In modern blast furnace overhauls, ceramic cups are generally constructed of bricks or pouring bodies. After several years of operation, in order to improve the airflow distribution or reduce the fuel ratio, the ironworks will shut down the furnace for a short period of time to repair the lining and tuyere belt, and resume production without processing the ceramic cups. Effect of blast furnace hearth ceramic cup construction on operating quality. With this method of short-term repair without removing residual iron, common problems after starting the furnace include the following:
- (1) After the furnace hearth cools down, cracks appear in the pouring body or the gaps in the brick lining become larger. If left untreated, there will be a risk of iron infiltration after the furnace is opened.
- (2) During the solidification process of the dead iron layer at the furnace bottom, it separates from the surrounding refractory material and contains debris. Due to the thermal expansion in the initial stage of furnace opening, it is transmitted to the furnace shell, causing the furnace shell to crack.
- (3) The ramming layer between the carbon bricks and the cooling stave, and the filling layer between the cooling stave and the furnace shell, are somewhat loose, causing “gap insulation” and gas blow-by.
Ceramic cup construction is at the heart of the questions posed above. When shutting down the furnace for maintenance and handling the furnace slag, if the surface of the ceramic cup is covered with a uniform viscous slag layer, the risk of iron infiltration when the furnace is opened will be avoided, and the oven time will be appropriately extended. With the protection of the viscous layer, the stress of the furnace ceramic cup can be effectively distributed and the furnace opening efficiency can be improved.
New Hearth Casting Material Integrally Cast Thin-Walled Ceramic Cup
Currently, the main blast furnace repair solution is to pour corundum silicon carbide material with higher thermal conductivity based on the remaining effective carbon bricks. In this way, the remaining carbon bricks that have formed a stable state are used to improve the heat transfer efficiency. Under the same cooling intensity, a slag-iron viscous layer is easily formed on the surface of the ceramic cup, which protects the ceramic cup.
The overall pouring design of the furnace hearth means that the corrosion of the castable by molten iron and slag is a long-term process, and the chemical erosion is extremely small. Therefore, when designing a new hearth, it can be directly designed into a thin hearth structure (Figure a). Forming a more efficient heat transfer furnace (Figure b simulates the reasonable distribution of the 1150°C isotherm). Combined with corrosion-resistant corundum silicon carbide castables, “elephant foot erosion” will no longer occur in blast furnace hearths.
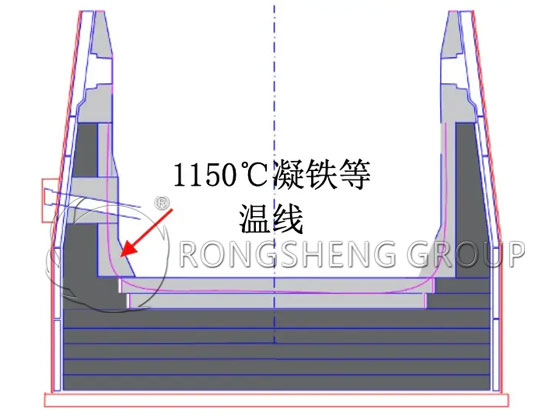
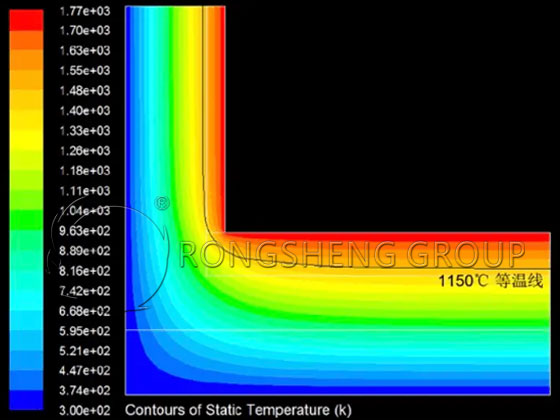
After comprehensively analyzing the above problems, a new hearth casting material is used to integrally cast thin-walled ceramic cups. The thermal conductivity of the pouring body can reach 6 W/(K·m), which is three times the thermal conductivity of traditional corundum-mullite ceramic cups. This more scientific temperature gradient distribution can more effectively form a slag-iron viscous layer and protect the working layer. The practice has proven that the sol-bonded corundum silicon carbide casting material has efficient resistance to slag iron erosion, resistance to molten iron dissolution, and reasonable thermal conductivity. Used in hearth ceramic cups, it can ensure the longevity of the hearth.
What is the Density of Blast Furnace Carbon Bricks?
What is the density of blast furnace carbon bricks? Carbon brick density is the volume density of carbon bricks, which refers to the mass per unit volume of carbon refractory bricks. The volume density index of carbon bricks is an important indicator of the density of carbon bricks. Carbon brick density is relatively easy to detect. The density of carbon bricks is used as a test to judge the degree of sintering of carbon bricks in production. The higher the density of the carbon brick, the better its resistance to the erosion of slag. Generally, the density of carbon bricks is expressed in g/cm3 or kg/m3.
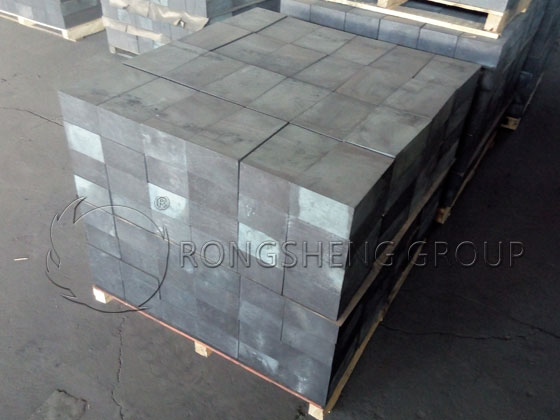
Blast furnace carbon bricks are divided into blast furnace semi-graphite carbon bricks, blast furnace microporous carbon bricks, and blast furnace carbon composite bricks according to the different parts of the blast furnace lining. Blast furnace carbon bricks made of different materials have different physical and chemical indicators and different volume densities.
- Blast furnace semi-graphite carbon bricks are generally used to build the blast furnace bottom. Its bulk density is 1.5g/cm3.
- Blast furnace microporous carbon bricks are generally used for blast furnace hearth wall masonry. Depending on the part used, the volume density is 1.65-1.7g/cm3.
- Blast furnace carbon composite bricks are generally used in the construction of blast furnace ceramic cups. According to different physical and chemical indicators, its volume density is 2.7-2.85g/cm3.
The density of blast furnace carbon bricks is one of the important reference indicators for customers to purchase carbon bricks. Carbon bricks for different uses have different physical and chemical indicators and different volume density requirements.
The factors that affect the volume density of blast furnace carbon bricks include the following two aspects. One is the particle size of the refractory raw materials of the blast furnace carbon bricks and the bulk density of the raw materials. On the other hand, is the control of the production process. Therefore, when producing blast furnace carbon bricks, it is necessary to strictly select the grade of raw materials and control the particles. During the production process, the pressure of the brick press to press the bricks is controlled, and the firing of the blast furnace carbon bricks is reasonably controlled.
When purchasing blast furnace carbon bricks, more physical and chemical indicators need to be provided, such as main component content, compressive strength, flexural strength, etc. Experienced refractory material practitioners can roughly judge whether the blast furnace carbon bricks can be used in industrial kilns with a long life based on the physical and chemical indicators and size requirements provided by the customer. Contact us to get free refractory lining solutions and quotations for blast furnace carbon bricks and refractory lining materials.