RS Refractory Fire Bricks Factory can Provide clay insulation bricks with a good heat insulation effect, lightweight refractory bricks with various body densities, and special-shaped lightweight insulation bricks that can also be customized. Clay insulation bricks generally refer to refractory bricks with a density of 0.6-1.5g/cm3, and the national standard size is 230*114*65. RS Refractory Factory recommends choosing the appropriate lightweight refractory brick material according to the use environment.
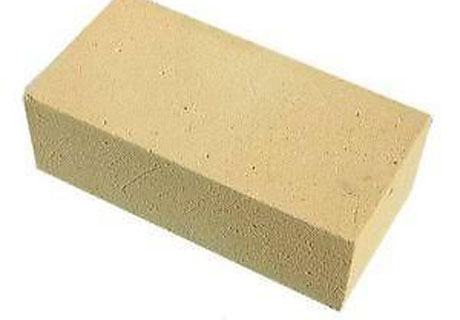
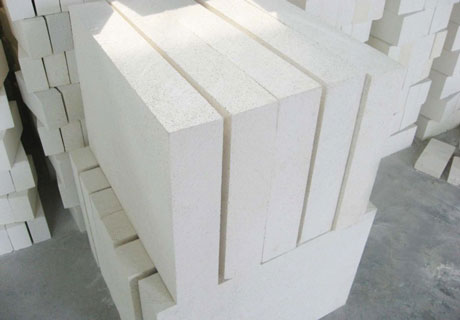
Lightweight insulation bricks can be divided into lightweight clay bricks, high alumina poly light ball bricks, mullite poly light insulation bricks, diatomite insulation bricks, floating bead insulation bricks, and acid-resistant bricks according to their materials. Lightweight insulation bricks are often used in the refractory industry to reduce the temperature of the outer wall of the kiln body improve working conditions and save fuel costs.
Lightweight insulation bricks are mainly used to deal with the heat storage loss of industrial kiln masonry and the heat loss of the furnace surface because these heat losses generally account for about 24-45% of fuel consumption. Using lightweight bricks with low thermal conductivity and small heat capacity as the furnace body structure material can save fuel consumption. At the same time, the kiln can also heat up and cool down quickly, which can improve the production efficiency of the equipment. It can also reduce the weight of the furnace body and simplify the structure of the furnace. Ultimately, product quality can be improved, ambient temperature can be lowered, and working conditions can be improved. 1.0 Precautions for lightweight insulation brick products.
- Lightweight insulation bricks have large porosity and loose structure, so they cannot be used in parts that directly contact slag and liquid metal.
- The mechanical strength is low and cannot be used for load-bearing structures.
- The wear resistance is very poor, so it is not suitable to be used in the parts that are in contact with the furnace material and have serious wear.
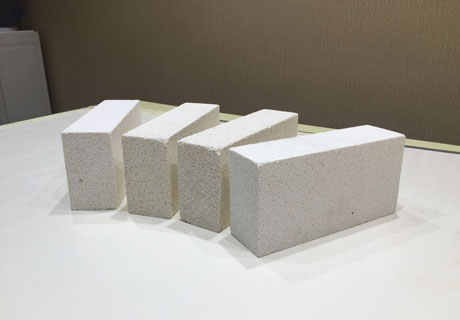
What is Light Weight Fire Bricks?
Lightweight insulation brick is a kind of heat insulation material. It refers to insulation bricks with high porosity, low bulk density, and low thermal conductivity. Lightweight insulation bricks are characterized by a porous structure (the porosity is generally 40-85%) and high thermal insulation.
- (1) Lightweight insulation bricks are classified according to volume density. The bulk density of 0.4 ~ 1.3g/cm3 is light insulation brick. Those below 0.4g/cm3 are ultra-light insulation bricks.
- (2) Lightweight insulation bricks are classified according to the use temperature. Use temperature 600 ~ 900 ℃ for low-temperature insulation material. 900~1200℃ is medium-temperature insulation material. Those over 1200°C are high-temperature insulation materials.
- (3) Lightweight insulation materials are classified according to the shape of the product. One is stereotyped lightweight insulation bricks, including clay insulation bricks, high alumina insulation bricks, silicon insulation bricks, and some pure oxide lightweight insulation bricks. The other is amorphous lightweight thermal insulation materials, such as lightweight thermal insulation castables.
The most common standard size of lightweight insulation bricks (lightweight refractory bricks) is T-3 (230*114*65mm). According to the size specification, it is divided into general refractory bricks and special-shaped refractory bricks. The universal size means that it can be used in conjunction with lightweight insulation bricks (lightweight refractory bricks) of other sizes during construction to complete the masonry of the kiln insulation layer. Then the specifications of general lightweight insulation bricks (lightweight refractory bricks) include T3, G1, G2, G3, G4, G5, G6, and other specifications of refractory bricks. The dimensions are: 230*114*65mm, 230×150×75mm, 345×150×75mm, 230×150/135×75mm, 345×150/130×75mm, 230×150/120×75mm, 345×150/ 110×75mm.

