When the magnesia carbon brick comes into contact with molten steel and slag, the slag corrodes the magnesia carbon clay brick. As a result, the thermal shock stability of the magnesia carbon brick is poor, and the phenomenon of peeling damage occurs. The service life of the slag line magnesia carbon brick is shortened, and the LF furnace refining production is affected. In order to extend the service life of magnesia carbon bricks, the researchers studied the influence of LF furnace slag on the corrosion resistance of magnesia carbon bricks. The ways to extend the life of magnesia carbon bricks for the LF slag line are discussed.
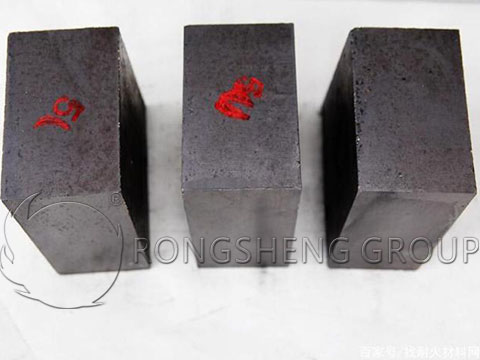
Experimental Materials and Process
Low-iron slag and high-iron slag used in LF furnace are used in the experiment. The magnesia carbon brick is selected from the slag line magnesia carbon brick MT-14 currently used by Angang.
After the researchers made the slag line magnesia-carbon bricks into crucible samples with an inner diameter of ф60mm × 50mm and an outer diameter of ф120mm × 100mm, the LF low-iron slag and high-iron slag were respectively charged into the prepared crucible. Keep the temperature at 1600℃ for 3h, and use the static crucible method to test the slag erosion resistance of magnesia carbon brick. They grind two kinds of LF furnace slag into 200 mesh fine powder, using novolac resin as the binder. Press it into a cylindrical sample of ф6mm × 5mm, and place it on a gasket made of magnesia carbon brick from the slag line. Then put it in the refractoriness tester DRH-III to observe the wetting angle between the slag and the magnesia carbon brick when the sample reaches the hemispheric temperature to characterize the wettability of the slag on the magnesia carbon brick.
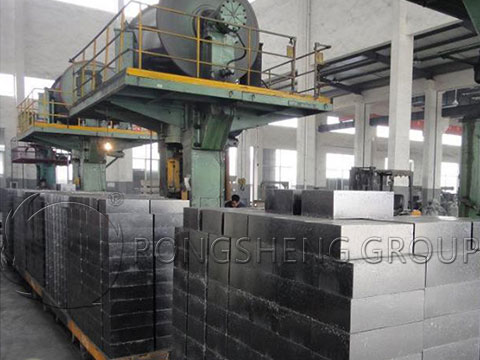
Experimental Results and Analysis
Wetting angle detection. According to the schematic diagram of the wetting angle of the two slags of the LF furnace on the magnesia carbon brick, the researcher calculated that the LF slag with less iron has a wetting angle of 45° for the magnesia carbon brick, and the LF slag with more iron wets the magnesia carbon brick. The angle is 58°. It can be seen that both slags of the LF furnace can wet the magnesia carbon bricks, and the slag with less iron wetting is more obvious, and the erosion of the bricks is more obvious. Therefore, the slag composition of the LF furnace can be adjusted within a certain range to increase the wetting angle of the slag to the product, thereby improving the corrosion resistance of the magnesia carbon brick.
Anti-slag erosion analysis. The SEM morphology of the magnesia carbon brick crucible after corrosion by the LF slag with less iron and more iron. After being corroded by LF slag, a thin slag layer was formed on the surface of the magnesia carbon brick, and the slag layer of the samples with less iron was relatively obvious. Due to the short erosion time, the erosion layer on the surface of the magnesia carbon brick is thinner after being eroded by the two slags. At the same time, the scaly graphite on the surface of the magnesia carbon brick in contact with the slag is oxidized, and the matrix is relatively loose. Moreover, the corrosion of low-iron LF slag on magnesia-carbon bricks is significantly stronger than that of high-speed LF slag, and the erosion layer is relatively deep. This is due to the relatively small wetting angle of low-iron slag to magnesia carbon bricks. Under the same conditions, the wetting rate of magnesia carbon bricks is fast, which accelerates the corrosion of magnesia carbon bricks.
The researchers further studied and found that the LF slag first wetted the surface of the magnesia carbon brick. Then along the pores left by the graphite oxidation, it intrudes into the matrix of the magnesia-carbon bricks, fills them around the magnesia particles, and chemically corrodes the magnesia particles to generate a low-melting liquid phase containing Ca, Si, and Al. Thereby gradually eroding magnesia particles. It can be speculated that as the reaction time increases, a cemented structure will be formed in the magnesia carbon brick. The magnesia particles will be embedded in the liquid phase, and the edges and corners of the magnesia particles will be eroded by the slag and become smooth. As a result, the composition and performance of the erosion layer of the magnesia carbon brick and the original bricklayer, especially the thermal expansion coefficient, are quite different.
