Fused cast zirconium corundum (AZS) bricks are mostly used in the highest temperature parts of the tank kiln and the parts most severely corroded by the glass liquid. Different brick models are usually marked by the amount of ZrO2 they contain. The brick is mainly composed of two crystal phases of α-corundum and baddeleyite and a glass phase. Except for the eutectic of α-corundum, baddeleyite is in free form. The more ZrO2 there is in the brick, the more free baddeleyite there is. The corrosion resistance of these two crystal phases is very good, and the two crystal phases are closely combined and the structure is uniform and dense, so the corrosion resistance is stronger. Due to the introduction of a small amount of Na2O into the brick, the mullite crystallization zone is reduced. The mullite crystal phase is difficult to precipitate, and a glass phase is formed to fill between the above crystal phases. This glass phase is eroded by high-temperature glass liquid to form albite glass with greater viscosity, which has a greater viscosity due to a certain amount of ZrO2 dissolved in it. This layer of high-viscosity glass stays on the brick surface and is not easy to spread, thus protecting the brick body. If the crystals of the bricks are coarse and it is difficult to form a high-viscosity layer after being corroded, the glass liquid will easily penetrate into the bricks and erode the bricks faster.
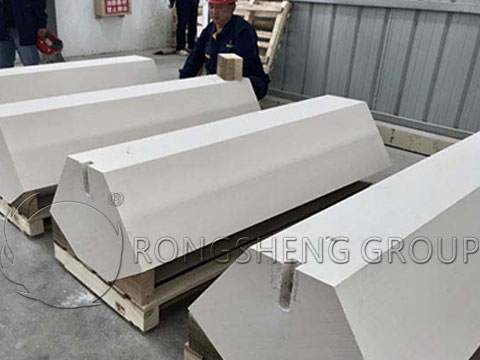
Alteration Process of Zirconium Corundum Bricks
The alteration process of zirconium corundum bricks begins with the interaction between the molten glass bricks and the original glass phase in the bricks, gradually diffusing and dissolving. Afterwards, the α-corundum and clinoclinite in the brick slowly dissolve in sequence. The viscosity of the glass liquid near the brick surface increases, forming a protective layer against erosion. At the same time, the metasomatic reaction will produce α-corundum, nepheline, skeleton baddeleyite, etc. Usually, for bricks near the liquid level on the upper part of the pool wall, the glass liquid in the metamorphic layer has obviously penetrated into the brick body, but the corundum and baddeleyite eutectic are still connected by the remaining glass. The surface of the bricks in the lower part of the pool wall is α-corundum, baddeleyite residues, and turbid glass phase. Due to the reaction between the glass phase in the brick and the glass liquid, a nepheline liquid phase is generated, which dissolves part of the zircon and forms a high-viscosity metamorphic layer. When the temperature decreases, the dissolved ZrO2 will precipitate star-shaped or dendritic crystals, which is the secondary crystallization of baddeleyite. In the high-viscosity layer at the lower part of the pool wall, mostly baddeleyite secondary crystals and nepheline crystals coexist. As the use time increases, these two crystal phases may be taken away by the glass liquid flow and then further diffused into the glass liquid. Baddeleyite, which is more difficult to melt, may partially dissolve and remain in the molten glass as stones in the finished product.
In some cases, the pool wall bricks are not one piece for the entire depth of the pool but are laid in layers, which results in horizontal joints. Erosion is prone to occur at horizontal joints. The erosion conditions of fused cast zirconium corundum bricks and sintered clay bricks are different. Clay bricks are basically eroded equally above and below the horizontal joints, while zirconium corundum bricks are severely eroded above the horizontal joints and slightly eroded below the horizontal joints. This upward drilling-like erosion process is roughly as follows. There are gaps in the horizontal seams of the pool wall, and molten glass can easily take advantage of them. At this time, the bricks above the horizontal joint will be eroded by the glass liquid below and form a high-viscosity protective layer. This protective layer tends to flow downward under the influence of gravity. Due to the loss of this high-viscosity layer, newly exposed brick surfaces will be subject to new erosion. At this time, there will be some bubbles at the top of the eroded layer, thus intensifying the erosion. As a result of this repeated action, the bricks above the horizontal joints are subject to strong upward drilling erosion. The protective layer of the bricks at the lower part of the horizontal joint will not be lost, and there will be no air bubbles staying on the lower surface, so it will be less eroded. Nowadays, due to the increase in kiln temperature and the use of auxiliary electrofusion and bubbling technology, erosion above the horizontal joints is more serious. Therefore, the design of the entire pool wall tile is often used.
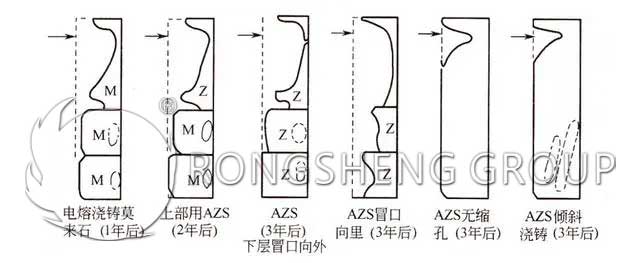
Zirconium corundum bricks made in a reducing atmosphere have poor corrosion resistance. This is because the electric furnace uses graphite electrodes and graphite furnace linings to create a reducing atmosphere. C and CO will reduce part of Fe2O3, TiO2, and SiO2 in the melt to low-valent oxides, increasing the components, and the softening temperature of the glass phase in the brick will drop by 100~150°C. When this kind of brick is used at high temperatures, the viscosity of the glass phase is lower and it is easier to diffuse into the high-temperature glass liquid. The crystal phase in the brick loses its binding material and enters the glass liquid, forming stripes and stones.
Zirconium corundum bricks made in a reducing atmosphere will also produce bubbles in the glass. This is due to the strong reducing properties of low-valent oxides and other reducing substances (such as C) in the glass phase in the brick. When they interact with the glass, they take away the oxygen dissolved in the glass, making the soluble gas in the glass liquid difficult to dissolve and turning into bubbles. For example, SO3 dissolved in molten glass is reduced to SO2. The solubility of SO2 in the glass liquid is low, so it becomes bubbles and reduces the quality of the glass.
Nowadays, the oxidation method is used to make zirconium-chromium corundum bricks, which can improve its performance and prevent the above defects. Rongsheng Refractory Brick Manufacturer is a powerful manufacturer of production and sales of refractory bricks. Buy high-quality refractory bricks for glass kilns, such as fused zirconium corundum bricks, corundum bricks, corundum mullite bricks, etc. Please contact us for a free solution and quote.