Regarding the burning of the furnace wall of a company’s 27000KVA sealed calcium carbide furnace, especially the redness of the furnace wall above the furnace’s eye-opening is more serious. In severe cases, the furnace wall is “eaten”. This has led to a reduction in the start-up rate of calcium carbide furnace equipment. In view of the furnace wall burning failure, by analyzing the causes of furnace wall burning, solutions were proposed.
Overview of the 27000KVA Sealed Calcium Carbide Furnace Body
The furnace body consists of a furnace shell, furnace lining, base, furnace outlet, etc. The upper part of the furnace shell is an integral welded structure of a water-cooled steel plate (20G). The three discharge openings are evenly arranged along the circumference. The furnace shell bears the weight of the furnace lining and materials in the furnace as well as the thermal stress caused by the increase in temperature of the electric furnace. Calcium carbide furnace lining is mainly composed of high alumina bricks, self-baking carbon bricks, refractory castables, carbon paste, and other refractory materials. The furnace parameters are as follows. Furnace shell diameter: φ9000mm. Furnace inner diameter: φ8160mm. The electrode diameter is φ1250mm. Electrode center distance: φ3120mm. Furnace depth: 2800mm.
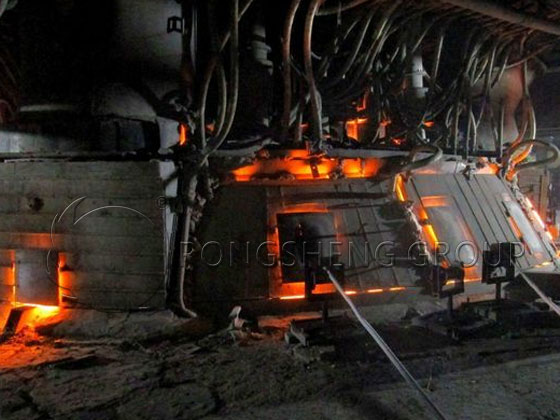
Causes of Burnt Damage to the Walls of Calcium Carbide Furnaces
① During the production of calcium carbide, the furnace lining around the furnace mouth is burned.
The outlet of the furnace is severely corroded by heat. The outlet is the closest place to the electrode and receives the most serious thermal corrosion. The outlet is damaged the fastest and the service life of the furnace lining is the weakest.
② The outlet has been corroded by oxidation, moisture, ferrosilicon, etc. for a long time.
There is also oxidation corrosion on the furnace wall around the outlet. When the pressure in the calcium carbide furnace is low in the later stages of the furnace, air will enter the lower part of the furnace outlet. The carbon bricks, high alumina bricks, and refractory castables at the outlet are oxidized by oxygen and carbon dioxide. Oxygen blowing and the use of cement balls for plugging the holes aggravate the oxidative erosion reaction.
③The outlet is subject to mechanical erosion.
The high-temperature calcium carbide flowing out when the furnace is discharged washes the discharge opening and expands the discharge opening. When the viscosity is high and the fluidity is poor and the discharge is not smooth, the artificial use of round steel with calcium carbide will cause the bottom of the outlet to be damaged by strong mechanical erosion and peel off.
④ Unreasonable current distribution causes burning damage to the furnace wall above the discharge eye of the calcium carbide furnace.
After the calcium carbide furnace is energized, the carbon electrode generates a strong current through the charge, ionizing the gas at the electrode tip. An arc area capable of high temperature is generated between one end of the electrode and the charge, which is called a molten pool. When the furnace entrance is shallow, the reaction molten pool of the calcium carbide furnace is too large, which will cause the furnace wall close to the electrode to be severely corroded by heat. In other words, this is the reason why the furnace wall appears red above the exit hole of the calcium carbide furnace or the furnace wall is burned through. After the furnace lining at the outlet is burned, it will cause collapse and melting holes in the furnace wall above the outlet.
⑤ The three outlet openings cannot be used evenly when discharging the oven, resulting in serious burn damage to the frequently used oven openings.
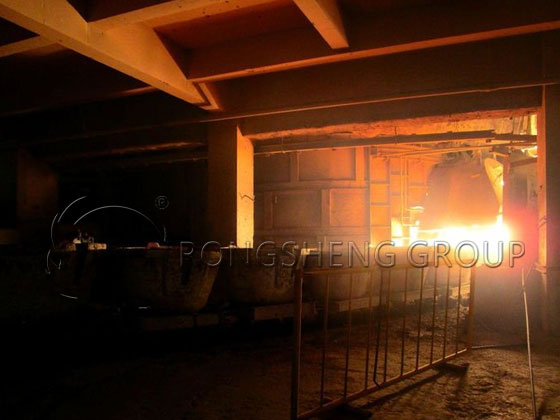
Take Repair Measures
① The depth of the electrode entering the furnace is controlled within the range of process requirements.
