Sintered AZS bricks for glass kilns are a refractory material used in glass kilns using zircon and alumina as the main raw materials. Among them, AZS represents A12O3, ZrO2 and SiO2 respectively. AZS #33, AZS #36, AZS #44. It is an indispensable refractory material in key parts of the glass kiln. It can be in direct contact with the molten glass and can resist the erosion of the molten glass.
Characteristics of Sintered AZS Bricks for Glass Kilns
- High refractory resistance. Sintered AZS bricks have high refractory resistance and can reach over 1790℃. They are advanced refractory materials.
- The softening temperature under load is high. Sintered AZS bricks have less impurities, and the load-softening temperature of aluminum-zirconium products can be above 1550-1650°C.
- Good thermal shock resistance. Sintered AZS bricks for glass kilns have good thermal shock resistance.
- Good chemical resistance. Aluminum and zirconium products refractory products are very resistant to corrosion and oxidation and reduction reactions of acidic or alkaline slag and molten metal, and are enhanced as the AL203 content increases and the harmful impurity content decreases.
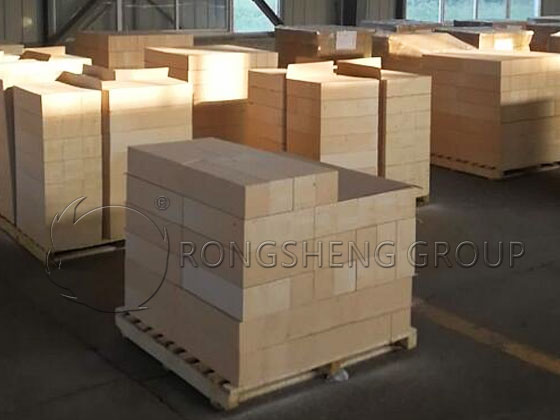
Refractory Bricks for Glass Kilns
The rapidly developing glass industry is also promoting the continuous development and innovation of refractory material technology used in glass kilns. Today’s glass industry requires refractory materials to not only improve combustion intensity but also improve heat transfer efficiency. At the same time, it is also necessary to ensure the reduction of heat loss and reduce environmental pollution.
The continuous advancement of glass furnaces is also forcing our refractory materials to make changes. This will require refractory materials to withstand higher temperatures, more rapid temperature changes, a series of chemical attacks, and more severe stress damage. As the basic material of glass kilns, refractory bricks for glass kilns continue to develop and innovate, thereby achieving energy conservation, emission reduction, and cost reduction in the glass industry.
Improvement of Sintered AZS Brick Production Technology
Select raw materials that meet the purity requirements, pre-synthesize, crush and classify some raw materials, and batch ingredients according to ingredients, process requirements and particle level. Appropriate binders are added to the ingredients, followed by mixing, high-pressure molding and high-temperature sintering to produce AZS bricks that meet the performance requirements. Thereby improving the problems that occur in the use of existing sintered AZS bricks.
By analyzing the performance requirements and usage conditions of refractory materials after full insulation of large float glass melting furnaces, and analyzing the use conditions and damage causes of existing sintered AZS bricks in melting furnaces. After comprehensive consideration, it is believed that high-grade sintered AZS refractory bricks that can be used under the temperature conditions of the insulation furnace for a long time should form a symbiotic crystal phase structure of baddeleyite, mullite and corundum, and strictly limit the proportional phase amount. Based on this understanding, the material composition that forms the desired crystal phase is set and the formula is designed. In actual production, strict attention must be paid to the purity requirements of raw materials. The presence of impurities, especially the presence of R2O components, not only affects the decomposition of ZrSiO4, but also affects the reaction of the decomposed products and the newly formed phase structure, easily forming a glass phase. Therefore, a slight increase in impurity content will have a significant impact on product performance.
Using relatively pure raw materials can cause ZrSiO4 to decompose during the sintering process of the sample. The SiO2 generated by the reaction is an amorphous phase, which only exists momentarily, and further reacts with AL2O3 to form mullite as the temperature continues to rise. It avoids the inhibition of the formation of mullite by Na2O, greatly reduces the amount of glass phase in the product, and is beneficial to improving the performance of the product. Sintered AZS bricks should have a relatively stable and uniform phase composition to avoid reactions between uneven phases under the action of high-temperature glass solution for a long time. In order to enable it to operate stably for a long time in high-temperature glass solution, for this reason, the performance indicators and crystal phase structure of the raw materials, the proportion of the ingredients, and the required particle size composition of the ingredients must be strictly controlled in the sintered AZS bricks.
High density and strength are closely related to the product’s corrosion resistance and high-temperature performance. In order to increase the density of the green body during the production process, it needs to be formed under a mechanical press of more than 650T and the particle size composition should be reasonably matched to comprehensively promote the increase in density.
High-quality AZS bricks for glass kiln. For repair and replacement of glass furnace refractory lining, please contact us and we can provide free solutions and quotations.