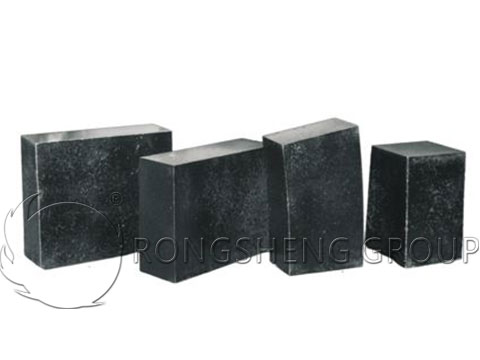
When subjected to thermal shock and thermal shock during use, the working surface of the magnesia carbon brick will be peeled off and damaged. Under the condition of refining outside the LF furnace, the viscosity of the slag decreases due to the high refining temperature. In addition, the internal temperature of the furnace lining is also higher, and the slag can penetrate deeper into the refractory bricks material to form a thicker reaction layer, which will aggravate the melting loss of the magnesia carbon brick lining. There was severe peeling and chip damage. Therefore, the impact of LF slag on magnesia carbon bricks is mainly manifested in the chemical attack and the resulting poor thermal shock stability, spalling damage.
In addition, the oxidation of carbon in MgO-C bricks and the influence of pores will also cause damage to the magnesia carbon bricks.
Due to the oxidation of carbon in the hot surface of the working lining, a thinner decarburized layer is formed, which is the primary cause of damage to the magnesia carbon brick. Due to the existence of open pores in the magnesia carbon brick, the damage of the magnesia carbon brick is aggravated. During the use of magnesia-carbon bricks, the pores play a catalytic role in the oxidation and destruction of carbon, and the slag erodes the brick lining more seriously. In this way, the magnesia carbon bricks are continuously corroded by the oxides in the slag passing through the pores and oxygen in the air, and the oxidation damage of carbon and the reaction between the slag and the MgO in the bricks are more intense, resulting in the damage of the magnesia carbon bricks. Due to the repeatability of the process, the damage of magnesia-carbon bricks is increasing.
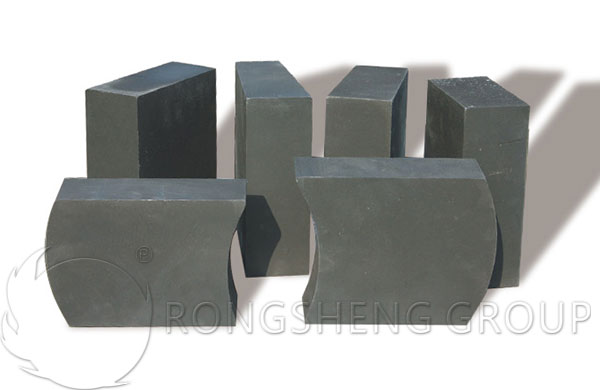
Ways to extend the life of magnesia carbon bricks for slag line
In summary, the wetting angle of the two LF furnace slags to the magnesia carbon brick is less than 90°, and it is easy to wet the surface of the magnesia carbon brick. The damage rate of the magnesia carbon brick will be accelerated when it comes into contact with the magnesia carbon brick, and the wetting of the low iron LF slag will be more obvious. In corrosion experiments, this phenomenon reduces the corrosion resistance of magnesia carbon bricks in contact with low-iron slag.
In order to extend the slag corrosion resistance life of LF furnace magnesia carbon bricks, we can adjust the composition of the slag and increase the wetting angle of the magnesia carbon bricks. A stable slag layer is formed on the surface of the magnesia carbon brick to prevent the oxidation of the surface graphite and inhibit the wetting of the surface of the magnesia carbon brick by the slag. Or by optimizing the matrix structure of the magnesia-carbon bricks, improving the introduction form and amount of graphite in the magnesia-carbon bricks, and adjusting the ingredient composition of the matrix. This will affect the number, size, shape, and distribution of the pores formed by carbon oxidation during the use of the magnesia carbon brick, thereby prolonging the service life of the LF slag line magnesia carbon brick.
Rongsheng refractory brick manufacturer
Rongsheng refractory brick manufacturer has advanced production and sales experience. Rongsheng’s refractory projects have spread to more than 60 countries around the world. And received unanimous praise from customers. Rongsheng’s refractory brick products not only serve LF refining furnaces but also provide high-quality refractory lining materials for various steelmaking and metallurgical equipment. If you want to know more about Rongsheng refractory material manufacturer or want to buy refractory material, please contact us. We will provide you with services according to your specific needs.