As we all know, carbon refractory materials, such as carbon bricks, have the characteristics of high thermal conductivity, strong slag resistance, high-temperature strength, and good thermal shock resistance. In addition, it has the advantages of large-scale. Therefore, Carbon Brick for Blast Furnace is widely used in the hearth and hearth of the blast furnace and other important parts that determine the service life of the blast furnace. In order to meet the requirements of the use conditions such as the always 1600℃ molten iron staying, which causes the difficulty of an overhaul.
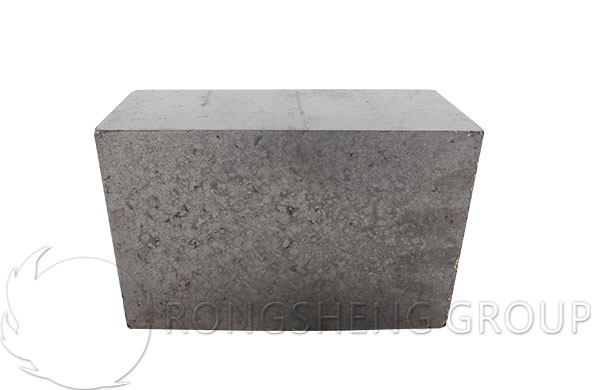
Different Damage to the Inner Lining of the Blast Furnace
The operating conditions of the Carbon Brick for Blast Furnace using as the lining of each part are different, so the damage state is also different. Carefully observe the damage characteristics of a blast furnace in a steel plant, and make the following summary.
- (1) The upper three layers of charcoal bricks of the hearth charcoal bricks are gradually eroded during the production with the erosion of the high alumina brick lining above the charcoal bricks. When the furnace is shut down for major repairs, the remaining thickness of the upper layer of bricks is generally only 400-800mm, and the thickness gradually increases downward. The carbon bricks from the fourth layer to the centerline of the taphole tend to erode less, but the carbon bricks around the slag taphole are generally eroded seriously.
- (2) The erosion rate of the charcoal bricks in the hearth below the taphole is greatly accelerated, forming a mushroom-shaped erosion with the erosion line of the furnace bottom. During the overhaul, the remaining carbon brick thickness in the hearth was only 200-400mm.
- (3) The inside of the hearth charcoal brick lining generally has serious annular erosion joints. Some form a ring-shaped cavity, some ring-shaped joints with carbon bricks become powder, and some become loose, and the strength is greatly reduced. The width of the circumferential seam belt is generally 200~500mm. The ring seam is wide at the top and narrow at the bottom into a horn shape, and the bottom extends to the corrosion line of the furnace bottom. Some cavities have been connected to the mushroom erosion zone of the hearth, and the slag iron can enter the annular seam zone.
- (4) The corrosion characteristics of the bottom carbon bricks are: the middle of the bottom of the furnace is raised, and the bottom carbon bricks lined by the hearth bricks are eroded into annular grooves. The erosion depth is 300~500mm deeper than the center. For all-carbon brick water-cooled thin furnace bottom, the maximum erosion depth is 2.3~2.5m. A large number of blast furnace shutdown and damage investigation data show that the damage of the carbon hearth bottom has two obvious characteristics: ① the shape of the hearth bottom erosion line is abnormal; ② the annular joint is formed in the sidewall of the hearth.
- (5) In the brick cracks of the residual carbon bricks at the bottom of the furnace, there are many iron sheets with a thickness of 2-10mm and a depth of about 500mm, and the thickest one is 40mm. It shows that this is also a view of erosion that cannot be ignored.
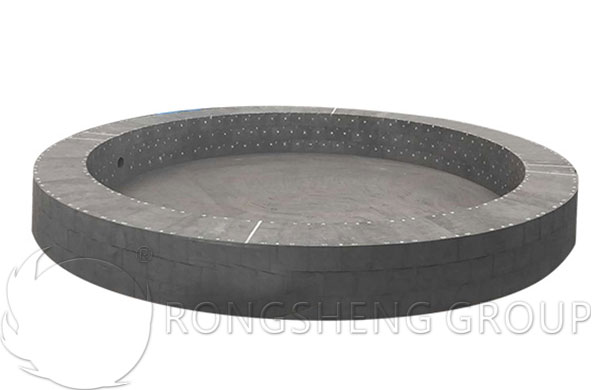
Understanding of the Formation Mechanism of Abnormal Erosion Line of Hearth and Bottom
The corrosion line of the hearth bottom of the carbonaceous hearth has a small top and a large bottom, which is different from the pot bottom erosion line of the hearth bottom of clay or high alumina bricks, so it is called abnormal erosion. Through the above analysis and discussion, it can be seen that iron infiltration of carbon bricks is a major cause of corrosion of the carbon hearth bottom of blast furnaces. However, there should be two prerequisites for the molten iron to penetrate into the carbon bricks: ① It must exist with a strong effect; ② The iron must exist in liquid form. As mentioned earlier, iron infiltration of carbon bricks will cause corrosion of carbon bricks, and the erosion of all hearths and bottoms constitutes its erosion shape. The reason why the erosion degree of the hearth bottom is gradually deepening and showing abnormal erosion can be investigated from the two prerequisites for the penetration of molten iron into carbon bricks.
