What are the requirements for the use of Refractory Materials for Glass Furnace Melting Pool? The maximum temperature of the glass furnace melting pool is 1570~1610℃. The safety limit usually depends on the specific glass composition and the softening point of the silica brick, which begins to soften and drip at 1620°C. The bricks above the glass liquid generally use silica bricks rather than other materials that are more resistant to high temperatures. The reason is that, in addition to its high-temperature strength, silica brick’s ablation is also compatible with glass. Other refractory materials are prone to producing infusible stones and other inclusions.
Under the parapet and glass surface, most refractory materials are used that are denser than glass and very dense. Its ability to resist the erosion of glass liquid is far better than the refractory materials used in the past. All refractory materials below the glass liquid level of the melting pool must be forced to cool outside due to their short life, especially at the glass liquid level line where the corrosion rate is greatest. As the furnace ages, when other dangerous parts expand, cooling air must also be added to these parts, and the air volume must be gradually increased.
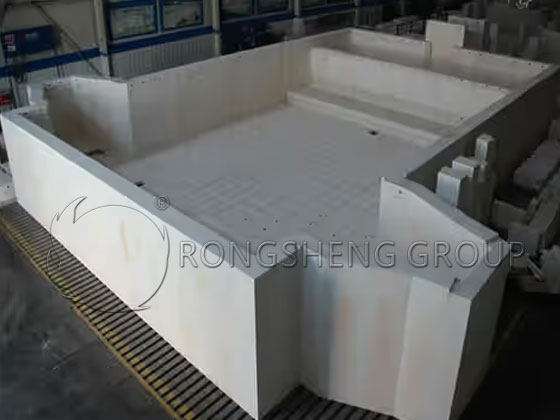
Any surface of a refractory brick in contact with hot glass liquid is the source of defects. Therefore, the trick in furnace design is to avoid covering a piece of refractory material as much as possible, and always have one surface exposed to the air to allow the heat to escape. For example, the pavement bricks at the bottom of the kiln must not float to prevent glass from entering under the bricks. The same is true for the silica bricks covered with insulation materials on the kiln wall mentioned above.
The most severely corroded refractory material is in the area of the first two pairs of flame outlets of the floating pile, where the grid is also most likely to be clogged. Clarifiers are the areas least exposed to erosion, and this area is usually unfired.
The bridge wall serves to separate two different temperature zones and also serves as a skimmer. The glass liquid flows out through the liquid hole.
The flow holes play a big role in cooling. It reduces the melting temperature of molten glass from 1540~1590℃ to about 1260~1310℃ in the clarifier. The feed channel is a temperature-controlled channel connected to the clarified discharge hole. Its function is to reduce the temperature of the glass liquid to about 1000°C to meet the needs of gob forming.
Common Refractory Materials in Glass Furnaces
Glass production is a high-temperature operation, and molten glass can corrode the refractory materials of the kiln tank. Refractory materials are affected by high temperatures, flames, and flying materials. Once corroded and damaged, the life of the furnace will be affected. If the glass liquid is contaminated, it will seriously affect the quality of the glass. Therefore, there should be strict requirements for the refractory materials used in glass kilns.
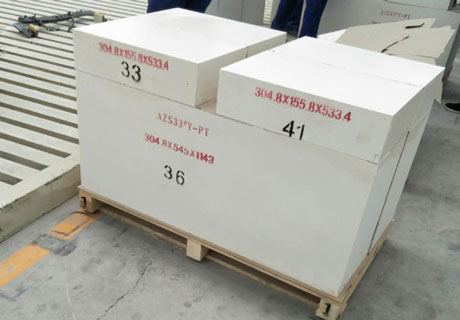
Commonly used refractory materials in glass melting furnaces are mainly divided into four categories: fused cast refractory materials, sintered refractory materials, unshaped refractory materials and insulating refractory materials.
