During the long-term use of coke ovens, the furnace body will inevitably gradually aging due to high temperature, mechanical force, physical and chemical reactions. The generation of melt holes in the coke oven carbonization chamber is the main sign of coke oven aging. For repairing coke ovens, fused silica bricks or ordinary silica bricks are generally used.
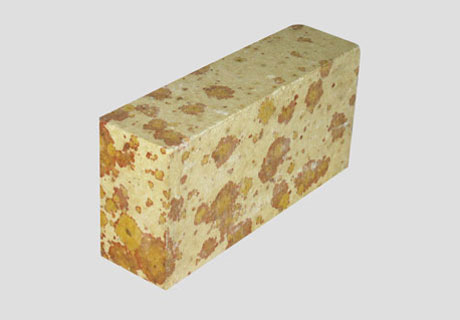
Coke Oven Repair Method
After the coke oven wall is damaged, the traditional cold repair technology needs to cool the repaired part to below 200 ℃, remove the old refractory bricks and re-build, and finally need to dry the oven. As the silicon brick cools to a temperature below the temperature point at which the silicon brick crystal form is transformed, the volume change caused by the crystal form transformation. It is very easy to cause the phenomenon of cracking at the connection part of the new and old furnace lining body, causing leakage.
The use of fused silica bricks in the coke oven for hot repair can effectively make up for the defect of the cold repair technology of the coke oven. The method of hot repair is under the temperature above 850 ℃, without the need for operators to enter the carbonization chamber. The operation of using special tools to send the fused silica bricks into the carbonization room for dry swing and then grouting. The temperature of the carbonization chamber can be kept in a fairly high range when using the hot repair of the fused silica bricks in the coke oven. Therefore, the construction period is relatively short, and the impact on the furnace wall is also small. Moreover, the use of fused silica brick as hot repair construction materials, no expansion joints can be reserved during repair, which has a considerable advantage compared to cold repair technology.
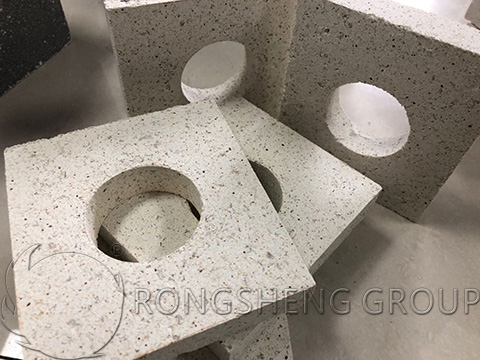
Physical and chemical indexes of fused silica brick and ordinary silica brick
Items | Fused Silica Bricks | Silica Bricks |
Apparent Porosity / % | ≤20 | ≤22 |
True Density / kg·m-3 | >1840 | ≥1850 |
Cold Crushing Strength / MPa | >30 | 19.6~29.4 |
Refractoriness Under Load / (℃) | 1660 | ≥1650 |
Linear Expansion / % | 0.16 | 1.2~1.4 |
Thermal Shock Resistance
(1100℃, Water quenching) / Cycle |
>30 | 1~2 |
SiO2 / % | >99 | 95 |
Al2O3 / % | <0.3 | 1.5 |
Fe2O3 / % | <0.2 | 1 |
CaO / % | <0.01 | 3 |
Na2O + K2O / % | – | 0.35 |
Advantages of Fused Silica Brick
The key point of hot repair technology in the coke oven is the use of fused silica bricks. Compared with ordinary silica bricks, fused silica bricks have the following advantages:
- The linear expansion rate is low. The linear expansion rate within 1000℃ is less than 0.16%, and the high-temperature volume is stable. During service, the structure of the kiln will not be stabilized due to thermal expansion;
- The product has high volume stability. Under normal circumstances, there will be no cracking or deformation. And the repair process does not need to stop the furnace, can be repaired directly under high-temperature conditions;
- Excellent thermal shock stability. During the service process, the product is placed at a high temperature of 1600 ℃, and it will not break or flake;
- The softening temperature under load is up to 1650℃ and the compressive strength is over 30MPa;
- High purity. The mass fraction of silica is greater than 99%. Strong anti-erosion ability, safe and reliable for long-term use.
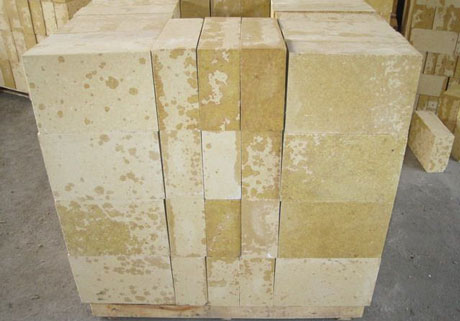
Rongsheng Refractory Brick Manufacturer
Rongsheng refractory brick manufacturer has more than ten years of production and sales experience. RS refractory bricks products have been sold to more than 60 countries around the world. Such as India, Pakistan, Kuwait, South Africa, Malaysia, Vietnam, Netherlands, Philippines, Singapore, Egypt, Russia, etc. If your thermal equipment needs to be repaired with refractory linings, such as high alumina bricks, fused silica bricks, mullite bricks, insulating bricks, etc. please contact us and leave your specific requirements. We will provide you with a high-quality refractory lining service.