In China, the early regenerative ball regenerative combustion technology was applied to the steelmaking open hearth and preliminary rolling soaking furnace in the iron and steel metallurgy industry. Based on the application of high alumina refractory ball, we look at some characteristics of high alumina refractory balls.
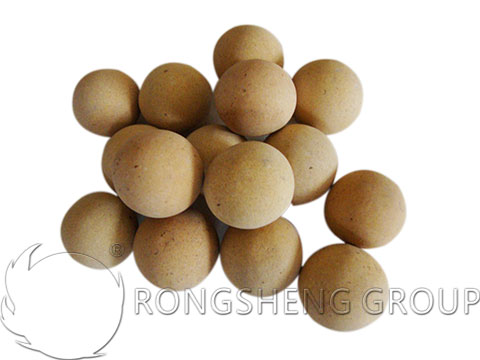
High Alumina Refractory Ball
Where the Al2O3 mass fraction is greater than 45%, refractory materials based on alumina or aluminosilicate are called high-alumina refractories. High alumina refractory products have different mineral compositions due to different Al2O3 content. As the Al2O3 content increases, the mullite and corundum crystal phases increase in the product, while the glass phase decreases accordingly, and the fire resistance increases accordingly. Generally, the fire resistance of high-aluminum refractory balls is not less than 1750 ~ 1 790 ℃, and the temperature at which the load begins to soften is not less than 1 400 ~ 1530 ℃.
Advantages and Disadvantages of High Alumina Refractory Balls
Al2O3 belongs to amphoteric oxide, so it has better resistance to acid slag erosion, but weaker than silicon refractory ball. Its resistance to alkaline slag erosion is also better, but weaker than Mg-Al refractory balls. When the Al2O3 content of the product is higher, its thermal stability will be significantly reduced.
During the operation of the ball-type hot blast stove, the refractory ball will be affected by the periodic cold-heat alternation under high temperature and the erosion or slagging of alkaline gas dust.
Production practice shows that high-alumina refractory balls are used in the high-temperature area of the pebble bed, and their fire resistance and load softening temperature can meet the requirements, but thermal stability and slag resistance appear insufficient. Therefore, surface cracks and slagging bonding phenomena often occur, resulting in poor air permeability of the bed and shortening the ball cleaning cycle.
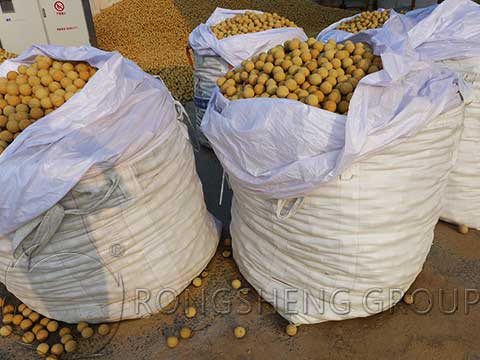
Application of High Alumina Refractory Ball
With the development of technology, high-alumina refractory balls have gradually been applied to various industrial furnaces such as soaking furnaces, car bottom annealing furnaces, and heat storage ball heating furnaces.
The lower and lower refractory balls of the hot blast stove are φ60mm AZC composite high-alumina refractory balls and φ45mm high-alumina refractory balls. These two balls have the same chemical and mineral composition except for their diameters. The powder generated by the damage and crushing of the alumina refractory balls and wall bricks is deposited in this area of the ball bed and mixed with the refractory balls and bonded together. The lower and lower sections of the hot blast stove have the characteristics of large bonding area and low bonding strength.
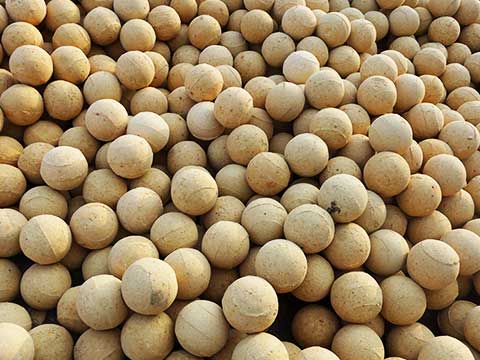
RS High Alumina Refractory Manufacturer
RS high-alumina refractory manufacturer has more than ten years of experience in the production and sales of refractory materials. Our refractory products have passed ISO 9001 quality certification and have been sold to more than 60 countries and regions in the world. If you have projects that require high alumina refractory ball, please contact us. We will contact you as soon as possible.