The total length of the cement kiln is about several hundred meters. In addition to the complicated main system such as preheating and decomposition, there are also huge auxiliary systems such as ventilation and waste heat power generation. These systems are all under high temperature and require the protection of refractory bricks and castables. In addition, this huge main and auxiliary system is in a severely chemically corrosive working environment, and each part has many differences. High and low temperature, frequency and amplitude changes, the degree of airflow, the different forces, the magnitude of mechanical stress, and the degree of wear of the raw clinker. The internal situation is complicated. Requirements of Refractory Materials for Cement Kilns are strict. Therefore, the performance requirements of the cement kiln lining for refractory bricks and castables are very complicated.
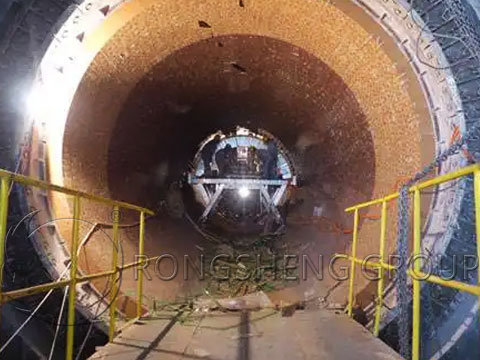
Reasons for the Damage of Refractory Materials Used in Cement Kilns
The causes of damage to refractory materials used in cement kilns can be roughly divided into:
- Thermal shock cracks and mechanical stress damage alkaline flaking.
- Abrasion airflow scours material wear.
- Damage caused by non-material properties such as construction and maintenance.
Therefore, we must be more cautious in the selection of refractory materials.
Requirements of Refractory Materials for Cement Kilns
Although the use environment of refractory materials for cement kilns varies greatly, they also have some things in common. Severe chemically aggressive atmosphere. Larger mechanical stress and wear, strong thermal shock stress. Therefore, a series of refractory bricks and castables must be used. The temperature of each part of the cement kiln varies greatly. Therefore, the main requirements for refractories are: strong chemical resistance, high strength, wear resistance, and strong thermal shock resistance. The refractoriness of refractory materials used in different parts is quite different.
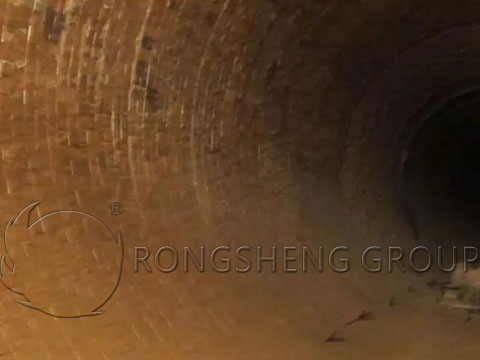
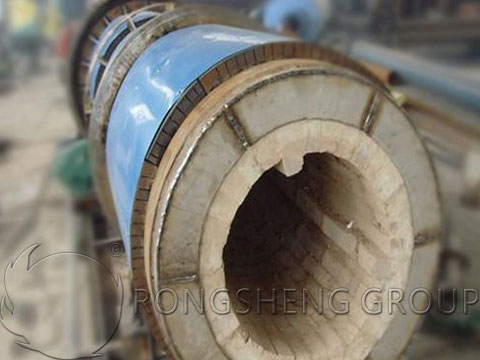
Main Features of New Dry-Cement Kilns
The inner lining has a large contact surface with a high temperature, and the gas temperature in the kiln exceeds 1800℃ at the hottest part. Therefore, only alkaline refractories can withstand chemical reactions with cement clinker, fuel ash, kiln dust, and various gases, and can withstand higher thermal loads.
