The quality of the taphole of the ferrosilicon electric furnace directly affects the service life of the taphole and the life of the furnace lining. Due to the high reduction temperature in the ferrosilicon furnace, the molten iron that has been smelted is regularly discharged from the iron hole, so the iron hole is extremely easy to oxidize and corrode. In addition to other reasons, the furnace wall burn-through accidents at the iron hole often occur, and directly affect the completion of production indicators. In view of the above situation of furnace bricks, we summarized the problems existing in the use of 203# and 204# furnace tapholes, and adopted a composite structure of “corundum silicon carbide bricks-roasted carbon blocks-high alumina bricks“. Judging from the use of more than one year, the life cycle of the taphole has been increased to a certain extent, the hot shutdown and maintenance costs have been reduced, and better economic benefits have been achieved.
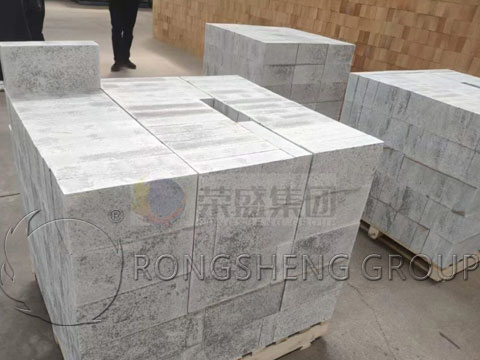
The Design and Use of the Original Taphole
A 12500kVA ferrosilicon electric furnace was originally designed with two tapping holes, which were installed at positions that formed an angle of 160° with each other. The iron mouth area is composed of furnace walls and launders. The iron mouth and launder are all built with roasted carbon blocks, and the surroundings are built with high-alumina bricks.
The average use cycle of the tap hole in normal production is 15 days per eye. After 1-3 months of use, the furnace wall of the tap hole burned through, and the runner burned out. The furnace eye oxidizes quickly, mainly on the left, right, and upper part of the iron mouth. Sometimes the furnace eye expands soon after use, especially in the later period of use, the amount of mudball is large, and the furnace eye running accident is prone to occur, which makes it difficult to open the eye plug. It takes about 50 pieces of electrode paste to repair the iron hole of each eye, and the labor intensity is high and the repair time is long. The main cause of the above problems is that the carbon bricks are easily oxidized at high temperatures, while the tapped carbon bricks are exposed to the air, which accelerates the oxidation of the carbon bricks. As a result, the furnace eye becomes larger and the iron hole maintenance is difficult.
The Use of Corundum Silicon Carbide Bricks Instead of Carbon Bricks for Masonry Tapholes
During the overhaul of 201# and 202# furnace linings refractory bricks, corundum silicon carbide bricks were used to replace part of the carbon bricks to build the tapholes. After the iron hole is transformed, the furnace eye life cycle is 25 days on average, and the longest time is 45 days. The iron mouth has never been burned through the furnace wall and the iron mouth furnace lining has never been seriously oxidized. From the perspective of production practice, the furnace eye is slow to oxidize and has a small area. Generally, only 15 pieces of electrode paste can be used to repair the furnace eye and launder. The carbon bricks of the runners are generally replaced less frequently, which effectively improves the service life of the tap hole and reduces the maintenance frequency and labor intensity of the tap hole.
The production practice of using corundum silicon carbide bricks for more than a year has proved that the material has good thermal stability at high temperatures, high refractoriness, and resistance to corrosion by molten iron and slag. It has the characteristics of no cracking, no oxidation, and no deformation at high temperatures. Therefore, the service life of the H iron port is improved. Moreover, the corundum silicon carbide brick is a conductor at room temperature, and its conductivity is significantly increased when used on a high-temperature iron hole, which makes the eye-opening work smoother.
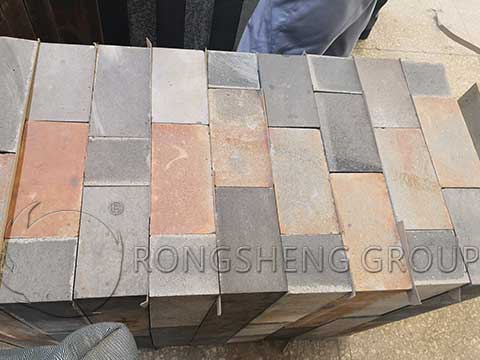
Application of Corundum Silicon Carbide Brick
Corundum silicon carbide bricks are economical and practical to be applied to the taphole of the ferrosilicon electric furnace. At the same time, according to data reports, it can also be applied to the taphole of other types of ferroalloy electric furnaces, such as smelting silico-manganese and silico-chromium alloys, and has also received good results. It should be noted that the quality of the material must meet the design requirements when building the “corundum silicon carbide brick-roasted carbon block-high alumina brick” iron mouth structure. At the same time, the masonry quality of the furnace lining in the taphole area must be guaranteed, and maintenance must be strengthened during use. Only in this way can the life cycle of the taphole and the life of the furnace lining be effectively extended, and economic benefits can be improved.
Buy corundum silicon carbide bricks from the fire bricks manufacturers, free specification customization of corundum silicon carbide bricks, and free samples. A strong-strength refractory material manufacturer not only has an advanced production line of refractory bricks but also the quality of refractory bricks is guaranteed. The customer service is also relatively complete. Get furnace bricks’ competitive prices from the refractory bricks manufacturer.