Application of phosphate-bonded high-alumina bricks in rotary kilns. Phosphate-bonded high-alumina bricks are mainly used in the lining of cement, lime, zinc smelting, and pelletizing rotary kilns. Can phosphate-bonded high-alumina bricks hang kiln skin? The kiln skin can only be hung on the kiln skin at a specific temperature.
If it is used in the kiln lining of a cement rotary kiln for waste incineration power generation, it depends on the chemical composition of the incinerated ash, coal ash, and materials. However, if the temperature is too low, the kiln skin cannot be hung, and even if it is hung, it cannot be hung firmly. Under normal circumstances, phosphate combined high alumina bricks is used as the lining material of the rotary kiln, and the kiln skin cannot be hung when the temperature is lower than 1450 °C. When the temperature is 1490 ℃, the skin of the kiln can be completely hung.
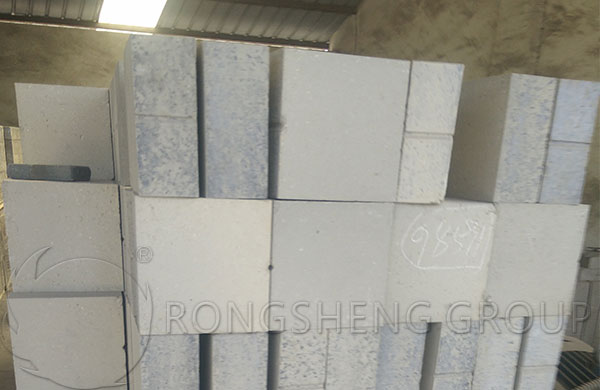
If it is a white ash kiln and a pellet kiln, the kiln skin cannot be hung because the temperature is low. If the temperature is too low or too thin, it will become red. No matter what kind of refractory brick is used as the lining, the operator should be careful in operation. Less material or running coal, and failure to pull the wind in time during operation will cause erosion and impact the kiln skin and kiln lining. Therefore, it is necessary to prevent local material accumulation and agglomeration in the kiln during operation.
Phosphate combined high-alumina bricks is used as the lining material of the rotary kiln for waste incineration and power generation, and the lining of the refractory bricks is often heated up too fast when the kiln is opened, and the kiln skin is damaged due to excessive cooling when the kiln is stopped. If the kiln skin falls off, the temperature of the heated surface of the brick will increase by 500°C to 600°C, causing the interior of the brick body to suffer shock damage. Even when the kiln is stopped, cold air will enter the kiln lining, and if the temperature of the refractory brick drops sharply, the surface of the refractory brick will burst.
Therefore, it is necessary to control the impact caused by drastic changes in temperature. The kiln skin of refractory bricks is generally hung in the firing zone, and the transition zone cannot be hung on the kiln skin due to the low temperature. The less CAS2 content, the firmer the kiln skin.
The changes in silicon and aluminum in the fired clinker play a decisive role in the hanging of the kiln skin. The more molten minerals produced in the clinker, the looser the kiln skin will be. Therefore, phosphate combined high-alumina bricks as the inner lining, and the compactness of the hanging kiln skin depends on the chemical composition of the ash powder, coal ash, and cement materials of waste incineration. The penetration depth of impurities in the material directly affects the firmness and density of the kiln skin.
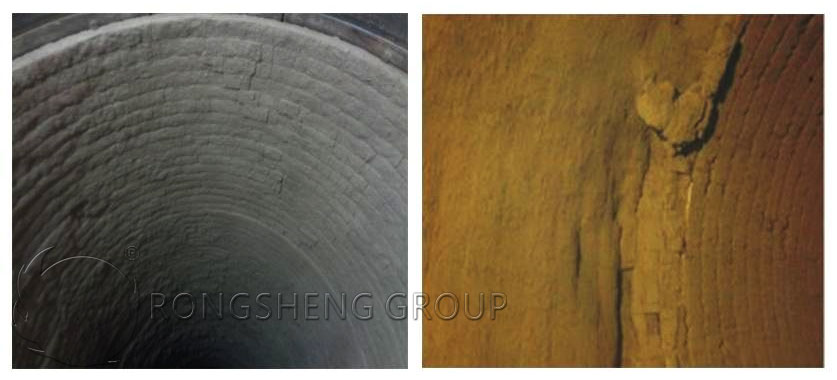
What is the most suitable temperature for phosphate-bonded high-alumina bricks to hang kiln skin?
Rotary kiln lining phosphate combined high alumina brick hanging kiln skin is a protective layer that adheres the material to the surface of the kiln lining brick. It can prevent chemical erosion and mechanical wear of high-temperature materials can also play a role in thermal insulation, and can also improve the service life of the lining.
When phosphate bricks are used as lining bricks for waste incineration rotary kilns, phosphate bricks with an aluminum content of more than 80% are generally used. The most suitable temperature for hanging kiln skin is 1470℃-1480℃. If the temperature is higher than 1490 ℃, too much liquid phase is prone to burning flow, and it is not suitable for hanging kiln skin.
If the temperature is too low and the kiln skin cannot be hung, there is a lack of a layer of kiln skin with sufficient thickness for protection between the refractory brick surface and the ash powder and materials in the kiln. Phosphate-bonded high-alumina bricks have high thermal conductivity due to their high density. If the kiln lining brick body is not thick, the kiln skin cannot be hung or hung too thin, it is very easy to cause a red kiln.
Hanging kiln skin is when the material is close to the firing zone, the flame is gradually shortened, the exhaust volume and combustion volume are increased, the high-temperature flame is controlled, and the refractory brick is fired into a semi-melted state. The chemical composition of the brick and the chemical composition of the clinker are bonded to each other. After condensation, the product of the reaction is agglomerated with the refractory bricks, forming the so-called kiln skin. When the staff operates carelessly and cannot increase the exhaust air in time, the flame extends deep into the kiln to the part where it is not hung on the kiln skin, or the kiln skin is not thick enough, and the accumulation of materials will cause local heating in the kiln. Causes rapid erosion of the kiln lining.
Phosphate-bonded high-alumina bricks often cause the kiln skin to be damaged due to excessive heating of the brick lining when the kiln is opened, and excessive cooling when the kiln is stopped. When the kiln skin falls off, the brick body is damaged by strong thermal shock. When the kiln is stopped, the cold air quickly enters the kiln, so that the temperature of the brick body drops sharply, and the original crack on the brick surface rapidly expands and bursts. Seriously affect the service life of the refractory brick lining.
Although the hanging kiln skin can protect the kiln lining bricks from drawing lots and is wear-resistant. But if the temperature is low, the liquid phase is insufficient to hang the kiln skin. Phosphate-bonded high-alumina bricks that cannot be hung on the kiln skin have a low service life. Generally, the grade of refractory bricks is improved to prolong the service time. Get more details about the application of phosphate-bonded high alumina bricks for the rotary kiln in Kenya.