There are many ways to bake and open a lime kiln, and they should be selected according to the local conditions at the time. The service life of lime kiln refractory bricks is not only related to the design, material selection, and masonry level, but the success of baking also determines the effective use of the kiln. As the last link in kiln construction, the baking steps should be arranged reasonably according to scientific methods.
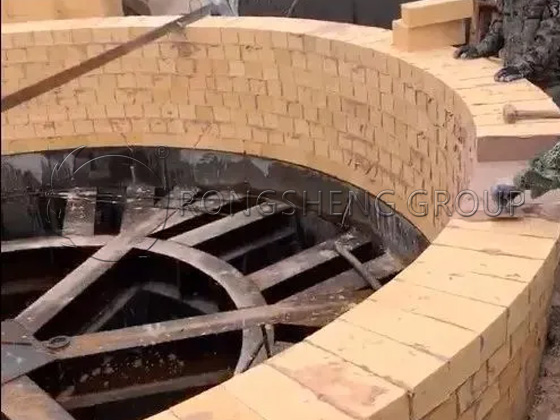
Drying and Starting of the Large Lime Kilns
Place a circular gas pipe on the spiral ash unloader under the kiln, install 12 gas nozzles at equal distances on the pipe, then ignite and heat up according to the temperature rise curve. It will be baked in about 48 hours. After cooling, remove the gas pipe and load the kiln, and open the kiln.
Make a manhole with a wooden board on one side of the wind cap to facilitate the transportation of materials when igniting and laying the kiln. Large pieces of quicklime (12-20 tons) are manually transported into the kiln to lay the kiln, and the height is 150-200 mm above the guard plate at the kiln wall. The center part is built into a crown shape, 200 mm above the wind cap. Small pieces of firewood (in bundles) are placed in a tic-tac-toe shape on the quicklime, forming a wind duct around it, about 300-400 mm high. A layer of shavings and waste oilcloth is laid on the firewood, and 2,000 kg of large firewood is placed on it. The top of the manhole is also sealed with firewood, and the manhole is also filled with shavings and waste oilcloth. Finally, about 4 tons of coke are thrown from the top of the kiln.
The kiln top flue and the kiln bottom door are half open, and then the waste oilcloth in the manhole is ignited with a torch. After the fire is slightly larger, the kiln top flue is fully opened for natural ventilation. When the color of the smoke discharged from the flue changes from yellow to thick smoke, the kiln bottom door can be closed, and then air can be blown in.
When the air supply starts, it should be handled according to the specific situation in the kiln. When the color of the flue smoke changes from yellow to black, and then from black to white, it proves that the combustion in the kiln is good and the wind pressure can be maintained at 20 to 40 mm water column. When the kiln top is completely white smoke, the air volume can be gradually increased until the surface smoke appears on the kiln top and the carbon dioxide content of the kiln gas reaches more than 20%. When the kiln top temperature is 100 to 150℃, a small amount of material can be added at intervals, and a small amount of ash can be discharged (commonly known as live kiln), and normal production can be gradually turned into normal production.
Lime Kiln Drying and Starting of Small and Medium-Sized Kilns
Put a small piece of limestone on the ash unloading machine at the bottom of the kiln, about 3 to 4 meters high, add about 500 kg of hardwood firewood, 200 kg of softwood firewood, and the appropriate amount of ignition materials such as shavings, and pour waste oil on it. Then use waste oil cloth to ignite it and throw it down from the top of the kiln. When thick smoke comes out of the flue, it means that the firewood has burned. In the future, add 500 kg of hardwood firewood every hour (depending on the combustion situation). If the fire is not strong, a small amount of wind can be sent in, so that it can be maintained for one shift. In the next few times of throwing hardwood firewood, about one ton of coke can be added as a primer in batches. Next, you can throw the mixed material, start with a small amount, and use a high ratio. Check at any time that the material surface is evenly red; otherwise, increase the air volume. In the future, the amount of material added will gradually increase, the fuel ratio will gradually decrease, and the material surface will not be required to be red. After 22 hours, start to unload the bottom stone and ash. Start with a small amount and gradually increase it later. As the amount of feed increases, the material level gradually increases, and it will return to normal after about 3 to 4 days.
Refractory brick Lime Kiln Baking Method
According to the different stages of the lime kiln in the construction and production process, the kiln baking method can be divided into: one-step method of kiln baking and kiln opening and two-step method of kiln baking and kiln opening.
