The characteristics of physical and chemical indicators of magnesia bricks with refractoriness above 2000 °C.
The refractoriness of magnesia bricks is above 2000°C, and the load softening temperature varies greatly with the melting point of the cement phase and the amount of liquid phase produced at high temperatures. The load-softening temperature of general magnesia bricks is between 1520 and 1600 ℃, while high-purity magnesia bricks can reach 1800 ℃. The load-softening start temperature of magnesia bricks is not much different from the collapse temperature. The linear expansion rate of magnesia bricks at 1000~1600℃ is generally 1.0%~2.0%, and it is approximately linear. In refractory products, the thermal conductivity of magnesia bricks is second only to carbon-containing bricks, and it decreases with the increase in temperature. Under the condition of 1100 ℃ and water cooling, the thermal shock resistance of magnesia bricks is only 1-2 times. Magnesia bricks can resist the erosion of alkaline slags such as iron oxide and calcium oxide, but they are not resistant to the erosion of acidic slags such as silicon oxide. Therefore, it cannot be in direct contact with silica bricks when used, and should generally be separated by neutral bricks. The conductivity of magnesia bricks at room temperature is very low, but it cannot be ignored at high temperatures, such as 1500 °C. It should be paid attention to when it is used on the bottom of an electric furnace, especially when it is wet.
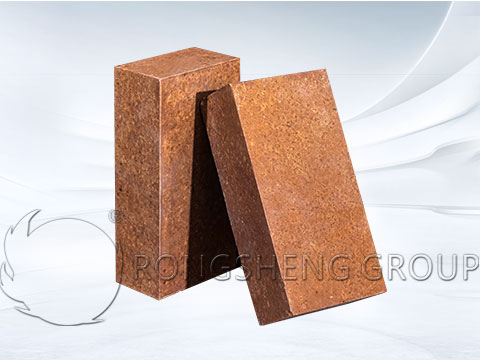
The microstructure of magnesia bricks is actually a combination of magnesia microstructures. The microstructure of magnesia bricks made of a kind of magnesia is the simplest, but the matrix part is relatively loose and has more pores. Magnesia bricks made of different grades of magnesia have obvious differences in microstructure. Magnesia bricks made of magnesia with high impurity content have many silicate phases, MgO crystals are round, and the direct bonding rate is low. The impurity content of the raw materials is low, and the magnesia brick fired at ultra-high temperature is used, the silicate is reduced, and the direct bonding rate is high. In magnesia bricks with more than 98% MgO content, the MgO crystals are euhedral and semi-euhedral. True direct intergranular bonding can only be maximized in materials free of silicates and intergranular pores.
The performance of magnesia bricks varies greatly due to the use of raw materials, production equipment, and technological measures.
Magnesia bricks have good high-temperature performance and strong resistance to metallurgical slag. It is widely used in the lining of steelmaking furnaces in the iron and steel industry, ferroalloy furnaces, mixed iron furnaces, and non-ferrous industrial furnaces for copper, lead, tin, and zinc furnace linings for building materials and lime calcining kilns. Glass industrial regenerator lattices and civil heat exchangers. High-temperature calcining kilns in the refractory industry, such as high-temperature shaft kilns for calcining magnesia, high-temperature tunnel kilns for firing alkaline refractory bricks, etc.
Magnesia brick knowledge question and answer
What is the refractoriness of magnesia bricks? Are magnesia bricks acidic or alkaline? Magnesia bricks are made by crushing magnesia raw materials into granules and powders. After batching according to a certain ratio, binders and kneading into mud. Then it is made into fired magnesia bricks through molding, drying, firing, and other processes. Magnesia bricks can be used in heating furnaces and soaking furnaces. Magnesia bricks are used to pave the surface layer of the furnace bottom and the lower part of the soaking furnace wall. Because it can resist the erosion of the iron oxide scale.