- The cast refractory material has excellent resistance to the erosion of glass liquid and alkali steam erosion, and is the furnace building material for key parts of the furnace. Cast refractory materials are mainly made by melting the raw materials in an electric furnace, casting them into shape, and then annealing and mechanical processing. Its microstructure is more uniform than ordinary refractory materials.
- Sintered refractory materials are important supporting refractory materials widely used in furnaces. Commonly used varieties include silica bricks, alkaline bricks, and zircon bricks. Zirconium mullite bricks, mullite bricks. Sillimanite bricks, high alumina bricks, clay bricks, etc.
- The amount of unshaped refractory materials currently only accounts for 3% to 4% of the amount of refractory materials in the furnace, but it is very important to the age of the furnace. Generally, unshaped refractory materials should be made of the same material as shaped materials. Therefore, the commonly used varieties are equivalent in composition to their corresponding stereotyped refractory materials.
- Insulating refractory materials require low density, low thermal conductivity and good thermal insulation effect. At the same time, it has high refractory resistance and mechanical strength, and does not react with the refractory materials in contact. Commonly used insulating refractory materials include lightweight insulating bricks, insulating panels, insulating (lightweight) castables, insulating coatings and refractory fibers.
Small Furnace Tongue and Refractory Bricks for Glass Kiln
At present, refractory bricks for small furnace tongues are mainly fused AZS bricks. Fused bricks have good strength, high-temperature resistance and corrosion resistance, but their thermal shock resistance is poor and prone to cracks. This is due to the fact that the zirconia in AZS bricks undergoes phase transformation and shrinks at around 1200°C. In addition, its structure is dense and has little buffering.
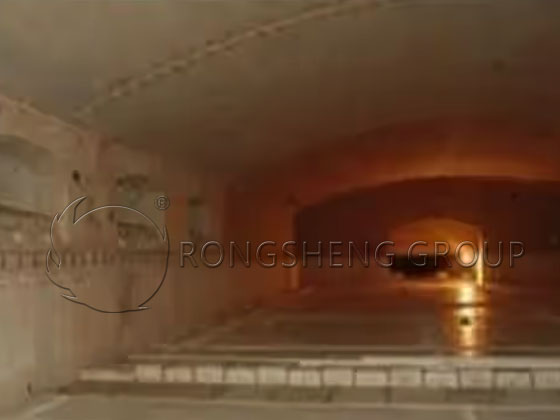
Due to the alternation of hot and cold between gas, combustion air and exhaust gas, the temperature of the tongue fluctuates rapidly between 1000 and 1600°C. This causes the AZS tongue to crack and peel to varying degrees. In addition, fused bricks are dense and require a strong steel structure for weight support, otherwise they are prone to collapse.
In addition, small stove tongues are also made of sintered mullite bricks, corundum, ordinary silica bricks and other materials. Although the thermal shock resistance has been improved, the erosion resistance and erosion resistance are not ideal. In the operation of many actual kilns, corrosion, peeling, etc. of the tongue often occur. On the one hand, it is the erosion of high-temperature airflow, and on the other hand, it is the erosion of flying dust. Especially the erosion of alkaline substances in the fly material will cause the following reactions:
- 1.NaOH corrosion of sillimanite, clay bricks, mullite and AZS:
AxSx + NaOH → Nepheline + Al2O3 (ΔV=6–36%)
- 2.NaOH corrosion of alumina corundum:
Al2O3 (α-alumina) + NaOH → β-alumina (ΔV=28%)
- 3.NaO erosion of ordinary silica bricks:
CaO-SiO2 (binding phase in silica bricks) + NaOH → Na2O-CaO-SiO2-phase glass phase
After the above-mentioned erosion occurs, due to the formation of nepheline and glass at high temperatures, volume deformation and high-temperature softening occur, which also causes various problems in the tongue. Therefore, the selection of materials for the small furnace tongue and grille requires refractory bricks that meet production conditions and take into account economic and practicality.