According to the existing furnace inner diameter is 8160mm. It is estimated that the depth of the carbide furnace electrode entering the furnace should be controlled at ≥600mm, so that the current distribution tends to be reasonable and the thermal corrosion of the furnace wall is reduced.
② Strengthen the daily maintenance of the outlet openings and use the three outlet openings in a balanced manner.
Always burn the furnace eye frequently. When turning on the furnace, try to burn the furnace eye in a regular manner, with a large outer opening and a small inner opening. After the furnace is finished, clean the furnace eye and the upper part of the furnace mouth.
Maintain a proper depth of the electrode into the furnace and increase the furnace bottom temperature. Improving the fluidity of calcium carbide shortens the discharge time, reduces the probability of mechanical erosion and air oxidation at the discharge port, and reduces the frequency of oxygen-blowing operations. Control the proportion of loach and its moisture to reduce erosion of the outlet. Use high-volatile electrode paste to repair the outlet in time, and maintain the outlet cooling equipment in a timely manner. Make sure it is in good condition and use the three outlet carbide stones evenly.
③ How to deal with the furnace wall turning red or the furnace wall being burned through.
Melting holes appear on the furnace wall, and the furnace wall becomes red. The treatment method is to weld the water box on the furnace shell and cool it, then dig out the furnace material, fill it with carbon ramming material, tamp it, and then cover the furnace material. The treatment method for burning through the furnace wall is to deal with it from the outside of the furnace wall, cut the red furnace shell, and remove the burned furnace wall. Clear the surrounding furnace materials and use aluminum silicate needle-punched felt for heat insulation. Then fill and level the floor with carbon ramming material. Use high-alumina bricks to build partition walls, repair the furnace outlet equipment, and weld the furnace shell. The distance between it and the high-alumina bricks should be greater than 400mm. Pour refractory material between the furnace shell and the high-alumina bricks to repair, and vibrate and compact. The curing time is 72 hours.
Burning damage to the furnace wall of the calcium carbide furnace is mainly caused by unreasonable current distribution, which causes heat to accumulate on the furnace wall and then causes thermal corrosion damage. When the furnace entrance is shallow, the reaction molten pool of the calcium carbide furnace is too large, causing the furnace wall closer to the electrode to suffer from thermal corrosion. According to the specific furnace depth, furnace inner diameter, electrode diameter, electrode center distance and other parameters, the control depth of the carbide furnace electrode entering the furnace can be calculated. By controlling the depth of the electrode into the furnace, controlling the current distribution tends to reasonably reduce the thermal corrosion of the furnace wall.
[Related News] Bayi Iron and Steel applied for a patent for the method of accurately selecting the opening position of the Ouye furnace hearth to improve the cooling intensity of the cooling stave for the carbon bricks.
According to news from the financial industry on April 3, 2024, according to an announcement from the State Intellectual Property Office, Xinjiang Bayi Iron and Steel Co., Ltd. applied for a project called “A method for accurately selecting the opening position of the Ouye furnace hearth.” Publication number CN117804231A, the application date is December 2023.
The patent abstract shows that the invention discloses a method for accurately selecting the opening position of the Ouye furnace hearth. By determining the gaps between the cooling staves and the gaps between the furnace carbon bricks, find out the position of the iron filings filler between the two cooling staves, and use a magnetic drill to make holes in the furnace shell. Use a percussion drill to drill through the iron filling layer to reach the carbon ramming layer. Then use a negative pressure ejector to suck out the debris blocked in the hole to make the grouting pipeline unblocked. Special carbonaceous slurry with high thermal conductivity is used to press into the furnace hearth and furnace bottom to simultaneously grout the hot and cold surfaces of the cooling stave to fill the air gaps in the carbon ramming layer on the hot surface of the cooling stave. Improve the cooling intensity of the carbon bricks by the cooling stave, and monitor the residual thickness of the hearth carbon bricks by adding a thermocouple.
To purchase high-quality refractory materials for calcium carbide furnaces and refractory materials for smelting furnaces, please choose Rongsheng Refractory Bricks Manufacturer. Rongsheng manufacturer, with rich production and sales experience, provides a guarantee for the long life and efficient operation of high-temperature industrial furnace linings. Contact us for a free solution and quote.