Traditional high alumina bricks and carbon bricks can no longer meet the needs of clean steel and steelmaking. In order to improve the corrosion resistance, thermal shock resistance and molten steel quality of ladle bricks, magnesia-alumina unburned bricks have become an ideal product for the new generation of ladle bricks. Magnesia-alumina spinel bricks have the following characteristics and can meet future applications in ladles.
What are Magnesia-Alumina Spinel Bricks?
Magnesia-aluminum spinel bricks are a series of crystals with the same structure as magnesium-alumina spinel MA. Magnesia-aluminum spinel belongs to the cubic variety. Magnesia-chromium spinel is an equiaxed mineral with a hardness of 5.5. Relative density 4.43, refractive index n=2.00 but no magnetism. Magnesia-alumina spinel bricks are made of natural magnesia materials such as magnesite, light-burned magnesia powder, and chromite. They are matched according to the design requirements, finely ground, and A raw material with magnesia-chromium spinel as the main component obtained by briquetting, calcining or electric fusion. my country’s ferrous metallurgy industry-standard YB/T132-1997 stipulates the technical conditions for magnesium-alumina spinel bricks.
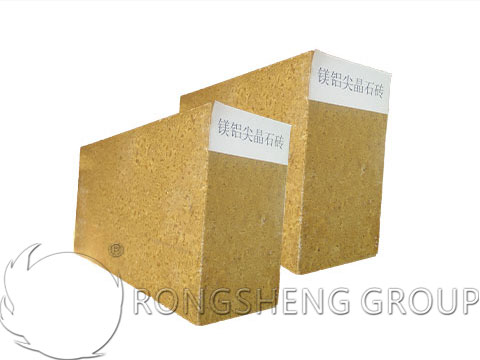
When making sintered magnesia-alumina spinel bricks, they are proportioned according to the planning requirements, further ground and pelletized, and then calcined in an oxidizing atmosphere. Made after cooperation and melting. Magnesia-alumina spinel bricks have perfect crystallization, dense structure, low porosity and high degree of direct bonding. Therefore, cast and combined magnesia chromium bricks have excellent corrosion resistance and are widely used in very severe corrosion situations. However, the thermal shock resistance of melt-cast rebonded magnesia-chromium bricks is inferior to that of directly bonded magnesia-chromium bricks made from magnesia and iron ore.
What are the Precautions for the Application of Magnesia-Alumina Spinel Bricks in Ladles?
- Physical properties. Comparing the physical properties of new ladle bricks, traditional Al2O3-MgO castables, and sintered high alumina bricks, the new ladle bricks have lower apparent porosity and higher bulk density than traditional castables. However, the new ladle-clad bricks have higher strength after drying and at 1000°C.
- Linear change. The linear change of the new ladle-clad brick is higher than that of the two traditional materials. Furthermore, the expansion phenomenon continued until later because the new ladle bricks were unburned bricks and the spinels near the hot surfaces reacted, effectively reducing erosion at the joints;
- Slag resistance. The slag corrosion resistance test was carried out using the above materials through the rotating slag test. Using oxygen and propane as fuel, under the test conditions of 1650℃ and 5h, the slag basicity of the material is 6.2. The corrosion resistance of the new ladle brick is better than other materials, and the slag penetration thickness is also thinner. While periclase completely disappears from the hot surface, and the amount of secondary spinel is large. However, from a thermal perspective, the amount of residual periclase increases, and the amount of secondary spinel decreases.
- Thermal conductivity. Thermal conductivity of high alumina bricks, magnesia carbon bricks (carbon content 15%), and unburned AI2O3-MgO bricks (new ladle clad bricks) at 600°C. The thermal conductivity of the new ladle brick is lower than that of magnesia carbon bricks and is almost the same as that of high alumina bricks and Al2O3-MgO castables.
