High Alumina Fire Bricks are a kind of alumina silica fire bricks that contain more than 48% Al2O3 content. High alumina fire bricks have properties of high thermal stability and refractoriness, and good slag resistance. They can be used to build electric furnace for steel making, glass furnace and lining of rotary kiln.
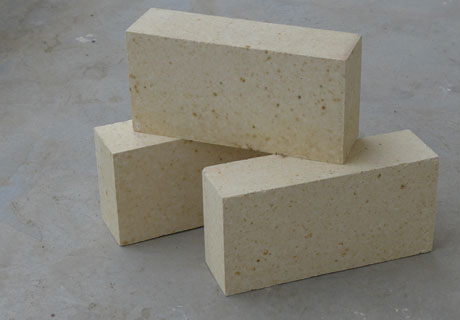
High Alumina Fire Bricks Composition
High Alumina Fire Bricks are high grade refractory materials with high refractoriness under load and low creep, which are made of alumina, fused alumina and fused mullite as the main raw materials.
Alumina silica fire bricks include high alumina bricks, mullite bricks and corundum bricks according to the different Al2O3 content.
Refractory Bricks are shaped refractory materials with certain shapes and sizes. There are burnt brick, unburnt brick, fusion cast brick, insulating fire bricks according to the different manufacturing process. There are standard brick, common brick, special brick according to different shapes and sizes, such as fireclay bricks, high alumina bricks, silica bricks, magnesia brick and so on.
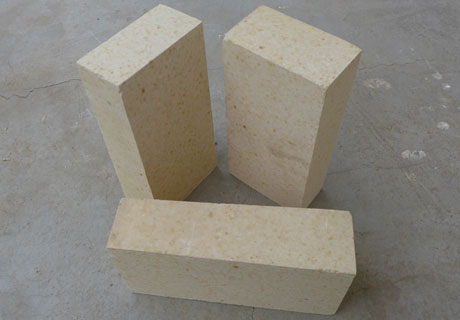
High Alumina Fire Bricks Properties
- Refractoriness
High Alumina Fire Bricks Products are the high grade alumina-silicate refractory. Their refractoriness will increase with the increasing of Al2O3 content, which generally is not lower than 1750~1790℃. When the Al2O3 content reach up to 95%, it is the corundum bricks that can resist high refractoriness of 1900~2000℃. - Refractoriness Under Load
High Alumina Fire Bricks Products’ refractoriness under load will reduce with the the increasing of SiO2 content and alkali metal oxide content, which is higher than fireclay bricks’ refractoriness under load of 1420~1530℃. Corundum bricks’ refractoriness under load reach up to 1600℃. - Slag Resistance
As the high alumina fire bricks contain much high neutral Al2O3 content, this kind of refractory products have strong alkali furnace slag erosion resistance. - Thermal Shock Stability
In the high alumina fire bricks products, there are two types of crystals of corundum and mullite exiting. As the corundum’s thermal expansion coefficient is higher than mullite’s. When the temperature change happened to the refractory bricks, the thermal expansion difference results the stress concentration. High alumina fire bricks products’ thermal shock stability is worse than fireclay bricks products’. - Reheating Linear Change
If the firing temperature and time of high alumina bricks products is enough, the volume is stable and the reheating linear change is low. Or, the recrystallization will cause the linear after contraction of fireclay bricks.
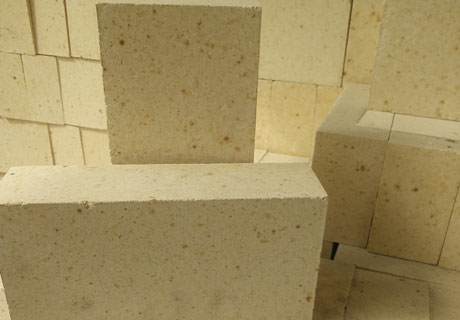
High Alumina Fire Bricks Application
High Alumina Fire Bricks can be used in many kinds of industrial furnaces or kilns, such as blast furnace, hot blast furnace electric furnace for steel making and molten steel ladle as the furnace top and wall. High alumina bricks also can be used for checkerwork of regenerative chamber, reverberatory furnace and rotary kiln.
High Alumina Fire Bricks Manufacturing Process
High alumina fire bricks have the similar manufacturing process with fireclay bricks. They are produced with alumina and other raw materials with high alumina content through molding and firing in the high temperature.
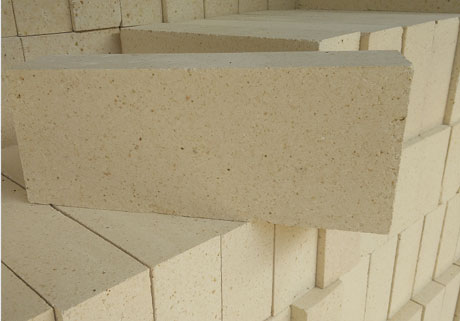
High Alumina Fire Bricks Manufacturer
Find the best high alumina fire bricks manufacturer to buy high quality high alumina fire bricks. If you want to lower your cost, you can choose RS Company, a professional refractory fire bricks supplier in China, to buy cheap high alumina fire bricks. China produces high quality refractory raw materials, thus we have the advantage to manufacture the best high alumina fire bricks and provide customers with lower price. Contact us for more details.