A non-ferrous metal production enterprise, after several minor repairs to the copper smelting converter, measured and counted the loss of refractory bricks in the converter from the wind eye to the upper furnace mouth and furnace mouth area. To sum up, the loss of Magnesia Chrome Bricks for Copper Smelting Converter is as follows. It can be seen from the data in the table that the life of the air eye brick and the furnace mouth brick determines the furnace life of the converter.
Items | Wind eye brick | Square brick (9th layer) | Wedge brick 1 (10th-16th layer) | Wedge brick 2 (17th-30th layer) | Lock brick for furnace mouth | Bricks for furnace mouth |
Original brick length / mm | 520 | 520 | 460 | 380 | 460 | 150 |
Loss / mm | 280 ~ 520 | 220 ~ 340 | 180 ~ 300 | 120 ~ 270 | 180 ~ 300 | Easy to drop bricks and fall off |
Improve and Control Measures
1. Improve the material content of magnesia chrome brick in the wind eye area
Magnesia Chrome Bricks for Copper Smelting Converter in the wind eye area are required to have strong properties such as high-temperature resistance, erosion resistance, chemical corrosion resistance, and impact vibration resistance. Therefore, the wind-eye bricks and triangle bricks in the wind-eye area were changed from the originally designed fused 20 magnesia chrome bricks (DMGe-20) to fused 26 magnesia chrome bricks (DMGe-26). The physical and chemical indicators are compared as follows.
Items | W(MgO)/% | W(Cr2O3)/% | W(SiO2)/% | Apparent porosity / % | Cold Crushing Strength / MPa | Load softening temperature / ℃
(0.2MPa, T0.6) |
DMGe-20 | 58 | 20 | 2.0 | 17 | 40(45) | 1700 |
DMGe-26 | 50 | 26 | 1.5 | 15 | 40(45) | 1700 |
The content of chromium oxide (Cr2O3) in the magnesia chrome bricks increases, which improves the anti-scouring performance of the magnesia chrome brick, and slows down the washing speed of the Magnesia Chrome Bricks for Copper Smelting Converter during use. At the same time, the porosity of DMGe-26 magnesia-chromium brick is significantly reduced, shortening the depth of slag erosion and metal penetration. The metamorphic layer at the hot end of the magnesium-chromium brick is also shortened, and the length of the metamorphic layer is shortened by about 10mm. The spalling length of the kind of refractory brick is reduced, and the wear rate of the wind eye brick is slowed down.
2. Strictly check the quality of maintenance
2.1 Mechanical aspects
(1) When repairing the wind eye seat and tee seat, polish the surface of the seat to ensure the flatness of the seat surface. When installing, use anti-loosening bolts and change the ordinary asbestos pad to aluminum-clad asbestos pad to ensure that there is no air leakage gap at the wind eye seat and tee seat.
(2) Make a wind eye tube adjustment model. Use the template to select two wind eye tubes as the calibration reference. After the correction of the center distance of the wind eye tube, it is necessary to meet the wind eye brick building requirements. Weld the wind eye tube and wind eye tube firmly.
(3) After the eye tube is installed in place, plug the eye tube nozzle with a plug. Start the GM fan to supply air to the converter, increase the air pressure to the air pressure during normal production of the converter, about 0.1MPa. Check the air leakage of the connection points of the bellows and the wind eye, and find the air leakage point and deal with it in time. To avoid insufficient air intake caused by air leakage, causing the inner tube of the wind eye and the furnace brick in the wind eye area to be washed too fast.
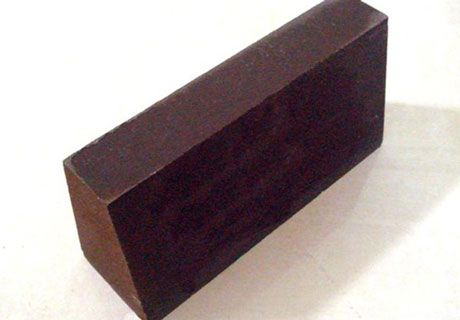
2.2 The kiln masonry aspect
(1) Wind-eye bricks, built from the middle to both ends. After masonry, polish the front and back of the wind-eye brick to avoid triangle joints in local locations.
(2) The bricks from the wind-eye bricks to the upper furnace mouth shall be returned to the masonry as required. Reduce the height difference between the bricklayers in the transition section of the retreat, and slow down the loss rate of the furnace bricks in the transition section.
(3) The mortar in the brick joint is full and uniform, consistent inside and outside. The joint between the new and old bricks is less than 3mm. The width of the processed brick is not less than 1/2 of its width, and the thickness is not less than 2/3 of its thickness.
(4) When the upper and lower furnace mouths are built, steel plates are welded on the furnace mouths to lock the bricks. To avoid the whole falling off the furnace mouth brick when cleaning the furnace mouth in production.
3. Standardize oven operation
Formulate oven specifications for minor repairs of converters. In the oven, firewood and oil gun are used in stages. Strictly control the heating according to the heating curve to ensure that the deviation of the oven temperature from the theoretical heating curve does not exceed 50°C, and ensure that the thermal expansion of the refractory material meets the material requirements. Avoid damage to refractory bricks caused by large fluctuations in oven temperature.
4. Optimize production operations
(1) Formulate the standard for adding cold materials to prevent the furnace temperature from being too high. Control the grade of matte copper stably, formulate the quantity of matte copper in a single furnace, and avoid large fluctuations in the quantity of matte copper. And strictly control the output of a single furnace.
(2) During the slag making process, the alkalinity of the slag is appropriately increased. The magnetic iron formed in the furnace adheres to the furnace wall, forming “slag hanging” in the furnace to protect the furnace bricks.
(3) In converter production, oxygen must be turned off before the shaker. In order to slow down the oxidation loss of oxygen-enriched air to the wind eye tube.
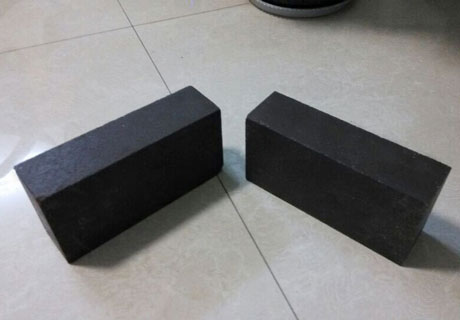
5. Conclusion
By implementing the above measures, the Copper Smelting Converter furnace life after minor repairs of the converter was increased from 90 to 140 furnaces. Although the converter furnace life has improved, it still has a considerable gap with other smelters. This also needs to reform the converter masonry structure, and strictly control the quality of the repair during the converter overhaul, to further optimize the converter production operations. Strive to increase the life of the converter minor repair furnace to 200 furnaces.
Rongsheng refractory brick manufacturer
Rongsheng refractory brick manufacturer has more than ten years of production and sales experience. Rongsheng’s refractory bricks products have been sold to more than 60 countries and regions around the world. Our refractory products are used in the following countries, such as India, Pakistan, Kuwait, South Africa, Malaysia, Vietnam, Netherlands, Philippines, Singapore, Egypt, Russia, etc. If you need to buy Magnesia Chrome Bricks for Copper Smelting Converter. Please leave your specific needs on this page form below and we will get in touch with you shortly.