Rongsheng Refractory Brick Production and Sales Manufacturer is a powerful refractory brick production and sales manufacturer. Rongsheng’s zircon refractory bricks have reliable product quality and favorable prices. As a manufacturer and sales manufacturer, Rongsheng regularly shares information on the production and process of refractory brick products. Contact Rongsheng for more information.
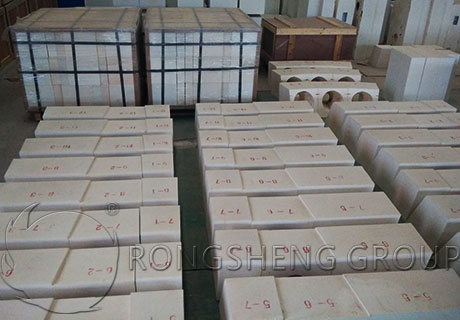
Raw Material Composition of Zircon Bricks
Products made of zircon as the main raw material and adding the appropriate amount of sintering additives. Since zircon raw materials themselves have no plasticity and decompose at high temperatures. Therefore, in the process of producing zircon bricks, it is necessary to take appropriate process measures for binders, particle size ratios and firing conditions.
Rongsheng refractory brick manufacturers use high-quality zircon as the raw material for brick making, and the mass fraction of ZrO2 is above 65%. Strictly control the impurity component R2O in zircon. Because R2O not only reduces the decomposition temperature of zircon but also affects the amount and viscosity of the glass phase formed after decomposition.
Zircon raw materials are very fine in particle size, and direct brick-making is difficult to process. In order to adjust the particle size composition of the ingredients and reduce the shrinkage during firing, Rongsheng refractory brick manufacturers pre-synthesize zircon into clinker. Before synthesizing clinker, zircon is first ground to promote sintering, reduce the sintering temperature, and increase the plasticity of the mud. Usually, particles ground to less than 0.063mm account for more than 80%. Such raw materials can produce clinker with low water absorption and high bulk density.
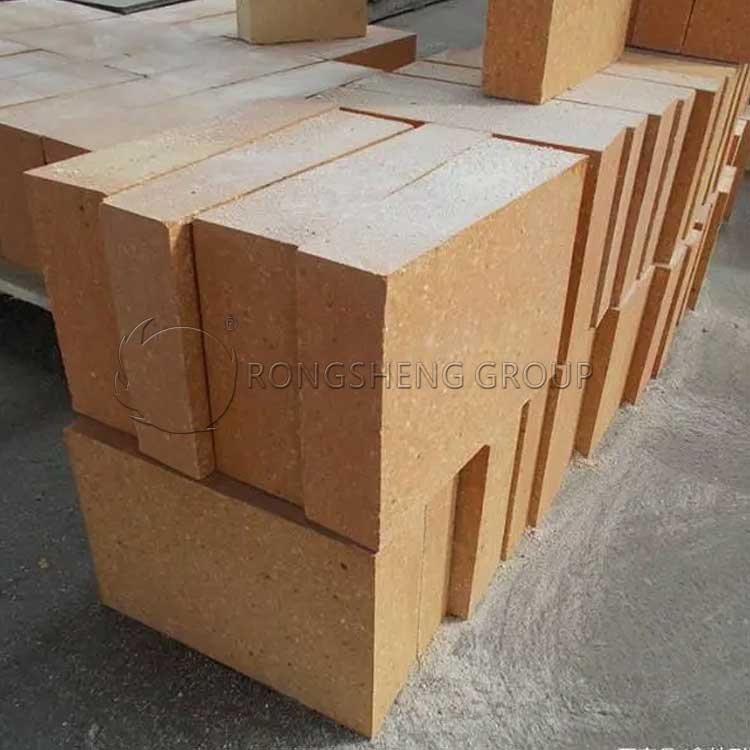
Additives in the Production of Zircon Refractory Bricks
The most commonly used sintering additive for producing zircon refractory bricks is refractory clay. When soft clay is used as a binder, clay with high plasticity, high refractoriness and low sintering temperature should be selected. Such as A2O3 (29%~32%), SiO2 (48%~50%), ignition loss of 15%~16%, refractoriness of 1730~1750℃. Plasticity index 1.95~2.96. Soft clay with a sintering temperature of about 1300℃.
With the increase of clay addition, the refractoriness of zircon bricks decreases significantly, and the load softening temperature also decreases. When the clay addition increases from 5% to 15%, the refractoriness of the product decreases from 1750℃ to 1680℃, and the load softening temperature decreases from 1700℃ to 1600℃. The amount of clay added and the firing temperature have an impact on the thermal shock resistance of zircon bricks. Reducing the amount of clay added is conducive to improving the thermal shock resistance of zircon bricks. Products made of all clinker have higher thermal shock resistance than those made of partly raw material.