- Creep properties of Al2O3-MgO castables, high alumina bricks, and new ladle bricks. At around 1400°C, the new ladle bricks undergo some expansion due to the secondary spinel formation reaction, making the curve appearance similar to that of Al2O3-MgO castable. The creep value of the new ladle brick is 1.197, and the creep value of the Al2O3/MgO castable is 1.1668. This is because the expansion in the joints of the new ladle bricks is absorbed.
Rongsheng Refractory Brick Manufacturer is located in Xinmi City, Henan Province, the capital of refractory materials in China. We mainly produce and sell various refractory bricks, unshaped refractory castable materials, insulation materials, etc. We integrate R&D, production and sales. Our refractory products can be used in metallurgy, chemical industry, building materials, electric power, non-ferrous metals, carbon industries, etc. We are committed to the service of refractory lining materials for high-temperature industrial furnaces. Can provide free refractory material designs, solutions, etc. Contact us to get free samples and quotes.
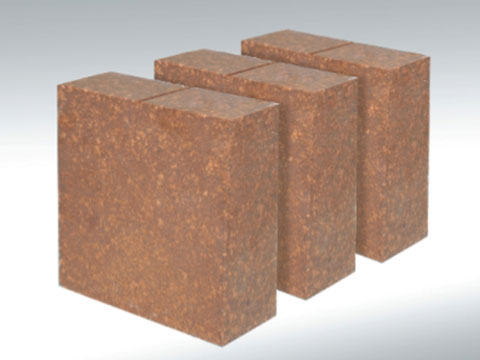
Production Technology and Application Advantages of Magnesia-Alumina Spinel Bricks
Magnesia-alumina spinel bricks are products made from high-purity magnesia and pre-synthesized magnesia-alumina spinel as the main raw materials, through reasonable grading, high-pressure molding, and high-temperature firing. It is characterized by high strength, corrosion resistance, low linear expansion coefficient, and good thermal shock resistance. Magnesia-alumina spinel bricks are ideal refractory materials for cement rotation and self-transition zones.
Bauxite-based sintered magnesia-aluminum spinel uses high-quality bauxite with an Al2O3 content of more than 76% and high-quality light-burned magnesium powder with a MgO content of more than 95%. After a multi-stage homogenization process, it is sintered at a temperature above 1800°C in an ultra-high temperature tunnel kiln. It has high volume density, high mineral phase content, well-developed grains, uniform structure, and stable quality. Magnesia-aluminum spinel has good corrosion resistance, strong corrosion and peeling ability, good slag resistance, abrasion resistance, good thermal shock stability, high-temperature resistance, and other performance characteristics. It is an ideal raw material for the production of refractory products such as magnesia-alumina spinel bricks, ladle lining bricks, and ladle castables used in the high-temperature zone of cement rotary kilns. Magnesia-aluminum spinel is widely used in refractory materials, steel smelting, cement rotary kilns, and glass industrial kilns.
Application advantages of magnesium aluminum spinel. One is to replace magnesia-chromium sand to make magnesia-alumina spinel bricks for use in cement rotary kilns. It not only avoids chromium pollution but also has good peeling resistance. Second, it is used to make ladle castables, which greatly improves the corrosion resistance of the steel plate lining. Making it widely used as a refractory material for steelmaking.
Application Advantages of Magnesia-Alumina Spinel Bricks
- Excellent kiln hanging performance.
- Low thermal conductivity (1000℃, 2.27w/m·k) and small thermal expansion coefficient (1000℃, 1..217%).
- Has excellent structural flexibility. It has strong anti-erosion and anti-penetration capabilities against K2SO4, Na2SO4, NaCl, and KCl alkali salts decomposed by cement materials.
- It has a high softening temperature under load and excellent thermal shock resistance. It is suitable for key parts of SP and NSP kilns with high kiln temperatures, fast rotation speed, strong alkali erosion ability, and heavy mechanical load. It can effectively extend the life of the furnace lining and maintain a lower temperature of the kiln barrel.