Glass melting furnace is the important thermal equipment in a glass factory. The cost of a melting furnace often accounts for half of the fixed asset investment of the entire glass production line. Since the advent of fused AZS bricks, almost all kiln wall bricks have been selected. In recent years, the shortage of raw materials, fuels, oil, electricity, etc. has become increasingly globalized, causing the price of fused AZS bricks to rise sharply all the way, and the share of refractory bricks materials in the entire furnace of fused AZS bricks has almost exceeded 50%. In addition, the life of fused bricks determines the length of the entire furnace operating cycle. It can be seen that how to use Fused AZS Wall Tiles and prolong the service life of bricks is particularly important.
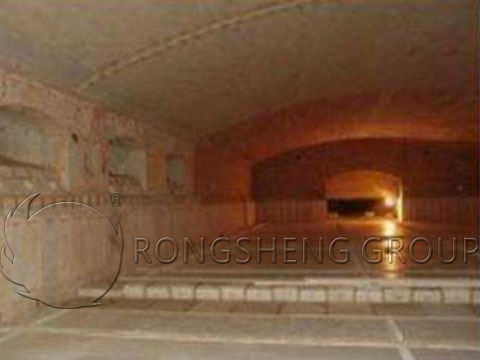
Methods to Slow Down the Erosion of Fused AZS Wall Tiles
How to slow down the corrosion rate of pool wall tiles, that is, how to enhance the corrosion resistance of fused bricks, is the key to extending the life of pool wall tiles. As we all know, reducing the use temperature of pool wall bricks is one of the main measures to extend the service life of bricks. In addition, due to different parts, different periods, and different conditions of pool wall tiles, different cooling methods must be adopted to achieve the expected cooling effect.
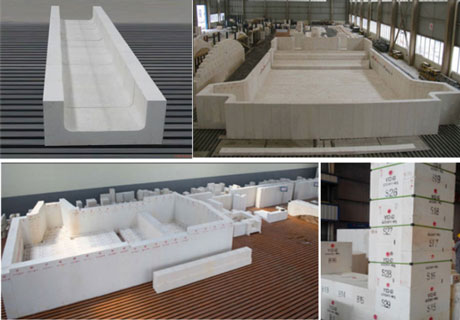
Reasonable forced air cooling method (wide-range system cooling method)
The uppermost end of the pool wall, that is, the upper part is 270mm, and the outer surface is the heat preservation part. Generally, because the flame is heated on the surface of the molten glass, the temperature of the upper layer of the molten glass is much higher than that of the lower layer. In addition, a large number of bubbles generated by the formation of silicate and the clarification of the molten glass, the large thermal convection inside the molten glass, etc. are all violent at the upper part, and the upper part of the pool wall is the part where the erosion rate is faster. In view of this situation, a reasonable choice of cooling fans and cooling ducts that are easy to regulate and control must be selected so that all parts can supply the necessary air volume. This cooling air should be installed and started when the kiln temperature is 250-300℃, and the air supply volume should be gradually increased as the temperature rises. It should be noted that the cooling should be carried out slowly at the beginning, and then gradually increase and decrease to avoid damage to the bricks due to the thermal stress generated by the temperature gradient.
Single point, centralized, forced air cooling
According to the current quality of domestically produced Fused AZS Wall Tiles and the manufacturer’s user experience, AZS bricks generally have a life span of 3 to 5 years. After the kiln has been in operation for 2 years, that is, in the middle and late stages of the kiln operation, due to individual differences in brick materials, such as the presence of melting holes in the brick materials, large gaps during the baking of the kiln after masonry or not properly handled, these parts will be affected. The phenomenon of oozing of glass water began. In view of this situation, single-point, centralized, and forced air cooling can be used to solve the problem.
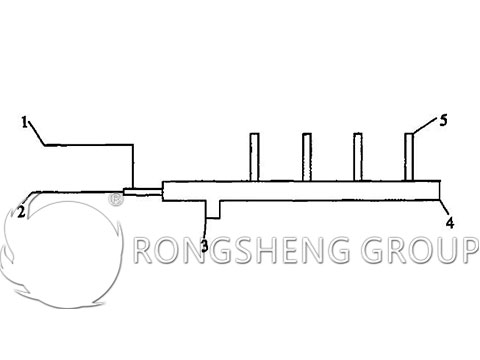
Wind-mixed water mist cooling method
Some special parts of the melting pool, such as the liquid hole, are not only the fastest eroded but also difficult to repair. Although settlement, tilting, and other methods are adopted in the design to improve its use environment. However, due to strong mechanical erosion and gas drilling erosion, the furnace was only used for 2.5 years before cold repair, and its cover bricks were already destroyed. Although forced air cooling has been adopted at the beginning of the operation, the expected effect is still not achieved. In this cold repair process, the liquid flow hole is semi-insulated, that is, the surface layer of the Fused AZS Wall Tiles are surrounded by high alumina bricks and then fastened with a steel structure. After the cold repair, the air-mixed-water mist cooling method is adopted decisively when starting operation.
This method is simple to manufacture, stable in control, and remarkable in a cooling effect. It avoids damage to bricks caused by improper direct water cooling. This is also the main reason why most manufacturers do not easily use water cooling. The same fluid tunnel has been running for 4 years after cold repair.
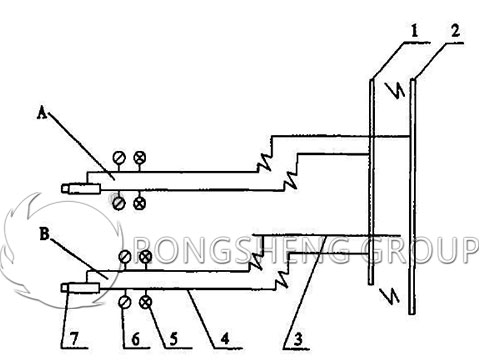
Bath cooling method
This method is mainly suitable for the middle and upper part of the pool wall brick in the later stage of the furnace operation.
Since the middle and upper part of the pool wall has different degrees of heat preservation, and the outer surface is fastened with steel plates, the erosion rate of the glass liquid is relatively weak, so there will be no problems in the early stage, and no measures need to be taken. In the third year after the cold repair of the furnace, the glass liquid gradually appeared in the middle and upper part of the pool wall. These leaks have a common feature, almost all leaks from the upper end of the pool wall insulation brick. Obviously, the leakage is through the channel formed between the pool wall fused brick and the insulation layer and flows from the outside. This phenomenon shows that the fused bricks in this part have been severely corroded. In view of the fact that there is an insulation layer on the outside of this part, forced air cooling is of no avail. The removal of the helper bricks requires a lot of work and is not safe. It is directly water-cooled and difficult to control. After the comparison, take the water bath cooling method to make these parts run safely to the end.
To Sum Up
In view of the different operating periods of the glass melting furnace, especially after minor cold repairs, different cooling and other maintenance measures have been taken for different parts of the Fused AZS Wall Tiles, which significantly prolongs the service life of the glass melting furnace. Obviously, this also brings huge economic benefits to the enterprise.