Rongsheng High Alumina Refractories products have high refractoriness, compressive strength, and load softening temperature. It can be used to build various large blast furnaces, such as steelmaking furnaces, hot blast furnaces, electric furnaces, rotary kilns, and other high-temperature parts of thermal equipment. Common high-alumina refractory products include high-strength lightweight bricks, high-alumina bricks, high-alumina castables, and high-alumina refractory fibers.
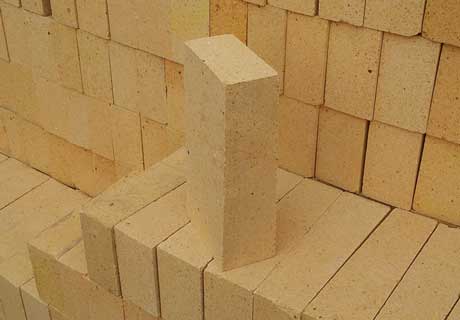
Classification of High Alumina Refractories Materials
High alumina brick
The main mineral composition of ordinary high alumina bricks is mullite, corundum, and glass phase. As the content of Al2O3 in the product increases, the number of mullite and corundum phases also increases, and the glass phase decreases accordingly. The refractoriness and high-temperature performance of the High Alumina Refractories products will increase accordingly.
High alumina bricks with special properties. These include high-load soft high alumina bricks, micro-expansion high alumina bricks, low creep high alumina bricks, and phosphate bonded high alumina bricks.
High alumina bricks have higher thermal conductivity than clay bricks. This is related to the decrease of the glass phase and the increase of mullite crystal or the corundum crystal in the product.
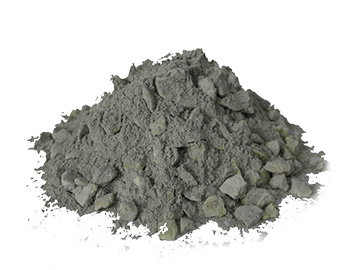
High aluminum castable
The traditional high-alumina refractory castable is an unshaped refractory composed of refractory aggregate powder, binder, and a series of admixtures. The steel fiber high alumina refractory castable is based on the traditional refractory castable, adding 446# heat-resistant stainless steel fiber. Models such as 310#, 330#, 430# are also used, with an additional amount of 1%-3%.
Rongsheng high-strength and high-alumina castables are mainly made of high-alumina bauxite. The application of today’s superfine powder compound type new technology application, plus high-efficiency thickener, etc. Use pure calcium aluminate cement as a fusion agent. Unshaped refractory castables are made of cementitious materials with a mandatory homogenization treatment process. It has high-quality characteristics such as high compressive strength, alkali corrosion resistance, and good wear resistance. Mainly used for large, medium, and small new type dry hair concrete kiln door cover, grate cooler, etc.
High alumina refractory fiber
High alumina refractory fiber uses industrial alumina and high purity silica as the main raw materials. Mix the ingredients in a certain proportion to form a mass. After being lightly burned, it is melted in an electric arc furnace or mixed by a dry method and then melted in a resistance furnace, and the melt stream is fiberized by the centrifugal spinning method or the compressed air injection method, and the raw cotton of high alumina refractory fiber is prepared. Raw cotton can be used directly or further processed into various refractory felts, blankets, boards, and other products.
The maximum use temperature of high alumina refractory fiber is 1400℃, and the long-term use temperature is 1200℃. Mixing high-aluminum fiber and polycrystalline fiber in a certain proportion can be processed into various mixed fiber products. The use temperature is related to the proportion of polycrystalline fiber added, and the use temperature range is 1200 to 1450°C.
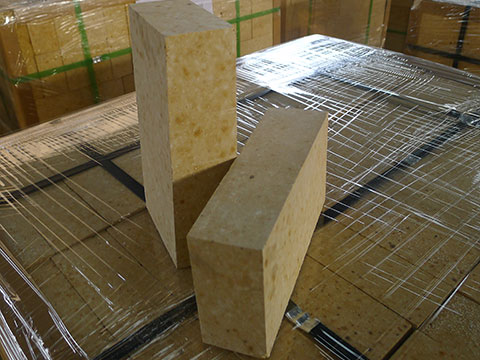
Advantages of High Alumina Refractories
Compared with clay-based refractories, high alumina refractories have the outstanding advantages of high refractoriness and load softening temperature. With the increase of Al2O3 content, the slag resistance is obviously improved.
