In the world of high-temperature industrial processes, managing heat is a constant challenge. Whether it’s in steel production, glass manufacturing, or power generation, the materials used to contain and insulate heat must be both durable and efficient. Among these materials, high alumina insulating fire bricks stand out as a cornerstone of modern thermal management. In this article, we’ll explore what makes these bricks so special, how they work, and why they are indispensable in extreme environments.
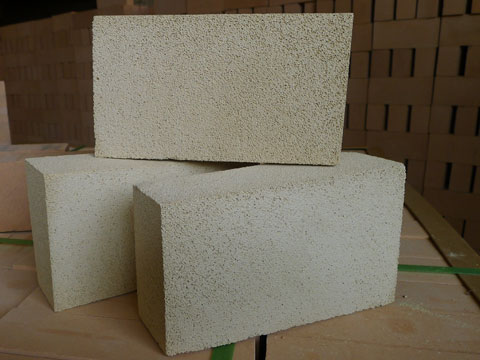
What Are Insulating Fire Bricks?
Insulating fire bricks (IFBs) are a type of refractory material designed to withstand high temperatures while providing excellent thermal insulation. Unlike dense refractory bricks, which are primarily used for structural support, insulating fire bricks are lightweight and have low thermal conductivity. This makes them ideal for applications where minimizing heat loss is critical.
The Importance of High Alumina in Insulating Fire Bricks
The term high alumina refers to the significant percentage of aluminum oxide (Al₂O₃) in the brick’s composition. While standard insulating fire bricks might contain around 30-40% alumina, high alumina bricks typically contain 50% or more. This high alumina content is what gives these bricks their superior thermal and mechanical properties.
Aluminum oxide is a ceramic material with excellent thermal stability, a high melting point (over 2000°C), and resistance to chemical corrosion. These characteristics make high alumina bricks ideal for applications where both extreme heat and chemical exposure are factors.
Key Properties of High Alumina Insulating Fire Bricks
- High Temperature Resistance: These bricks can withstand temperatures up to 1800°C, making them suitable for use in extreme environments.
- Low Thermal Conductivity: Their insulating properties help conserve energy by reducing heat loss.
- Chemical Resistance: High alumina bricks are resistant to corrosion from acids, alkalis, and other chemicals.
- Mechanical Strength: They are highly durable and can withstand physical stress and abrasion.
- Thermal Shock Resistance: These bricks can endure rapid temperature changes without cracking.
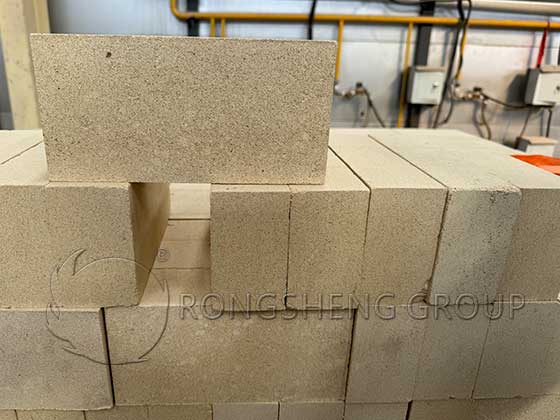
How Are High Alumina Insulating Fire Bricks Made?
The manufacturing process of high alumina insulating fire bricks involves several key steps:
- Raw Material Selection: High-purity alumina is mixed with other refractory materials, such as silica or clay, to achieve the desired properties.
- Forming: The mixture is shaped into bricks using molds or extrusion techniques.
- Drying: The formed bricks are dried to remove moisture, which helps prevent cracking during firing.
- Firing: The bricks are fired at high temperatures (typically between 1400°C and 1600°C) to achieve their final strength and thermal properties.
Applications of High Alumina Insulating Fire Bricks
The unique properties of high alumina insulating fire bricks make them indispensable in a variety of industries. Some common applications include:
- Steel and Metal Industry: Used in blast furnaces, ladles, and kilns where extreme heat and chemical resistance are required.
- Glass Manufacturing: Essential for glass melting furnaces due to their ability to withstand high temperatures and resist corrosion from molten glass.
- Cement Production: Used in rotary kilns and other high-temperature processing equipment.
- Petrochemical Industry: Ideal for reactors and incinerators that handle corrosive chemicals and high heat.
- Power Generation: Used in boilers and incinerators in power plants to manage extreme heat and thermal stress.
Advantages Over Other Refractory Materials
While there are many types of refractory bricks materials, high alumina insulating fire bricks offer several advantages:
– Energy Efficiency: Their insulating properties help reduce energy consumption by retaining heat within the system.
– Longer Lifespan: Their durability and resistance to wear and tear mean they need to be replaced less frequently.
– Versatility: They can be used in a wide range of applications, from industrial furnaces to laboratory equipment.
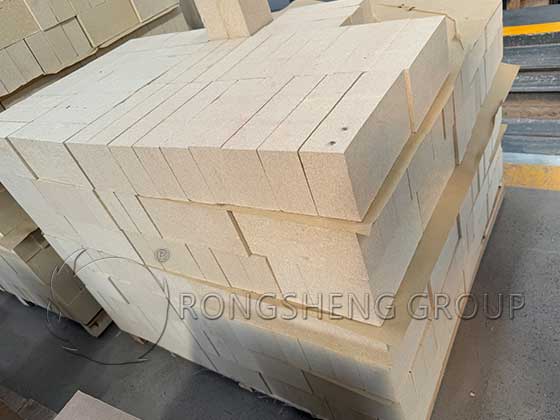
Challenges and Considerations
Despite their many benefits, high alumina insulating fire bricks are not without challenges. They are more expensive than standard insulating fire bricks due to the high cost of alumina. Additionally, their dense structure can make them heavier, which may require stronger support structures in some applications.
RS High Alumina Insulating Fire Bricks Manufacturer
High alumina insulating fire bricks are a marvel of materials science, combining strength, durability, and exceptional thermal insulation. Their ability to withstand extreme temperatures and harsh chemical environments makes them indispensable in industries ranging from steel production to power generation. As technology advances, these bricks will continue to play a vital role in enabling the high-temperature processes that drive modern industry.
Whether you’re an engineer, a materials scientist, or simply someone curious about the world of refractories, understanding the properties and applications of high alumina insulating fire bricks offers a fascinating glimpse into the science of heat management.