The characteristics of andalusite are obvious. Mulliteization temperature is low; thermal expansion during conversion is low. The crystals are coarse and can be used as aggregate. All these characteristics allow andalusite to be directly used to make fired or unfired refractory bricks without calcination and save a lot of energy. Through a series of Applications of Andalusite Bricks, Rongsheng Refractory Bricks Factory discovered the advantages of Andalusite refractory bricks and their application advantages in industrial furnaces.
Advantages and Characteristics of Andalusite Refractory Bricks
- It has strong creep resistance. Creep is a measure of the ability of refractory bricks to resist high-temperature loads for a long time. Melt impurities that can cause premature softening of refractory bricks have a huge impact on creep. Even high-quality dense clay bricks will contain about 5% Fe2O3, TiO2, R2O, etc. Andalusite refractory bricks contain less melt impurities. Therefore, the creep value for 25 hours under the conditions of 1300℃/0.2MPa is 0.28%. It is only 20% to 25% of the clay brick containing 42%, which is lower than the bauxite high-alumina brick containing 85% Al2O3.
- Another characteristic of andalusite refractory bricks is that it has higher high-temperature strength and less decrease with increasing temperature. High-temperature strength is related to the amount of liquid phase formed inside the refractory brick at high temperatures.
- In addition, andalusite refractory bricks also have good high-temperature volume stability and thermal shock stability. Compared with other Al2O3-SiO2 series refractory bricks with the same Al2O3 content, it has strong resistance to chemical attack.
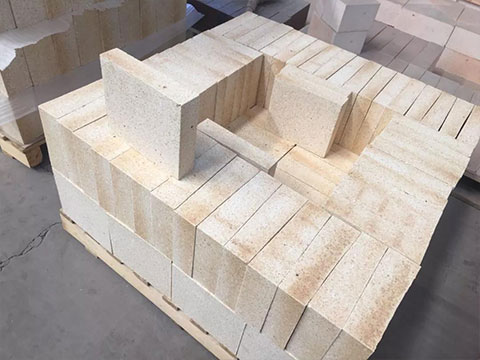
Application of Andalusite Bricks in Torpedo-Type Hot Metal Tanks
Burned andalusite bricks were used on a 150t torpedo-type hot metal tank in a steel plant and achieved good results. It has been used without any repairs and has a lifespan of 520 times. It greatly exceeds the service life of the original high alumina bricks, about 300 times. The use of andalusite bricks shows that the bricks have a low erosion rate, good thermal shock stability, and no peeling, cracking, etc.
Formed under 63GPa (630t) press. After drying, the brick density is 2.65 ~2.75g/cm3. It is made by keeping it at 1500℃±20℃ for 8 hours.
The indicators of andalusite bricks such as load softening temperature and thermal shock stability are significantly better than those of high alumina bricks. Therefore, it has a better use effect, but it is not as good as andalusite-SiC-C brick.
Application of Andalusite Bricks in Lead-Zinc Sealed Blast Furnace
During maintenance at a smelting plant, it was discovered that the high-alumina brick wall was seriously eroded, with only about 1/3 remaining, which is about 115mm thick. In order to improve equipment operation rate, reduce costs and increase output, it was decided to extend the maintenance cycle to three years. If the blast furnace is still lined with high alumina bricks, it will obviously be difficult to meet production requirements. Therefore, the furnace lining needs to be re-selected. Andalusite bricks are used to adapt to the new furnace age requirements.
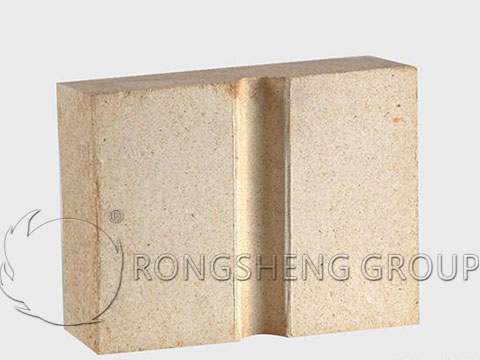
Damage Factors and Material Selection Requirements for Blast Furnace Lining
During many years of use, it has been found that the most vulnerable parts of the blast furnace body are concentrated in the furnace throat, four furnace doors, secondary air outlets, and above. During the annual mid-maintenance process, considerable damage to these areas was discovered. The furnace shell can even be seen in some places, and only local repair methods can be used to extend the furnace life. If the situation is serious, special protective measures must be taken during production. For example, spraying water to force-cool the furnace shell will cause great inconvenience to production. The damage to the furnace lining is mainly caused by the following aspects.
