Lightweight silica bricks are also called silica insulating bricks. The lightweight refractory bricks with a silica content of more than 91% and a bulk density of less than 1.2g/cm3. The refractoriness and softening temperature under load is not much different from ordinary silica bricks with the same composition. However, due to a large number of pores, the compressive strength, slag resistance, and corrosion resistance are not as good as ordinary silica bricks, but the thermal shock resistance is improved. RS refractory bricks company discovered the application of lightweight silica bricks based on years of production and sales experience and the characteristics of lightweight silica bricks. Contact RS refractory bricks factory for the affordable price of lightweight silica bricks.

Characteristics of Silica Insulation Bricks
Using finely divided silica as raw material, the critical particle size is usually not more than 1mm, and the particles smaller than 0.5mm are not less than 90%. Add flammable substances to the ingredients or use the gas generation method to form a porous structure, which is obtained by firing. Can also be made into non-fired products. It is mainly used in various parts of the kiln that require heat insulation or weight reduction without direct contact with the melt, without the action of corrosive gases, and without sudden temperature changes. It can be used at high temperatures and cannot be in contact with basic refractory materials. According to different materials, the operating temperature is 1200-1550℃.
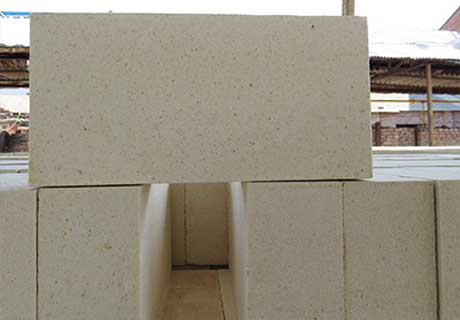
Application of Silica Insulation Bricks
Lightweight silica brick is a very special material, mainly used in the glass industry and steel industry. In most cases, lightweight silica bricks and dense silica bricks are used as part of the structural layer. Commonly used in the glass kiln industry, mainly the insulation of the kiln vault, thereby reducing heat loss and increasing the efficiency of the melting process. In the steelmaking industry, lightweight silica bricks are used for hot blast stove walls and domes.
- Silica Insulation Bricks are Used in the Glass Industry – Thermal Insulation of Furnace Vaults
During the glass melting process, very high temperatures are reached in the raised lower part of the dome. Depending on the type of glass, the temperature is around 1600°C. Lightweight layers are usually designed as two or more layers.
Lightweight silica bricks are primarily exposed to these temperature loads. It is expected that the single layers of the vault (structural layer and lightweight layer) have the same or similar expansion properties. Silica bricks with a bulk density of 1250kg·m-3 or 1000kg·m-3 can meet the requirements of the dense layer. The next layer uses silica bricks with a bulk density of 800kg·m-3 or 600kg·m-3.
Lightweight silica bricks can be freely stacked on the furnace arch or bonded with silica refractory mortar. There is no chemical load during the furnace service period (several years). Lightweight silica bricks are mainly used because the chemical and mineral composition of the working linings is similar to dense silica bricks.
- Lightweight Silica Bricks are Used in the Steel Industry – Hot Blast Stove
Hot blast stoves are often used for hot blast (called blast furnace blast), which communicates with the blast furnace’s air extractor. Depending on the shape and location of the hot blast stove, the temperature range is between 1000 and 1300 °C. The hot air is in the range of 2300~6500m3·min-1.
Lightweight silica bricks are used in blast furnace blasting parts and communicate with the blast furnace exhauster. The temperature range of lightweight silica bricks is between 1000 and 1300 °C. It can meet the whole cycle life of the hot blast stove. The bulk density of the lightweight silica bricks used is 1250kg·m-3 or 1050kg·m-3. Mainly due to their higher strength.
Lightweight silica bricks are also used in the coking chamber and the partition wall of the combustion chamber of the coke oven, the regenerator and the slag chamber of the steelmaking open hearth, the soaking furnace, the glass melting furnace, the firing kiln of refractory materials and ceramics, etc. There are also vaults and other load-bearing parts for kilns. It is also used for high-temperature load-bearing parts of hot blast stoves and acid open-hearth furnace tops.
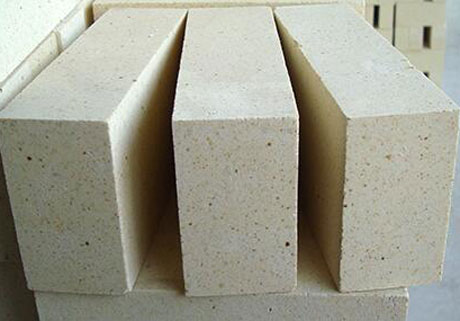
Advantages of Lightweight Insulation Bricks
The advantages of lightweight insulation bricks are high-temperature resistance, high bulk density, high strength, wear resistance, and acid and alkali corrosion resistance. It is widely used in high-temperature furnaces such as metallurgy, chemical industry, electronics, and glass. It has the advantages of reducing the weight of the kiln, thinning the kiln wall, changing the kiln structure, increasing the heating rate, reducing energy consumption, improving working conditions, and improving work efficiency. The heat storage loss of industrial furnace masonry and the heat dissipation loss of furnace body surface generally account for about 24-45% of fuel consumption. The use of lightweight insulation bricks with low thermal conductivity and small heat capacity as the structural material of the furnace body can save fuel consumption. At the same time, because the furnace can heat up and cool rapidly, it can not only improve the production efficiency of the equipment but also reduce the weight of the furnace body and simplify the structure of the furnace. Then improve the quality of insulation, reduce ambient temperature, improve labor conditions, and save energy and production costs.
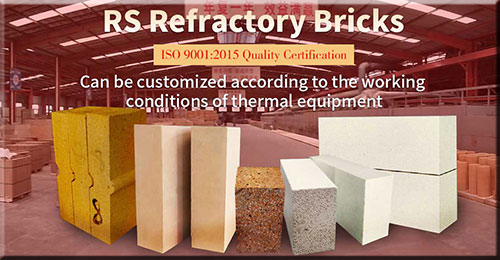
To buy low-density thermal insulation bricks, lightweight silica insulation bricks, lightweight insulation bricks, and thermal insulation bricks for tunnel kilns, please contact Rongsheng refractory bricks manufacturer rs refractory bricks company.