- (1) Refractoriness. The refractoriness of high-alumina refractories has a large fluctuation range, generally 1770~2000℃. The refractoriness of high-aluminum New Year goods materials is mainly affected by the content of Al2O3 and increases with the increase of the content of Al2O3 in the product. At the same time, the refractoriness is also affected by the content and type of impurities and is related to the mineral phase structure of the product.
- (2) Load softening temperature. The starting deformation temperature of High Alumina Refractories products under load is greater than 1400°C; and it increases with the increase of Al2O3 content.
- (3) Thermal conductivity. High Alumina Refractories products have higher thermal conductivity than clay products. The reason is that there are fewer glass phases with low thermal conductivity in High Alumina Refractories products. The amount of mullite and corundum crystals with better thermal conductivity increases, which improves the thermal conductivity of the product.
- (4) Thermal shock resistance. The thermal shock resistance of High Alumina Refractories products is between that of clay products and siliceous products. 850°C water cooling cycle is only 3~5 times. This is mainly because the thermal expansion of corundum is higher than that of mullite, and there is no crystal transformation.
- (5) Slag resistance. High-alumina refractory products can not only resist acid slag erosion but also resist the effect of alkali slag saving. However, the ability to resist alkaline slag is not as good as that of magnesia materials, but is better than clay 06 and increases with the increase of mullite and corundum content.
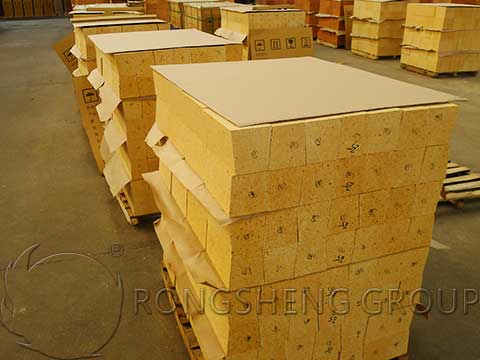
The Properties of High Alumina Refractories
In general, for refractory products with Al2O3 content below 70%, the load softening temperature depends on the quantity ratio between the mullite crystal phase and the liquid phase, and it increases with the increase in the quantity of mullite. Therefore, reducing the content of impurities in the raw materials is beneficial to improve the softening temperature under load and the high-temperature creep properties. For mullite-corundum products with Al2O3 content of 70%-90%, as the aluminum content increases, the load softening temperature does not increase. Only when the product transitions to almost entirely composed of corundum and contains more than 95% aluminum, the high-temperature structural strength can be significantly improved.
The thermal shock resistance of high alumina products is worse than that of clay bricks. Only adding a certain amount of synthetic cordierite to the ingredients can improve the thermal shock resistance of the product. The slag resistance of High Alumina Refractories products increases with the increase of Al2O3 content, but the corrosion resistance of alkaline slag is lower than that of alkaline refractories. The reduction of impurity content is beneficial to improve slag resistance.
High Alumina Refractory Material Manufacturer
Rongsheng high alumina refractory material manufacturer is an experienced refractory material manufacturer. Our refractory products have been sold to more than 60 countries and regions all over the world. For example, Malaysia, Qatar, Bangladesh, South Africa, India, Indonesia, Pakistan, Netherlands, Kuwait, Kenya, Russia, Philippines, Vietnam, etc. In addition to high-alumina bricks, our high-quality refractory brick products include magnesia bricks, magnesia chrome bricks, magnesia spinel bricks, magnesia carbon bricks, corundum bricks, AZS bricks, etc. We also have a fully automatic refractory castable production line with annual output. If you need to buy refractory materials, please leave us your specific needs. We would like to provide you with not only high-quality refractory products but also satisfactory services.