Sintered corundum brick has stable performance at high temperatures, and high melting points and the normal temperature compressive strength of corundum brick can reach 340MPa. The load softening start temperature is greater than 1700°C. It has strong resistance to acidic or alkaline slag, metal, and glass liquid.
Production Process and Characteristics of Sintered Corundum Brick
The production process of sintered corundum bricks is to crush sintered corundum to 3mm coarse particles and some fine powders less than 0.074mm in height. Then add a small amount of clay and other binders for mixing, and shape it with a high-pressure friction brick press or hydraulic press. The adobe is fired in a high-temperature chamber after being dried. Generally, the sintered corundum brick with higher purity has a firing temperature of 1750-1800°C.
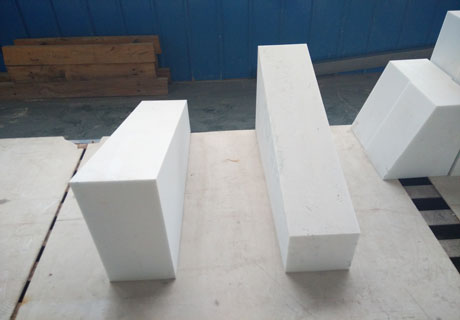
Sintered corundum bricks are fired at high temperatures in a shuttle kiln. It has the characteristics of high refractoriness, good thermal shock stability, high-temperature strength, strong slag resistance, small expansion coefficient, low creep, and spalling resistance. The thermal shock stability of corundum brick is related to its structure. Good corrosion resistance, but poor thermal shock stability. The bulk density is greater than 3.60g/cm3, and the porosity is less than 3%.
Characteristics of Sintered Corundum Bricks
Sintered corundum bricks are high-grade refractory materials, suitable for use in high-temperature kilns under various atmospheric conditions. High-quality high-purity corundum bricks are widely used in zirconia ceramics, fluorescent materials, electronic ceramics, and magnetic materials. High-temperature sintering of ceramic powder and gasification furnaces in the petrochemical industry, secondary reforming furnaces for synthetic ammonia, carbon black reaction furnaces, and high-temperature kilns for the glass industry. The dimensions, physical and chemical indicators, and service life of the products have met the requirements of high-temperature furnaces.
Sintered corundum bricks are mainly used in blast furnaces and refining furnaces outside the metallurgical industry. It is also used in ironmaking blast furnaces and blast furnace hot blast stoves, refining furnaces outside steelmaking furnaces, and sliding nozzles. Glass melting furnaces and petrochemical industrial furnaces are now used in a large proportion of glass melting furnaces in the market.
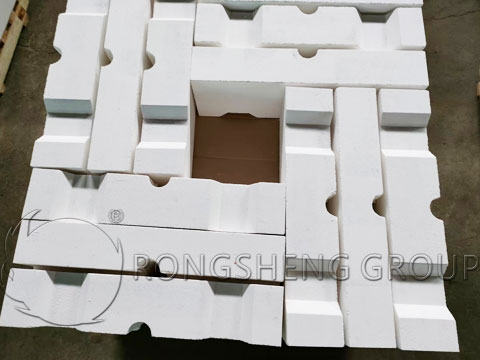
What are the Advantages of the Application of Sintered Corundum in High-Purity Corundum Bricks?
Corundum bricks are refractory products with corundum as the main crystal phase. Good chemical stability, and strong resistance to acidic or alkaline slag, metal, and glass liquid. It is mainly used in ironmaking blast furnaces, blast furnace hot blast stoves, refining furnaces outside steelmaking furnaces, glass melting furnaces, and petrochemical industrial furnaces. The high-purity corundum bricks currently on the market are mainly produced from fused corundum raw materials. The production of fused corundum has the disadvantages of high energy consumption, large loss, and environmental protection. The use of fused corundum raw materials to produce high-purity corundum bricks has the problem of being difficult to sinter and slag resistance needs to be improved.
Sintered corundum has high sintering activity, which can promote the combination of matrix and particles. Sintered corundum was introduced into the preparation of high-purity corundum bricks, and the effects of different sintered corundum on the properties of corundum bricks were studied. The results show that the grain size of sintered corundum particles is smaller and there are more pores. In the sintering process, it is beneficial to diffusion and mass transfer sintering and improves the sintering strength of corundum bricks. The tight combination of matrix and particles also improves the permeability resistance of corundum bricks.
Advantages of Sintered Corundum in High-Purity Corundum Bricks
Due to the small grain size of sintered corundum, there are more pores in the grains, which is conducive to diffusion and mass transfer sintering. Part of the pores is excluded from the crystal along the grain boundary with the migration of substances, resulting in volume shrinkage. As a result, the linear shrinkage of the sample increases with the increase of the content of sintered corundum, and the apparent porosity of the sample decreases with the increase of the content of sintered corundum.
The pure sintered corundum raw material has a fine-grained structure, high strength, and high sintering activity. The combination of sintered corundum particles and the matrix in the brick is good, so the mechanical strength performance increases with the increase of the content of sintered corundum.
The results of the static crucible slag resistance test show that sintered corundum can slow down the penetration of slag into the refractory bricks. There are two reasons for this result. One is that the apparent porosity of samples with high content of sintered corundum is low. The second is that the sintered corundum raw material particles are well combined with the matrix, which hinders the penetration of slag into bricks.