Silica bricks refer to acidic silica products with SiO2 content greater than 93%. The properties of silica bricks include chemical mineral composition, true density, bulk density, refractoriness, load softening temperature, high-temperature volume stability, thermal shock resistance slag resistance, etc. It is closely related to many factors such as the nature of raw materials, crystal transformation status, and manufacturing process. Silica bricks are mostly used in the vaults of coke ovens, hot blast furnaces, glass kilns, and tunnel kilns. Shelf bricks of various kilns, etc., especially coke ovens (carbonization chamber, combustion chamber, regenerator) use a large number of silica bricks and siliceous regenerative bricks. RS refractory brick manufacturers can provide high-quality silica brick products. Based on the application of silica bricks and zero-expansion silica bricks in glass kilns, we continuously improve and enhance product quality.
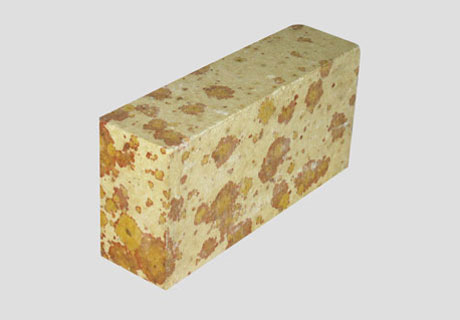
Silica Bricks for Glass Melting Furnace
- The volume is stable at high temperatures and will not cause changes in the furnace body due to temperature fluctuations. Due to the high load softening temperature and the small creep rate of silica bricks, the glass melting furnace can keep the furnace body from deforming at 1600°C and the structure is stable.
- No pollution to glass liquid. The main component of silica brick is SiO2. If there are any pieces falling off or surface droplets during use, it will not affect the quality of the molten glass.
- Resistant to chemical attack. The silica bricks of the superstructure are corroded by gases containing R2O in the glass batch. A smooth metamorphic layer is formed on the surface, which reduces the erosion rate and plays a protective role.
- The volume density is small, which can reduce the mass of the furnace body. The true density of high-quality silica bricks is 2.32-2.36g/cm3, and that of general silica brick products is 2.38-3.42g/cm3.
Although the fire resistance of silica bricks is not very high. However, the softening temperature under load is higher, and the high-temperature structure has greater strength. And it has good stability when used for a long time above 600℃. When heated to 1450°C, the total volume expansion is about 1.5% to 2.2%. This residual expansion will cause the masonry joints to seal tightly, ensuring good air tightness and structural strength of the masonry body. It also has the advantages of long service life and reduced energy consumption. Can resist the erosion of acidic slag. Therefore, it is currently mainly used for building glass furnaces and coke ovens. Use silica bricks to build the partition wall of the coke oven carbonization chamber. It has good stability and air tightness under high temperatures, and its service life can reach 10-15 years. If used properly, it can last more than 25 years.
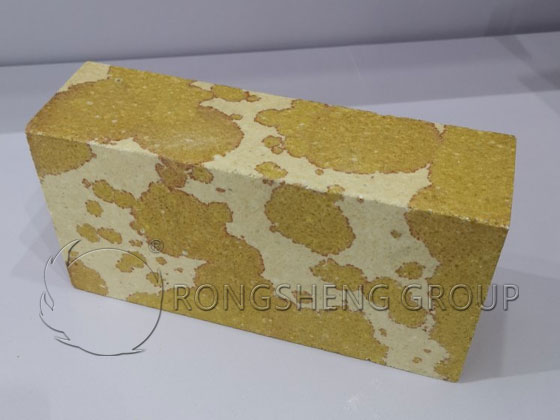
Characteristics of Zero-Expansion Silica Bricks for Glass Kilns
- SiO2 content is greater than 99%, with excellent corrosion resistance and acid resistance.
- Low Fe2O3 content, less than 0.1%, no pollution to products (such as glass liquid, etc.).
- The low flux index (Al2O3+2R2O) is less than 0.3%.
- The thermal expansion rate is close to zero, so there is no need to reserve expansion joints during repairs, which increases the tightness of the masonry.
- Excellent thermal stability, the product will not explode during hot repair. Repair work can be carried out directly without stopping the furnace at high temperatures.
- After repair (hot repair), peeling and other phenomena will not occur, and it is safe and reliable for long-term use.
- Good corrosion resistance. Due to the lack of calcium, erosion cannot form.
Zero expansion silica brick is also called fused quartz brick or thermal shock-resistant silica brick. Resistant to acidic slag erosion. Higher high-temperature strength. The load softening starting temperature is 1620~1670℃. It will not deform after long-term use at high temperatures. Good thermal shock stability, heat exchange in water is 1~30 times. It uses natural silica as raw material and adds an appropriate amount of mineralizing agent to promote the transformation of quartz in the green body into tridymite. It is slowly fired at 1350~1430℃ in a reducing atmosphere. In the process of firing silica bricks, why should they be fired slowly? The main thing is to convert quartz into tridymite. The more tridymite, the smaller the true specific gravity and the higher the melting point. And because phosphoquartz is a spearhead-shaped twin crystal, the spearhead-shaped twin crystals will form an intertwined network structure, giving the product a higher load-softening temperature and mechanical strength. Therefore, it is generally hoped that there will be as much tridymite in the fired silica bricks as possible. Followed by cristobalite, the less residual quartz, the better.
Buy high-quality zero-expansion silica bricks/calcium-free silica bricks from Rongsheng manufacturers. The products have stable quality and fast delivery.