Reasons for damage of lining carbon bricks in a blast furnace
There are many reasons for the damage of Carbon Brick for Blast Furnace lining, especially because the stress of blast furnace lining carbon bricks increases with the improvement of blast furnace efficiency. Among them, the blast furnace bottom and hearth carbon lining embodies a comprehensive process and is composed of thermochemical corrosion and thermomechanical corrosion. The mechanism of erosion is:
- (1) Metal penetration. The penetration of molten iron will change the physical parameters (performance) of carbon brick materials.
- (2) Carbon bricks are dissolved. The carbon entering the molten metal causes the carbon brick to melt in the carbon subsaturated molten iron.
- (3) The flow of the molten product of zinc and alkali. This leads to an increase in mass transfer and thermal conductivity and carbon loss on the working surface.
- (4) The deposition of stress metal leads to unstable heat flow in the lining, thereby forming cracks and causing peeling damage.
These mechanisms do not appear singly, but are integrated and mutually reinforcing, resulting in the destruction of carbon bricks.
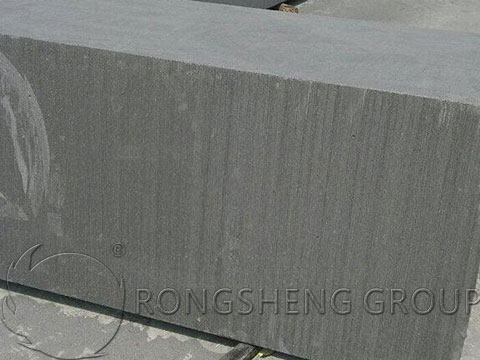
The Detail Corrosion of Blast Furnace Lining of Carbon Bricks
- (1) Different carbon bricks have very different air permeability. The air permeability of the same carbon brick is anisotropic. This factor should be considered when laying blast furnace charcoal bricks.
- (2) The distribution of micro-pores before and after iron infiltration of carbon bricks changed significantly. Under the production conditions of a certain steel plant, the infiltrated molten iron mainly fills the micropores with a diameter of more than 24 m. This can be used as a reference standard for the production of microporous carbon bricks.
- (3) The molten iron penetrating into the carbon bricks mainly corrodes the binder structure, and the large pores of the carbon bricks are mainly distributed in the binder structure.
- (4) Iron penetration is a major cause of carbon brick erosion. As the static pressure of the molten iron increases, the degree of penetration and damage of the molten iron to the carbon bricks increases, which helps to form abnormal corrosion lines.
- (5) If the temperature distribution in the blast furnace charcoal hearth and bottom block is abnormal, it will be beneficial to the penetration of molten iron and the formation of abnormal corrosion lines.
- (6) The low melting point metal in the molten iron is deposited in the lowermost part of the hearth, which lowers the melting point of the molten iron in the lower part and increases the penetration of the molten iron in the lower part. The erosion of the lower carbon bricks is increased, resulting in abnormal erosion.
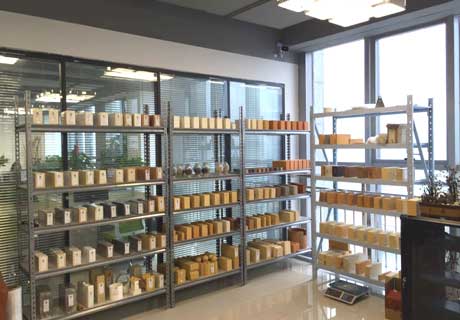
Rongsheng Refractory Brick Manufacturer
Rongsheng is an experienced refractory brick manufacturer and sales company. Rongsheng’s carbon brick products have a good reputation among customers. Rongsheng’s refractory bricks products have also been sold to more than 60 countries and regions around the world. For example, Vietnam, Laos, Thailand, Malaysia, Singapore, Indonesia, Philippines, Turkey, Kuwait, South Africa, Egypt, Russia Uzbekistan, etc. We have rich experience in the production and sales of blast furnace carbon bricks, ladle magnesia carbon bricks, and magnesia spinel bricks for rotary kilns. If you are repairing the furnace lining or rebuilding the furnace lining, or you plan to build a new project if you need to buy refractory lining materials. Please contact us. We will provide you with services according to your specific needs.