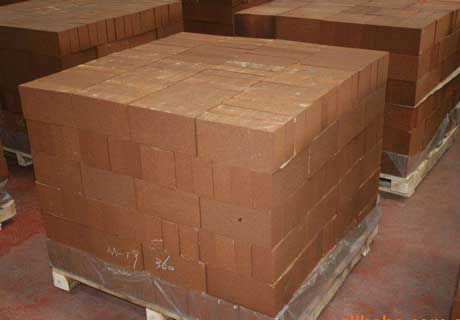
Requirements of Refractory Materials for New Dry-Cement Kilns
- It is easy to hang and protect the kiln skin
The temperature of the magnesia spinel brick can be maintained at about 600-800℃ on the hot surface. The thermal expansion rate of the hot surface layer is only 0.6%-0.7%. At this time, the refractory bricks are relatively stable and not easy to burst. If exposed to a flame above 1700°C, the temperature difference stress in the refractory material exceeds the strength of the brick itself when the temperature is raised, and cracking and peeling cannot be avoided. Alkaline bricks are conducive to clinker reaction and hang well on the kiln skin.
- Good chemical resistance
Under the high temperature of the firing zone, the refractory material undergoes a strong chemical attack. When the material in the firing zone contains 28% of the liquid phase, it will easily corrode the refractory. Magnesite bricks and dolomite bricks are all alkaline, so they can resist the erosion of clinker. Moreover, the gas produced by combustion and the sulfur, chlorine, alkali, etc. volatilized from the material have a strong chemical attack on various refractory materials.
- Good thermal shock resistance
When the kiln is shut down, opened, and the operation of the rotary kiln is unstable, frequent opening and shutting of the kiln will cause the temperature to change sharply, resulting in aggravated thermal shock damage.
Under normal circumstances, the time for each revolution of the rotary kiln is less than 1 min. When the kiln rotates once, the refractory materials in the kiln, including the kiln skin of the burning zone, are exposed to the hot kiln gas once and are covered by the materials for the rest of the time. In this way, the surface temperature of the refractory material in the kiln will experience periodic fluctuations with a temperature difference of up to 400°C. The inside of the refractory is still at a relatively low temperature, and the temperature difference between the inside and outside of the refractory will cause internal thermal stress and cause damage.
- Sufficient load softening temperature and refractoriness
The refractory materials used in the firing zone should have minimum refractoriness of 1730°C or more. Generally, the alkali bricks used in the firing zone have refractoriness greater than 1750-1790°C.
The load softening temperature of the refractory brick refers to the temperature at which the refractory brick starts to soften when it is subjected to a pressure of 0.2 MPa. The load softening temperature of magnesia bricks is about 150°C higher than the clinker firing temperature. Higher load softening temperature is not desirable, because alkaline bricks will make it difficult to form kiln skins.
- Proper porosity
The lining of the rotary kiln has strong chemical erosion and penetration. If the porosity is too large, the flue gas and liquid phase will easily penetrate and deposit harmful components, which will damage the kiln lining. However, the porosity is not as low as possible, and the apparent porosity is best maintained between 16%-18%.
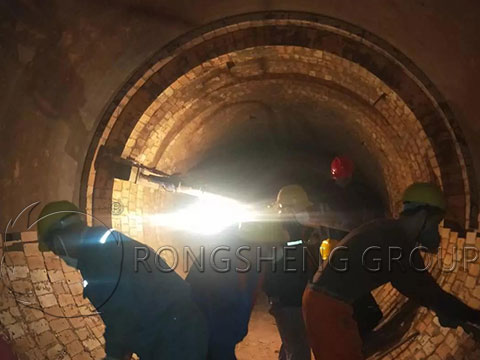
Refractory castables are commonly used in cement kilns. Among them, the commonly used refractory castables are special castables for kiln mouths, special castables for coal injection pipes, silicon carbide anti-skinning castables, high-performance castables, steel fiber reinforced wear-resistant castables and high-strength alkali-resistant castables. Due to the different properties of different types of refractory castables, they have their own advantages and disadvantages in use. It can be selected according to the needs of different parts of the cement kiln. For more prices of refractory materials for cement kilns, please leave your specific requirements on the form of the page. Quality RS Refractory Fire Bricks for sale. Rongsheng’s refractory service will not let you down.