The amount of clay added has a great influence on the sintering and high-temperature performance of zircon bricks. When zircon bricks with more clay are fired, a large amount of high-temperature liquid phase is formed. The high-temperature liquid phase fills around the zircon particles, promotes sintering, and is easy to densify. During the firing process, the liquid phase infiltrates into the cracked zircon particles, adding new reaction surfaces and promoting the decomposition of zircon. A more liquid phase reduces the refractoriness and load-softening temperature. When the temperature changes, there is a corresponding large volume change, which makes the thermal shock resistance of the product worse.
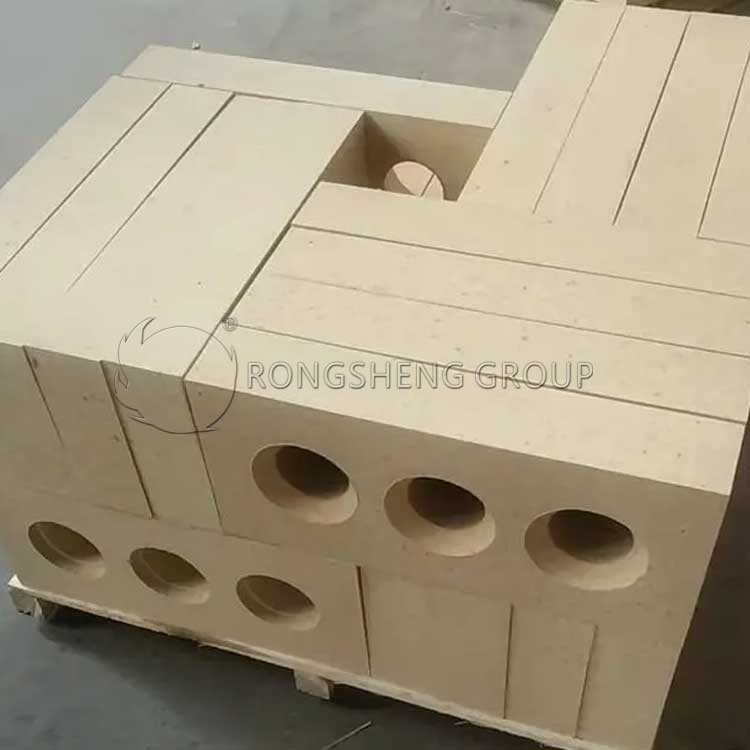
Production of Rongsheng High-Performance Zircon Bricks
Rongsheng refractory brick manufacturer, through actual experiments and customer feedback, found that when the critical particle size of the ingredients is slightly larger, greater than 3 mm, its thermal shock resistance is better.
In order to make the mud moisture uniform and make the clay plastic, the material should be trapped for no less than 48 hours.
Increasing the molding pressure is an effective measure to reduce the porosity of the product and increase the volume density. Therefore, the molding pressure should be above 85 MPa.
Control of firing temperature of zircon refractory bricks
The firing temperature of zircon refractory bricks is 1550~1650℃. To avoid large-scale decomposition of zircon, the firing temperature of zircon bricks should be controlled below 1600℃.
During firing, zircon decomposes at high temperatures. Pure zircon begins to decompose slowly at 1540℃ and rapidly at 1700℃. Factors affecting the decomposition of zircon include: impurity particle size in the raw material, heating temperature, insulation time, furnace atmosphere, heating rate and cooling rate, etc. Oxides with strong reactivity with SIO2 have a great influence on the decomposition of zircon, and follow the order of Group I>Group II>Group III in the periodic table. That is, alkali metal oxides (Na2O, K2O) are most likely to react with SiO2 to form a glass phase. The greatest influence on the decomposition of zircon reduces the temperature at which zircon begins to decompose.
Effect of adding micro powder on the performance of zircon bricks
Rongsheng zircon brick manufacturer has concluded through research that when about 30% of the zircon in the brick decomposes to form SiO2 and ZrO2, the product has a high resistance to slag penetration. At this time, the SiO2 glass phase has formed a continuous matrix. At high temperatures, the liquid phase exhibits high viscosity and makes the brick thermoplastic. From the perspective of corrosion resistance, it is better for the zircon particles in the zircon brick not to decompose. From the perspective of resistance to slag penetration, it is more advantageous to have a certain amount of decomposition to obtain a continuous high-viscosity SiO2 matrix. For this reason, the process adopts the addition of a certain amount of SiO2 micro powder or fused quartz powder to produce zircon products with a continuous SiO2 matrix. This type of zircon brick can be fired at a lower temperature and has better durability.
