Compared with traditional silica bricks, high thermal conductivity silica bricks have been greatly improved in terms of structural morphology, crystal structure, and physical and chemical indicators. After magnifying the structural morphology of high thermal conductivity silica bricks and traditional silica bricks by 20 times, it is found that the pores of high thermal conductivity silica bricks are smaller and more evenly distributed. Gases within pores have a lower thermal conductivity than solids, so pores always reduce the material’s ability to conduct heat. Within a certain temperature range, for a certain porosity, the smaller the pores, the stronger the thermal conductivity.
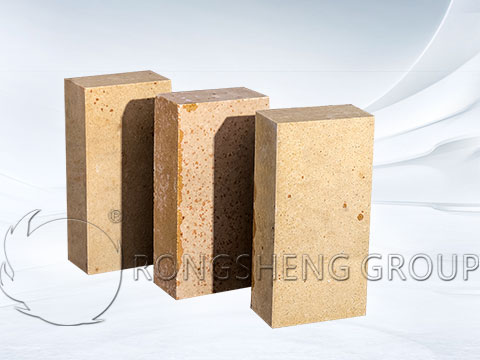
The phosphorous quartz content of the high thermal conductivity silica brick is 70%, and the phosphorous quartz content of the traditional silica brick is 60%. The phospho-quartz content of high thermal conductivity silica bricks is 10% higher than that of traditional silica bricks. Phospho-quartz has a spearhead-like twin crystal structure, which is very dense, which is conducive to the improvement of thermal conductivity.
Performance Comparison between High Thermal Conductivity Silica Bricks and Traditional Silica Bricks
After comparing the basic properties of high thermal conductivity silica bricks with traditional silica bricks, it is found that after the thermal conductivity of high thermal conductivity silica bricks is improved, other performance indicators are consistent with traditional coke oven silica bricks. That is to say, high thermal conductivity silica bricks all inherit the advantages of traditional coke oven silica bricks, and further highlight the characteristics of high thermal conductivity on this basis. It can be seen that all aspects of the performance of high thermal conductivity silica bricks are balanced.
Performance Characteristics of High Density and High Thermal Conductivity Silica Bricks
-
High Density and High Thermal Conductivity Silica Brick
Improving the thermal conductivity of silica bricks has certain economic benefits for shortening the cooking time and increasing productivity. Therefore, the manufacture of high-density and high thermal conductivity silica bricks has attracted people’s attention.
The phase composition of silica bricks is crystal phase (tridymite, cristobalite, and quartz), glass phase, and pores. Among them, the glass phase and pores are the main factors that reduce the thermal conductivity of silica bricks. The biggest influence is the pores, followed by the glass phase.
At present, the way to improve the thermal conductivity of silica bricks is mainly obtained by increasing the content of tridymite and reducing the porosity.
Select special silica raw materials and additives that can be converted into SiO2. Strictly adjusting the firing system and firing bricks under controlled atmosphere conditions is possible for the development of high-density and high thermal conductivity silica bricks.
-
Other Special Silica Bricks
Silica chrome bricks have high resistance to the action of iron oxide and slag. Silicon-zirconium bricks and silicon cordierite bricks have high thermal shock stability. Silicon carbide bricks not only have high thermal shock stability but also have high wear resistance and thermal conductivity. These siliceous refractory materials can meet different needs respectively.
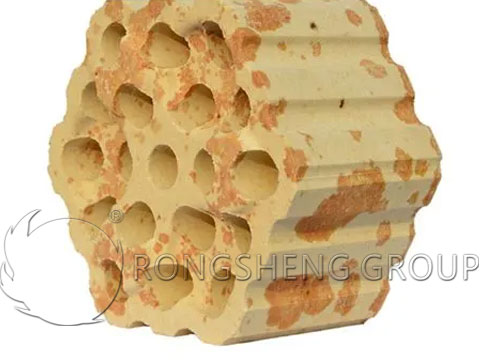
High Thermal Conductivity Silicon Checker Brick
- If the outlet temperature of the hot blast stove remains unchanged, that is, the heat storage capacity of the checker bricks of the hot blast stove remains unchanged. The combustion cycle can be shortened by changing from ordinary silicon checker bricks to high thermal conductivity silicon checker bricks.
- If the combustion cycle and gas consumption of the hot blast stove remain unchanged. After changing from ordinary siliceous checker bricks to high thermal conductivity siliceous checker bricks, the overall heat storage capacity of the hot blast stove increases. Furthermore, increasing the heat release during the air supply period is beneficial to the further increase of the hot air outlet temperature.
- If the outlet temperature of the hot blast stove, the combustion cycle and the heat storage capacity of the checker bricks are kept unchanged. After changing from ordinary silicon checker bricks to high thermal conductivity silicon checker bricks, the heat transferred from the flue gas to the checker bricks will increase. The flue gas temperature during the combustion cycle can be reduced. Thereby, the calorific value of the mixed gas can be effectively reduced, the consumption of coke oven gas can be reduced, and the effect of energy saving and consumption reduction can be achieved.
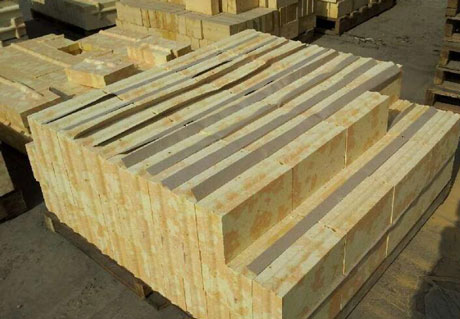
Rongsheng Refractory Brick Manufacturer
Rongsheng refractory brick manufacturer is a powerful refractory brick production and sales manufacturer. In the production and sales of high-quality silica bricks, our technical team and powerful production workshop provide a guarantee for the production of our high-quality high thermal conductivity silica bricks. Committed to solving the problem of refractory brick lining, we will provide customers with the most suitable refractory brick lining products according to their actual production needs. To purchase high-quality refractory brick products and get free refractory brick lining solutions, please contact us.