Corundum-mullite brick products use imported tabular corundum and high-purity fused corundum as the main raw materials. It adopts micro-powder addition technology and is fired at high temperatures in a shuttle kiln after mixing, shaping, and drying. During the production of corundum mullite bricks, a certain thickness of heat insulation layer material is designed and produced on the non-working surface according to the usage conditions.
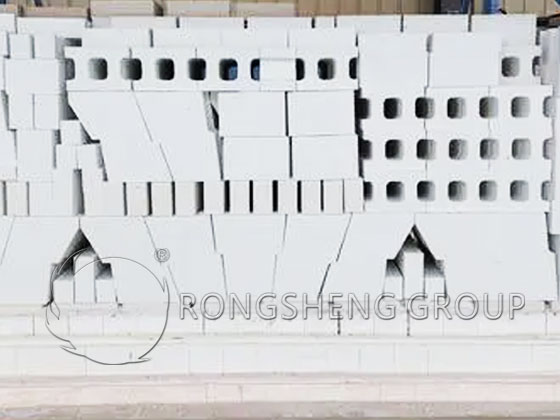
Corundum-mullite bricks use special production technology to combine two different materials into one whole. Under the premise of ensuring no fracture and keeping the thermal expansion rate close to the same, the corundum mullite bricks have the characteristics of high-temperature erosion resistance, high strength, and erosion resistance. It can effectively solve the problem that double-layer insulation materials cannot be used in the rotary kiln lining.
The Practicality of Corundum Mullite Bricks in Wear and Erosion Environment
Corundum-mullite bricks are refractory materials that have the ability to resist friction, impact, and grinding of hard substances. Therefore, the higher the wear resistance, the better the performance of the refractory material. We can analyze the practicability of corundum bricks in abrasion and erosion environments through wear resistance.
- Select appropriate refractory materials based on the structure, working characteristics, and working conditions of the furnace and analyze the causes of material damage. Accurately understand and grasp the temperature changes of various parts of the material, and carefully observe the material to prevent it from being subjected to various destructive effects.
- Be familiar with the chemical composition, physical, and working properties of materials in order to give full play to the characteristics of materials.
- Make the materials in each part of the furnace reasonably matched to avoid mutual damage between materials, and at the same time, take measures to ensure the overall service life.
- Solve resources and costs as much as possible while meeting the above basic principles. You can choose materials with low prices and transportation costs, and at the same time vigorously develop recycling to reduce costs.
The corundum usage rate is very low and it is difficult to meet the requirements. However, the overall strength and construction capabilities are poor and cannot meet the diverse environment of the industry. In the future, we will vigorously strengthen our own fire resistance, and use high quality and service first.
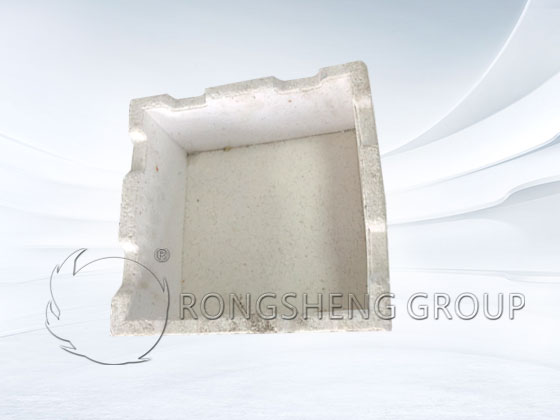
Corundum Mullite Brick Sagger
Corundum mullite bricks are widely used in high-sintering equipment such as zirconia ceramics, fluorescent materials, electronic ceramics, magnetic materials, ceramic powders, gasifiers in the petrochemical industry, and high-temperature kilns in the glass industry.
Among them, the corundum mullite brick sagger is used to load materials and sinter materials at high temperatures. The thermal shock stability is higher than that of 99 porcelain crucibles and can be used at high temperatures of 1700°C. Corundum mullite brick sagger is made of phosphorus, lithium, rare earth, and other powder-sintered materials. It has high refractoriness, good thermal shock stability, high-temperature resistance, good corrosion resistance, etc. Applicable to alumina ceramics and zirconia ceramics, fluorescent materials, powder metallurgy, electronic ceramics, magnetic materials, high-temperature sintering ceramic powders, etc.
Characteristics of Corundum Mullite Bricks
- Corundum-mullite bricks have the characteristics of high refractoriness and good thermal shock stability.
- High-temperature strength, corrosion resistance, and slag resistance.
- Features such as small expansion coefficient, low creep property, and low peeling. Corundum-mullite bricks are suitable for use in high-temperature kilns under various conditions.
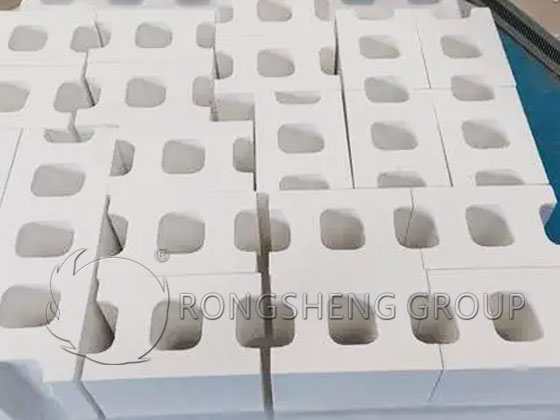
How Can Corundum Mullite Bricks Improve the Thermal Shock Stability of Corundum Bricks?
Thermal shock stability of corundum mullite bricks refers to their ability to resist cracking or shattering when subjected to hot and cold cycles at high temperatures. To improve the thermal shock stability of corundum bricks, you can start with the following aspects:
- Optimize material formula. Choose raw materials with high purity, low oxide content, and fine particle size. And carry out reasonable formula design to improve the density and earthquake resistance of the material.
- Increase the sintering temperature. Appropriately increasing the sintering temperature of corundum mullite bricks can increase the density and integrity of the crystal structure, thereby improving their thermal shock stability.
- Control sintering time. Excessive sintering time will cause the particles of corundum mullite bricks to grow too large, thus reducing their thermal shock stability. If the sintering time is too short, its density will be affected. Therefore, it is necessary to master the appropriate time during the sintering process.
- Add an appropriate amount of stabilizer. Stabilizers can form solid solutions in the crystal lattice of corundum-mullite bricks. Thereby enhancing the stability of its crystal lattice and improving thermal shock stability.
- Optimize processing technology. When processing corundum mullite bricks, the right temperature and pressure need to be used. Avoid excessive residual stress and micro-cracks, thereby improving its thermal shock stability.
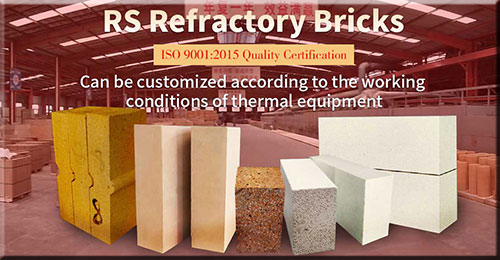
RS Corundum Mullite Brick Manufacturer
RS corundum mullite brick manufacturer is a powerful manufacturer and seller of refractory bricks. As a refractory material manufacturer, we provide refractory material services for high-temperature industrial furnaces. Our corundum mullite refractory brick products are of reliable quality. If you purchase our products, we provide after-sales service to ensure the long-life operation of your high-temperature industrial furnace. RS refractory brick factory has a high production capacity and fast delivery. Customer service is guaranteed. Contact us to get a free quote and samples.