Lightweight insulation bricks (lightweight refractory bricks) also include the size of wedge-shaped and some special-shaped bricks. Wedge shape refers to a six-sided brick body with at least two end faces, sides, or large faces that are symmetrical trapezoids. The specifications of common wedge-shaped lightweight insulation bricks (lightweight refractory bricks) are Tc21, Tc22, Tc23, Tc24, Tc25, Tc26, Tc27, Tc28, Tc29, Tc30, and other specifications of refractory bricks. Sizes are: 114×65/35×230mm, 114×65/45×230mm, 114×65/55×230mm, 114×55/45×230mm, 114×75/45×230mm, 114×75/55× 230mm, 114×75/65×230mm, 114×70/60×230mm, 114×85/55×230mm, 114×80/50×230mm. Specifications for lightweight bricks. The specifications of lightweight bricks are generally common, and the purchased quantity is T-3 (230*114*65mm) standard bricks, which are converted into about 588 pieces per cubic meter. Due to the different densities of the material, the weight per cubic meter is different. The body density of the commonly used light-temperature brick is 0.5-1.0g/cm. Then each cubic meter is about 500kg-1000kg. The size of the general refractory brick is convenient for the masonry of the industrial kiln, and the reasonable refractory brick is matched with the masonry to make the kiln lining more tightly. When choosing the size of lightweight insulation bricks (lightweight refractory bricks), you can choose according to the common size combined with the structure of the actual part of the kiln.
High Alumina Lightweight Refractory Bricks. The aluminum content in the high-alumina lightweight insulation brick is not less than 48%, and it is made of other mineral clay clinker as raw materials. The refractory temperature is high, and it is usually distinguished according to the density, which is divided into a density of 1.0 and a density of 0.8. Since refractory bricks with low density are not easy to form during the production process, appropriate perlite minerals need to be added. Lightweight high alumina refractory bricks have the advantages of high refractory temperature, high compressive strength, low thermal conductivity, and good thermal insulation performance. High-aluminum lightweight insulation bricks with a density between 1.3-1.5. High-aluminum lightweight insulation bricks are usually used in tunnel kilns, shuttle kilns, wall kilns, and also in various heating furnaces and coking furnaces in the steel industry, as well as other thermal equipment, heat treatment lining materials, and other insulation parts.
High alumina poly light brick. High-aluminum poly-light bricks are used. High-alumina poly-light bricks have reached various technical indicators of similar products, and are currently a new material that must be selected in the design of industrial kilns. It is widely used in kiln lining (not eroded by solution) and insulation layers in metallurgy, machinery, ceramics, and chemical industries. It is an ideal energy-saving product. Its use temperature is below 1350°C.
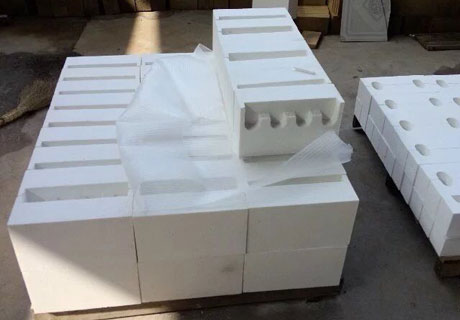
How to Choose the Right Lightweight Firebrick?
RS Refractory Fire Bricks Factory can provide high alumina bricks, clay bricks, insulation bricks, refractory castables, and customized refractory processing. Lightweight clay bricks mainly play the role of heat insulation for kilns, and the specific gravity is divided into 1.2, 1.0, 0.8, and 0.6.
In general, 1.0 is more commonly used. However, some furnace linings have a high temperature, and the weight of the furnace lining must also be considered, so light bricks with a specific gravity of 0.8 or 0.6 should be used.
If it is a shaft furnace or a pellet furnace, it is enough to use light bricks with a specific gravity of 1.0. If it is a blast furnace or hot blast furnace, choose 1.0 or 0.6 lightweight clay bricks according to the location and temperature.
Of course, the preheater of the lime kiln uses light bricks with a specific gravity of 1.0, and it is not necessary to use 0.6 specific gravity bricks. The temperature in this part is not high, and the lightweight brick with a specific gravity of 0.6 has a good heat insulation effect, but its strength is low. It is not good to choose bricks with a specific gravity of 0.6 when the temperature is not high. If the strength is low, they will be crushed and the insulation space will change. Thus affecting the use of refractory bricks in the working layer.
According to practical experience, the furnace wall of some calcium carbide furnaces uses light clay bricks, and the specific gravity is changed from 0.8 to 1.0. However, in the process of use, the insulation bricks have low strength and are crushed, and the crushed bricks become bricks, and the insulation layer changes, and there will be upper voids from top to bottom. So that the refractory bricks of the working layer began to loosen and fall from the upper part. Therefore, the specific gravity selection of lightweight clay bricks is also very important.
When choosing a specific gravity, you can’t just choose the lightest one. Although the insulation effect is good, the strength is not high and it will break. On the contrary, it will not have the effect of heat insulation. Moreover, the price of light clay bricks is different with different specific gravity. The lighter the more expensive, the furnace with low temperature uses high-priced bricks, which not only does not work but increases the production cost.
Therefore, it is more appropriate to choose a specific gravity of 1.0 for a furnace with a low temperature. If the furnace is too high, 0.6 lightweight clay bricks can be used as the thermal insulation layer. If the temperature is not high, you can choose 0.8 or 1.0, or 1.2 specific gravity.
Buy high-quality lightweight insulation bricks, 0.8 clay insulation standard bricks, and 1.0 lightweight insulation bricks. For high-alumina lightweight insulation bricks with a density between 1.3-1.5 and a temperature of 1600-2000 degrees, please contact RS Refractory Fire Bricks Factory, at sales@rsrefractoryfirebrick.com.