- ① The blast furnace has a high temperature and strong reducing atmosphere, which is prone to coke formation during operation, especially at the furnace throat, 4 furnace doors, secondary air outlets and above. When coking reaches a certain level, it is often necessary to use coke washing to remove slag, and the coke washing temperature reaches above 1300°C. It is necessary to take a break for cleaning every 1 to 2 weeks, usually once a week. When cleaning, in addition to using a slag scraper to remove slag, the slag that is difficult to remove is also cleaned. The impact force on the furnace lining is relatively large and its structure is easily damaged. In addition, when the wind is off for cleaning, the cooling speed is very fast, and the temperature drops to more than 500°C in a short period of time. Therefore, it is required that the furnace lining material selected has better thermal shock resistance.
- ② When the blast furnace is running, because the upper part is feeding materials, the tuyere blows in high-temperature and high-pressure air, and the lining of the furnace body is simultaneously impacted by the material and washed by the high-pressure gas. Therefore, the lining material is required to have high strength.
- ③ The reducing atmosphere in the blast furnace is strong and there is a large amount of reducing gas CO. Therefore, the selected lining material is required to have a low Fe2O3 content and a strong resistance to CO erosion.
As we all know, mullite has high refractoriness, good creep resistance and corrosion resistance. Andalusite can spontaneously transform into mullite and silica-rich glass phases at high temperatures, resulting in andalusite bricks with low thermal conductivity and dense structure. It has high strength, excellent creep resistance, slag resistance and CO corrosion resistance. Its thermal expansion rate is low and its thermal shock resistance is good. Therefore, based on the above three damage factors of the blast furnace body, andalusite bricks were initially selected as the lining of the blast furnace body.
The three-year use of andalusite bricks on the lead-zinc closed blast furnace body proves that the thermal shock resistance, high-temperature strength and other properties of andalusite bricks can meet the requirements of the furnace body. The service life of the blast furnace is greatly extended. This achieves the good effects of improving the blast furnace operating rate, reducing production and increasing output.
What should I do if the refractory material cracks, falls off, or is easily worn? To solve the problem, you need to dig into the root cause and analyze the real cause. Rongsheng Refractory has been engaged in refractory production and R&D services for many years and can solve various difficult problems in high-temperature kiln linings. Welcome to consult and technical exchange.
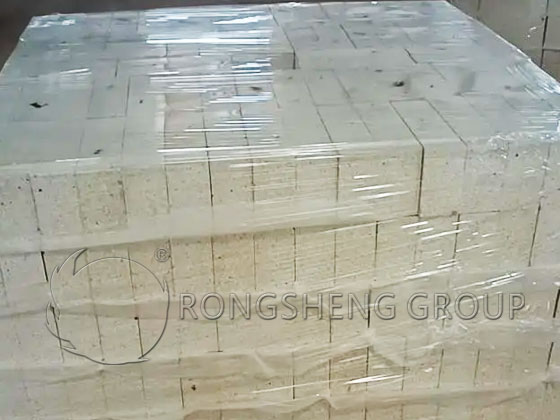
Application Advantages of Andalusite in Refractory Materials
Andalusite is a natural aluminum-siliceous refractory mineral with high-temperature reactivity. Andalusite is also widely used in refractory materials and can be used in the production of refractory bricks and the production of refractory castables. The phase transformation and microstructural changes of andalusite at high temperatures give it special properties such as excellent thermal shock resistance, high thermomechanical strength, good creep resistance, good chemical, alkali metal and metallurgical resistance. The erosion ability of slag, etc. These unique physical and chemical properties can significantly improve the performance of aluminum-silica series shaped and unshaped refractory materials. And it is widely used in metallurgy, non-ferrous metals, glass, cement, casting, and other industries, as well as industrial kilns and ceramic kiln furniture.
Andalusite can be used in refractory bricks and refractory castables in the production of refractory materials. During the production of refractory bricks, andalusite refractory raw materials are added or andalusite refractory raw materials are used as the main aggregate. The refractory bricks produced are andalusite refractory bricks. Andalusite refractory bricks have the characteristics of high-temperature resistance, wear resistance, corrosion resistance, good thermal shock resistance, low creep rate, high load softening temperature, and good thermal spalling resistance. Andalusite refractory bricks can be used in a variety of high-temperature industrial kilns, such as blast furnaces and hot blast stoves.
Andalusite raw material itself is a refractory raw material with excellent properties. When producing castables, andalusite is used as the main refractory raw material. The andalusite amorphous refractory material produced has the best high-temperature creep resistance in long-term high temperatures and has strong resistance to deformation. When producing refractory castables, a certain amount of andalusite is added to make the high-temperature volume of the andalusite castables more stable. Eliminate the fission phenomenon in the middle and late stages of refractory materials and improve the load-softening and creep properties of refractory castables. Different particle sizes of andalusite play different roles in improving material properties. Coarse-grained andalusite can improve the high-temperature strength of the material, while fine-grained andalusite can improve the material’s thermal shock resistance. This is very effective in solving the cracking problem during the use of castables.
Andalusite refractory bricks and andalusite refractory castables contain andalusite raw materials, which have stable high-temperature properties and low high-temperature creep rates. Suitable for industrial kilns in long-term high-temperature environments. Contact us to get free samples and quotes.