, the stress cannot be released in time, and microcracks will occur. After long-term stress, the microcracks will continue to expand and increase, and the brick body will crack, which can easily cause the refractory bricks to fall off.
If the length, width and thickness of the refractory bricks are reduced, the weight will be reduced by about 4-6 kg, although the number of mortar joints will increase during masonry. However, due to the small brick type, the thermal stress generated inside the brick body is small, and the brick joints are released, which buffers the stress concentration and reduces the possibility of crack formation.
Therefore, the size of the refractory brick shape should be determined according to the size of the furnace lining. Moreover, no matter what material of refractory bricks is used for the size of the furnace lining, the appropriate brick type is the best and most applicable.
For example, the roof bricks of the furnace lining are made of appropriate weight, and then the roof bricks are produced into buckle bricks. In this way, the flat bricks are meshed with each other, which increases the friction between the bricks and reduces the sinking of the roof bricks. Even if the bricks are broken, the refractory bricks are tightly meshed, and the broken bricks cannot slip, so the broken bricks will not fall off.
The size of refractory bricks has different effects, but when constructing masonry, staggered masonry should be used, and the straight seams should be changed to curved brick seams. This avoids the flow of flame straight seams in the furnace lining, which can reduce fire leakage and increase the service life of refractory bricks.
How to Choose the Right Refractory Bricks for Kiln Lining?
- Choose according to the working temperature of ±100℃, focusing on matching RUL and thermal shock performance.
- Use “thin seam + flexible filler” technology to control the brick seam to 1-2mm.
- Set a “transition layer” between different bricks, such as adding sillimanite bricks between high-alumina bricks and carbon bricks.
Rongsheng Refractory Brick Manufacturer
Rongsheng Refractory Brick Manufacturer is a refractory material manufacturer with rich experience in production, sales, and construction. Rongsheng Refractory Manufacturer’s furnace lining material products have been sold to more than 120 countries and regions around the world. Rongsheng Refractory Manufacturer’s refractory material products, including various refractory brick shapes, can be customized according to actual high-temperature working conditions. Welcome to consult Rongsheng Manufacturer’s refractory brick products, and look forward to establishing a cooperative relationship with you.