As a composite refractory material, magnesia carbon brick effectively utilizes the strong slag erosion resistance of magnesia and the high thermal conductivity and low expansion of carbon. It compensates for the biggest shortcoming of poor peeling resistance of magnesia. Magnesia-carbon bricks can be used on the ladle lining, and their main features are good high-temperature resistance, strong slag resistance, good thermal shock resistance, and low high-temperature creep. Rongsheng refractory brick manufacturer has many years of production and sales experience, providing high-quality magnesia carbon bricks for ladle lining.
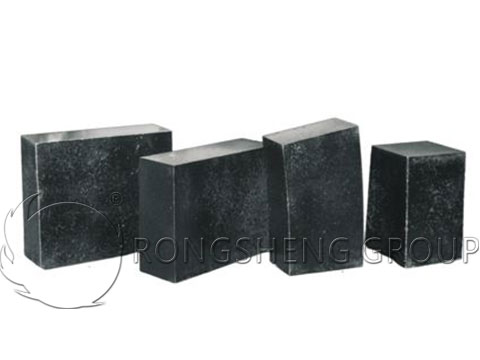
Advantages of Using Magnesia Carbon Brick on Ladle Lining
The refractory materials used in the early ladle slag line were directly combined with magnesia-chrome bricks, fused magnesia-chrome bricks, and other high-quality alkaline bricks. After the MgO-C brick was successfully used in the converter, the refining ladle slag line also began to use MgO-C brick and achieved good results. Even so, the use of magnesia carbon bricks in the ladle lining is not perfect.
Refractory brick manufacturers, in order to improve the oxidation resistance of MgO-C bricks, often add a small number of micro-powder additives. Common additives are Si, Al, Mg, Al-Si, Al-Mg, Al-Mg-Ca, Si-Mg-Ca, SiC, B4C, BN, and recently reported additives such as Al-B-C and Al-SiC-C series, etc.
The action principle of additives can be roughly divided into two aspects. On the one hand, it is from a thermodynamic point of view. That is, at the working temperature, the additive or the additive reacts with carbon to form other substances, which have a higher affinity with oxygen than carbon and oxygen and are oxidized prior to carbon to protect carbon. On the other hand, consider it from a dynamic point of view. The compounds formed by the reaction of additives with O2, CO, or carbon change the microstructure of carbon composite refractories. Such as increasing density, blocking pores, hindering the diffusion of oxygen and reaction products, etc. So, what are the specific functions of these additives in magnesia carbon bricks?
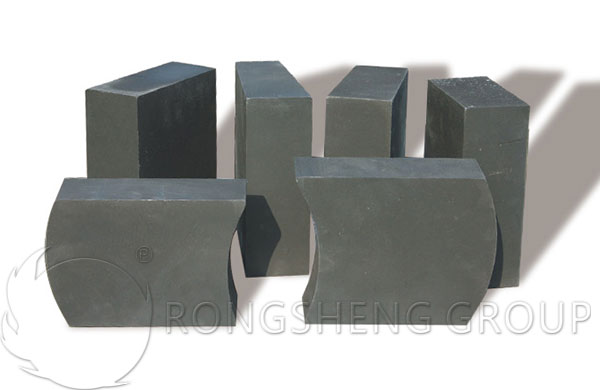
What are the functions of micro-powder additives in magnesia carbon bricks?
The oxidation resistance mechanism of Si powder is added. In magnesia-carbon refractories, the added Si powder will react with C(s) in the environment to form β-SiC. When the heat treatment temperature exceeds 1100°C, this reaction will occur violently. When the heat treatment temperature is around 1200°C, Si will also react with N2 in the environment to form Si3N4. In addition, when the heat treatment temperature is in the range of 1100°C-1500°C, glassy SiO2 will also be formed. SiC and Si3N4 in the material react with CO to form SiO(g), which will be further oxidized to form SiO2, which will deposit in the pores, block the pores, and reduce the diffusion flow of oxidizing gases. Thereby improving the oxidation resistance of magnesia carbon bricks. When the heat treatment temperature is higher than 1500°C, Si will eventually generate forsterite, and M2S will also block the pores and increase the strength of the material.
Add the anti-oxidation mechanism of SiC. SiC is added to the magnesia-carbon refractory material, although SiC cannot be oxidized preferentially over C to improve the oxidation resistance of the material. However, the process of SiC being oxidized to SiO2 is accompanied by a large volume expansion. At the same time, SiC will eventually transform into a forsterite phase and deposit in the pores to block the pores. Reduce the diffusion flow of oxidizing gas and improve the oxidation resistance of magnesium carbon refractories.
Oxidation resistance mechanism of Al powder added. In magnesia-carbon refractories, when the heat treatment temperature is 660 ° C, the added metal Al powder reacts with carbon in the material or nitrogen in the air to form Al4C3 and AlN. And these two substances will change under CO atmosphere, that is, Al→Al4C3→Al2O3, Al→AlN→Al2O3, Al→Al4C3→AlN→Al2O3. And no matter which process occurs, it will eventually be transformed into a stable phase of Al2O3. On the one hand, this change process is accompanied by changes between gas phases such as Al(g), Al2O(g), AlO(g), AlO2(g), AlN(g), and AlC(g). Not only can it block the pores, reduce the apparent porosity of the material, and make the structure of the material more compact. Moreover, the effective contact area between the oxidizing gas and the material is reduced. On the other hand, Al and Al4C3 will react with CO to release C and Al2O gas, and Al2O(g) will continue to diffuse outward. When the gas diffuses to the surface of the refractory material, due to the high partial pressure of oxygen, Al2O(g) will be transformed into Al2O3 and deposited in the pores to form a protective layer, while blocking the pores. Inhibit the further diffusion of gas and play the role of anti-oxidation. Al2O3 will also react with MgO in the material, and finally produce magnesium aluminum spinel, MA will also block the pores and improve the oxidation resistance of the material.
Manufacturer of Magnesia Carbon Bricks for Ladle
With the advancement of smelting technology, there are new requirements for refractory materials. In the long-term application practice, traditional magnesia-carbon bricks will also be replaced by low-carbon magnesia-carbon bricks. Manufacturers of magnesia-carbon bricks for ladles are also keeping up with the pace of development, making unremitting efforts to solve the problems of thermal shock stability and slag-resistant permeability caused by the reduction of carbon content in magnesia-carbon bricks. Rongsheng refractory brick manufacturer is committed to refractory materials for high-temperature kiln lining and provides solutions for ladle lining. Contact us for free samples and price information.