Magnesia-chrome bricks and clay bricks are generally used as refractory bricks for zinc oxide rotary kilns. Magnesia-chrome bricks are used in the sintering zone, clay bricks are used in the cooling zone and other parts, and steel fibers are poured in the kiln head and kiln tail.
Magnesia-chrome bricks for furnaces in the lead smelting industry
Lead smelting has complex requirements for refractory materials. Not only must there be sufficient high-temperature resistance, but also a certain high-temperature mechanical strength, and at the same time, it must have good resistance to slag erosion and slag and flue gas erosion. Therefore, there are very strict requirements for the selection of refractory materials in the furnace. Magnesia-chrome bricks are mainly selected in their high-temperature working area. The selection of refractories in the working area (furnace wall and furnace roof) of the lead smelting furnace is divided into two areas. One part is the magnesia-chrome brick in the molten pool area (especially the slag line area), and the other is the magnesia-chrome brick in the gas phase area.
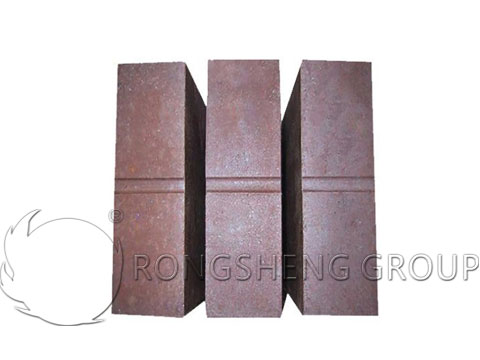
-
Furnace molten pool area
The refractory bricks in the molten pool area (especially the slag line area) will be eroded and washed by the slag, and the composition of the lead smelting slag is relatively complex. High-alumina refractory materials will participate in the slagging reaction, so it is not appropriate to use high-alumina refractory bricks, and magnesia-chrome refractory bricks should be used. At the same time, considering the slag corrosion resistance and erosion resistance of refractory bricks, magnesia-chrome bricks with electrofusion and recombination should be selected. The refractory bricks of this material are more resistant to slag erosion than semi-recombined magnesia-chrome bricks. The increase of Cr2O3 content can improve the slag corrosion resistance of bricks, so try to choose magnesia-chrome bricks with higher Cr2O3 content.
-
Gas phase zone in the furnace
The refractory bricks in the gas phase zone will not be corroded by slag, but only by the splash erosion of a small amount of molten edge and the erosion of dusty flue gas. Therefore, magnesia-chrome bricks with lower Cr2O3 content can be selected.
The magnesia-chrome bricks used in the lead smelting reduction furnace of a certain factory used directly bonded magnesia-chrome bricks with higher Cr2O3 content in the early stage of production. There are phenomena such as no metal and slag wrapping on the surface of the magnesia-chrome bricks in the meteorological area, bricks broken into two sections, and loose structure. According to the analysis results, it is judged that a large amount of Fe3+ and Fe2+ in the refractory bricks are reduced to elemental Fe, which leads to the loose structure of the bricks. Therefore, in the maintenance, the fused rebonded magnesia-chrome bricks with lower Cr2O3 content (Cr2O3 containing S is 12%) were used. The main reason for this improvement is that the apparent porosity of fused rebonded magnesia-chrome bricks is low, and the content of Fe3+ and Fe2+ in refractory bricks is reduced at the same time. Therefore, it is more suitable for the strong reducing atmosphere in this gas-phase zone and prolongs the service life. After switching to this type of fused and combined magnesia grid brick, the service time is greatly extended and good results have been achieved.

Characteristics of Zinc Oxide Rotary Kiln
- The zinc oxide rotary kiln is used for the calcination production of zinc oxide. It is a kind of equipment with a good calcination effect and strong pertinence.
- The calcination effect is good, the output is high, and the zinc oxide obtained after calcination has a high utilization value.
- It is more environmentally friendly and adopts a sealed form to effectively avoid dust overflow during operation, improve the working environment and reduce energy consumption.
- The internal structure design is reasonable, the appearance is also very novel, and the connection between the components is also in place, making the equipment run more smoothly.
- It has low requirements on the working environment, can work in harsh environments, and has no obvious influence on the calcining effect of zinc oxide.
- It can work for a long time, because the material has good wear resistance during the production of the equipment, and the number of equipment failures during operation is also very small, which reduces the maintenance cost to a certain extent.
Selection of Refractory Materials for Furnaces in the Lead Smelting Industry
According to the characteristics of the smelting process and the characteristics of the smelting materials, the correct selection and use of refractory materials. This can not only ensure the normal operation of the metallurgical furnace, prolong the life of the furnace, but also enable the enterprise to obtain economic benefits. Only correct and reasonable refractory design, including structural design, expansion calculation, and masonry heating and baking, all affect the normal use of refractory materials. Therefore, on the basis of the existing development, it is necessary to further conduct in-depth research and improvement on refractory materials such as erosion resistance, slag erosion resistance, stress analysis, and baking system. Refractory material suppliers, design units, and users need to work together in order to achieve a better application effect of refractory materials.