A rotary kiln waste incinerator is a heat treatment equipment for incinerating waste (including domestic waste and medical waste), which can fully guarantee the environmental protection requirements of stabilization, safety, reduction, and harmlessness of medical waste. At the same time, it is in line with the development trend of contemporary medical waste and domestic waste treatment. Contact RS Refractory Brick Manufacturers to obtain free samples and quotations of chrome corundum bricks for rotary kiln waste incinerators.
The internal temperature of the rotary kiln type waste incinerator is 1400℃~1600℃, and it can reach 1700℃ locally. The slag in the furnace in contact with the hot surface contains Na2O, K2O, C1, K2SO4, etc. Alkalinity 0.3~1.5. The rotary kiln rotation mode is positive and negative swing. The atmosphere in the furnace is constantly changing. In addition, the types of medical waste, water content, and acidity vary greatly. The refractory lining of the rotary kiln type waste incinerator is required to have strong resistance to slag erosion, permeability, high strength, erosion resistance, wear resistance, and thermal shock resistance. To accommodate the impact of mechanical stress and thermal stress.
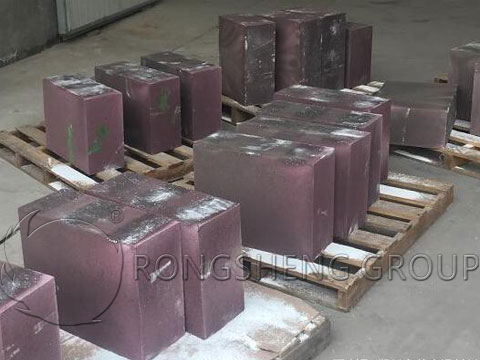
Chrome Corundum Brick for Rotary Kiln Type Waste Incinerator
At present, the refractory materials used in rotary waste incinerators include magnesia-chrome bricks, aluminum-chrome bricks, high-alumina bricks, silicon carbide bricks, etc. However, due to the uncertainty of the atmosphere in the furnace, the operating temperature, the calcium-silicon ratio in the slag, and the variability of the types of garbage. Even refractory bricks with better performance are difficult to achieve their expected results.
The refractory bricks used in the rotary kiln for incinerating medical waste and domestic waste must be able to be used in the furnace with severe slag erosion, severe thermal shock, and high operating temperature (1600 ℃). Chrome corundum material has the conditions of use, it is more suitable to make it into chrome corundum brick.
The composition of chrome corundum brick is 10%~30% Cr2O3, with particle size <0.1MM. 3%~6% ZrO2, the particle size is 0.5~4.0MM. 62%~87% AL2O3 (corundum), particle size is 0.2~0.4MM. Bricks are made by machine pressing and fired between 1450% and 1700%. The open porosity is between 9% and 18%, the elastic modulus is less than 3000MPa, and the temperature cycle stress value is greater than 30.
Chrome corundum brick has good corrosion resistance and is especially suitable for incinerating rotary garbage incinerators corroded by acid and alkali. This is used at temperatures up to 1700°C and its structural elasticity and corrosion resistance are still very good.
Refractory bricks for waste incinerators also need continuous improvement
- Bricks containing chromium oxide will continue to be used as linings of waste incinerators due to their excellent resistance to slag erosion. However, its high density and strength result in poor toughness of the material and therefore poor resistance to structural spalling. Methods of introducing microcracks into materials can balance the gap between material erosion resistance and spalling resistance.
- Most waste incinerators are equipped with a water-cooled structure. SIC castables are ideal masonry materials due to their high thermal conductivity. Its use in other parts of waste incinerators will also become an important direction for chrome-free refractories for waste incinerators.
- Chromium-free refractories for waste incinerators will continue to be the focus of research.