Sintering of pure zircon bricks
The sintering of pure zircon products is difficult and relies on solid phase diffusion at high temperatures, and its speed is very slow. The addition of certain oxides can promote sintering. Oxides such as Na2O, K2O, MgO, CaO, and B2O3 can promote sintering very effectively. But it also significantly promotes the decomposition of zircon. Oxides such as TiO2, P2O5, Fe2O3, BeO, and Cu2O can promote the sintering of zircon products without promoting the decomposition of zircon. Therefore, TiO2 and P2O5 can be used as sintering additives for zircon materials.
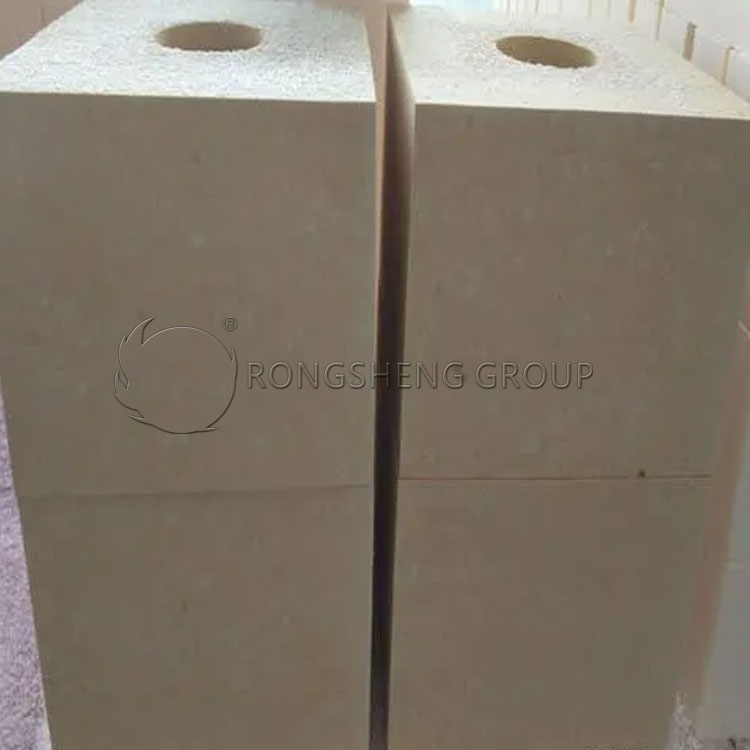
Production Technology of High-Quality Machine-Pressed Zircon Bricks
Grind the zircon raw material (containing ZrO264%~65%) to a particle size of <0.06 mm≥82%, use 7% starch slurry (powder:water=1:7) as the binder, and the molding pressure is 85MPa. The molding moisture of the green body is 4.5%~5.5%, the maximum firing temperature is 1600°C, and the temperature is maintained for 2~3 hours to produce zircon clinker with a water absorption rate of 4%~6%.
Zircon clinker is used as coarse particles with a particle size of 1.5~0.5 mm. Ball-milled powder with a particle size <0.06 mm and soft clay with a particle size ≤0.5 mm are used as fine powder. It takes 48 hours to batch, mix, and trap materials, and the molding pressure is 85MPa. The dry residual moisture of the bricks is ≤3%, the volume density of the semi-finished product is ≥3.1g/cm3, the firing temperature is 1550~1600℃, and the heat preservation is 3~4 hours. Zircon stone products with porosity ≤24%, volume density ≥3.2 g/cm3, normal temperature compressive strength 50~70 MPa, load softening temperature (0.2 MPa) 1510~1630°C, and ZrO2 56%~60% content were produced.
The production process of high-quality machine-pressed zircon bricks. First, zircon is sand-ground finely (<0.088 mm accounts for 97%) to synthesize clinker. Then break it into 5~3mm, 3~1mm, 1~0mm particles. Add a certain proportion of additives (TiO2 + Al2O3 + MgO) to the matrix, about 0.8% to 1.5%. Add 5%~25% zircon sand, and then bake it at 1550~1650℃ after shaping.
Rongsheng Refractory Brick Factory
Rongsheng Refractory Brick Factory is a powerful manufacturer and seller of refractory bricks. Rongsheng’s zircon bricks are highly dense, highly resistant to penetration, and have good thermal shock stability. If you need to buy high-quality zircon bricks, please contact Rongsheng. Direct shipment from the manufacturer, low price, fast delivery. Contact Rongsheng for more information and quotes for free.