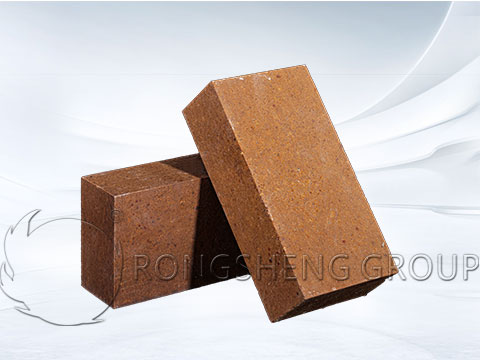
How much is the fire resistance of magnesia bricks
The refractoriness of magnesia bricks is over 2000°C, which belongs to special refractory materials, and the load softening temperature is generally between 1520 and 1600°C. The refractoriness of magnesia bricks with higher purity can reach 1800°C. The thermal shock resistance of magnesia bricks is poor, and improving the purity of magnesia bricks can properly improve the thermal shock resistance. The ability of magnesia bricks to resist acid slag is very poor, and they cannot be in direct contact with silica bricks during use. Generally, neutral bricks should be used to separate them.
Are magnesia bricks acidic or alkaline?
The main crystal phase of magnesia bricks is periclase, which belongs to basic refractory bricks. It has strong resistance to alkaline slag, but it cannot resist the erosion of acid slag. At a high temperature of 1600 ° C, it can react with silica bricks, clay bricks, and even high alumina bricks.
If you need to use magnesia bricks or magnesia-chrome bricks for your high-temperature industrial kiln equipment, please contact us, a manufacturer of RS refractory bricks. We can provide pre-sale guidance and sample service. Rongsheng Refractories specializes in the production of refractory bricks and castables, source manufacturers, and primary sources.
The difference between high alumina brick and magnesia brick
High-alumina bricks are aluminum-silicon series products, and magnesia bricks are magnesia series products. High alumina bricks can resist weak alkali and weak acid atmospheres and are neutral products. Magnesia bricks are resistant to strong alkali corrosion and cannot be used in an acidic atmosphere. They belong to the alkaline series of products.
High alumina bricks and magnesia bricks are two kinds of refractory products with different materials and properties. Magnesia bricks have a density above 3.0 and a melting point of 2850°C, and high-alumina bricks have a density above 2.3 and a melting point of 1500 ℃.
The raw material of magnesia bricks is magnesia particles from less than 5 mm to fine powder, which are crushed, shaped, and sintered at a high temperature of 1600 °C. The raw material of high alumina bricks is bauxite particles and fine powder which are crushed, shaped, and sintered at a high temperature of 1450°C.
The refractoriness of magnesia bricks is above 2000°C, and the load is soft at 1800°C. However, magnesia bricks have high thermal conductivity and poor thermal shock resistance. High-temperature resistance. Magnesia bricks have poor corrosion resistance to acid slag and cannot direct contact with acid products. If it is in the kiln lined with acid, it must be separated by high alumina bricks before use. Moreover, the hydration resistance of magnesia bricks is poor, and it is easy to grow white hair when it encounters water, It also produces cracks and reduces its strength. Magnesia bricks must be protected from moisture, rain, and snow during storage and transportation.
The refractoriness of high alumina bricks is above 1700°C. The softening temperature under load is 1520°C, and the maximum is not more than 1600°C. The load softening temperature of high alumina bricks is also very different according to different raw material grades. The load softening temperature of the third-grade high alumina brick is still around 1410°C. Although high alumina bricks are neutral bricks, they have good thermal shock stability, are not afraid of hydration, and can be used in weak alkali and weak acid atmospheres.
Therefore, at different temperatures of different kiln linings, the selection of magnesia bricks or high alumina bricks should be selected according to the degree of erosion and atmosphere. In an alkaline atmosphere, magnesia bricks must be used. The use temperature is below 1400 ℃, and high alumina bricks can be used in weak alkali or weak acid atmospheres.
The difference between high-alumina bricks and magnesia bricks is that they have different materials, different operating temperatures, different corrosion-resistant atmospheres, and different thermal shock effects. Another difference is the market price, the price of high-alumina bricks is low, and the price of magnesia bricks is high.
RS refractory brick manufacturers
RS Refractory Brick Manufacturer is a manufacturer of refractory bricks with rich production and sales experience. Our refractory products include various types of refractory bricks for high-temperature industrial furnaces. Especially all kinds of insulation bricks, low body density (<0.4g/cm3), low iron. Various precast refractory shapes are suitable for various high-temperature industrial furnaces. Contact us for free refractory lining solutions, samples, and quotes.