The completed lime kiln or the kiln after major repairs is required to be put into production immediately. The kiln that is restarted after a non-maintenance shutdown or the kiln that has undergone medium or minor repairs should adopt the one-step method of kiln baking and kiln opening at the same time.
When the kiln construction time is short, the temperature in the kiln construction season is low, the environment is relatively humid, and the newly built lime kiln cannot be put into production immediately, the kiln baking method should adopt the two-step method of kiln baking and kiln opening separately.
Preparation work before refractory brick Lime kiln baking
In order to make the kiln baking work go smoothly, the following preparation work must be done before kiln baking.
- 1) After the kiln lining is built, the debris that may be brought in during the construction process and the equipment installation process should be cleaned up.
- 2) After the kiln lining is built, the quality of the masonry should be checked to see if it meets the requirements.
- 3) The feeding equipment, discharging equipment, and fans should be debugged and qualified.
- 4) The electrical equipment and contact signals should be fault-free.
- 5) The welding assembly of pipeline valves should be tight and leak-free.
- 6) The detection instruments on the kiln should be installed effectively.
- 7) The raw materials for kiln baking should be fully prepared.
- 8) The tools for operation should be fully prepared.
- 9) The safety protection measures are appropriate, and the safety equipment should meet the requirements.
- 10) Take timely measures to eliminate the faults found and handle them properly.
Prerequisites before refractory brick Lime kiln baking
The preparatory work before kiln baking should be confirmed to be all qualified, and the kiln baking operation can be carried out after natural drying for at least 15 days.
The ambient temperature during natural drying should be kept above 5℃.
When refractory castables are selected as the lining of a lime kiln, they must be cured according to regulations before the kiln baking operation can be carried out.
General operation of refractory brick Lime kiln
1) One-step kiln baking with simultaneous kiln baking and kiln opening.
First, cover the ash discharging mechanism at the bottom of the kiln, such as the ash discharging screw cone, ash tray or plate-type ash discharging machine, with lime blocks of a certain thickness and appropriate particle size for protection. Stack firewood on the formed protective layer and leave ignition holes. Stack an appropriate amount of coke on the firewood, and then add a mixture of limestone and coke on the coke layer to ignite the kiln. After ignition, the air supply volume should be controlled, and the temperature should rise slowly and evenly. The kiln heating experience of kiln baking and kiln opening of existing lime kilns with similar performance can be referred to determine the temperature measurement point and the total kiln baking and kiln opening time, formulate a kiln baking curve, and perform a kiln baking operation. After the kiln heating process is stable, materials can be gradually added and put into production.
2) Use the two-step kiln drying method with separate kiln drying and kiln opening
According to the specific conditions of the kiln construction site, the appropriate kiln heating method should be selected (such as generally using a small coke oven in the kiln, and sending warm air when conditions permit). The temperature in the entire kiln should reach and be maintained at around 150℃ for about two weeks to dry the free moisture in the masonry and prevent the kiln lining from freezing in winter.
After the kiln drying process is completed and passed the inspection, the kiln can be opened as needed according to the method in the previous paragraph.
Precautions for refractory brick Lime kiln baking
1) Reasonable kiln baking curve and kiln baking operation procedures should be formulated according to the specific conditions, such as the size of the kiln body, the structure of the kiln body, the type of refractory materials selected, the kiln construction environment, and the different construction seasons.
The kiln baking curve includes: kiln baking period, kiln baking maximum temperature, heating rate, kiln baking insulation temperature, insulation time, and cooling rate etc.
When the kiln lining is a refractory castable, the kiln baking curve should also be formulated according to its material, thickness, and molding process.
When the kiln lining is composed of different types of refractory materials, the kiln baking curve should be formulated according to the material characteristics and primary and secondary relationships.
2) Representative temperature measurement points should be set at appropriate parts of the kiln lining to monitor and control the temperature required for kiln baking.
3) The kiln heating should be uniform and slow, and sudden heating or cooling is strictly prohibited to avoid local overheating that may damage the refractory lining or nodules.
4) During the kiln drying process, if a fault occurs and affects the normal temperature rise, insulation measures should be taken immediately, and the temperature can be continued only after the fault is eliminated.
The kiln drying process should be recorded in detail. If abnormal phenomena occur, corresponding countermeasures should be taken, and the reasons should be noted.
5) When implementing the kiln drying operation, the kiln drying temperature should be measured and recorded as required, and the actual kiln drying curve should be drawn.
6) After the kiln drying is completed, when the kiln body temperature drops to normal temperature, relevant personnel must be organized in time to enter the kiln for cleaning and inspection, and the defects that have occurred must be corrected before it can be put into production.