The burner brick is a component used in refractory installations, usually installed on the burner wall of the furnace. Mainly used in the gas combustion process, by heating the fuel in the burner brick to the ignition temperature, stabilizing the combustion process, and controlling the shape of the flame to meet the requirements of specific heating processes.
The Function of Gas Burner Brick
The function of gas burner brick has two aspects. On the one hand, it can organize the combustion process of fuel and ensure that the fuel is completely burned in the burner brick. On the other hand, when the combustion process stops, the burner brick can recover the flue gas and avoid the leakage of the flue gas.
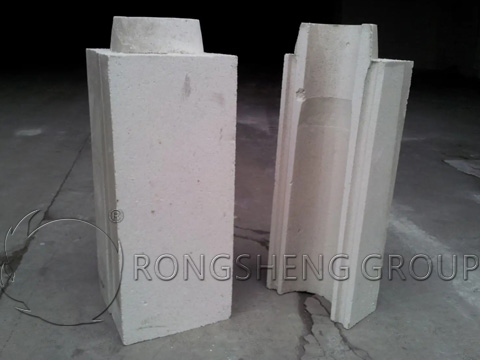
In addition to the above functions, burner bricks also have other important functions. First, it heats the fuel to ignition temperature, making it easy to ignite and burn quickly. Secondly, during the fuel combustion process, the burner brick can maintain a certain high temperature to ensure the stability of the combustion process and prevent pulsation or combustion interruption to meet the requirements of the heating process. In addition, burner bricks help further mix fuel and air to improve combustion efficiency.
Various types of Burner Bricks
Burner bricks can be divided into various types depending on the material used. Including chrome corundum burner bricks, corundum mullite burner bricks, high alumina mullite burner bricks, clay burner bricks, and silicon carbide burner bricks. These burner bricks of different materials have different characteristics and application ranges, and suitable materials can be selected according to specific needs.
Three Types of Burner Bricks and Their Production Processes
At present, among the many kilns, those that use gas heating, such as natural gas or coal gas, are used for heating. Kilns that form gas combustion and generate heat sources must be equipped with burners and burner bricks. The burner brick has also become an important part of the gas-heating furnace. The main function of the burner brick is to fully contact and mix the gas and combustion air in the burner brick area, and then burn them with the help of the high heat of the burner brick.
The entire production process of burner bricks starts with drawings. Kiln manufacturers can accurately design which category of burner bricks they need to use based on the size of the furnace, combustion power, gas consumption, and other data. Generally, burner bricks are divided into three types according to the shape of the flame: long flame, flat flame, and short flame. The long flame burner has a relatively long flame. This type of burner is mostly used for combustion in rotary kilns and roller-drying kilns. The main feature of the flat flame burner is that the burner outlet adopts a trumpet-shaped burner brick, which makes the flame form a wall-adherent disc-shaped flame with a thickness of 100~200mm and a diameter of 600-2000mm. This special temperature field, heat flow field, and pressure field are conducive to rapid heating of the workpiece, preventing oxidation, and saving energy. Therefore, the main application of flat flame burners is in industrial furnaces where the heated workpiece cannot be in contact with the open flame. Short-flame burners have shorter flames, like premixed ones, which have shorter flames. The designed burner bricks are drawn according to the drawings and then handed over to the refractory material manufacturer for production.
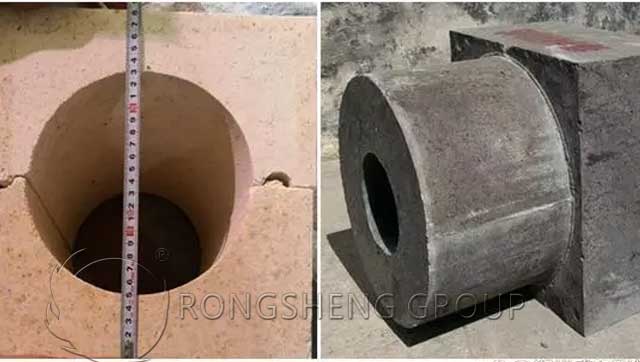
Forming of Burner Bricks
The forming process of burner bricks. Before production, first understand the operating conditions of the burner brick, such as combustion temperature, physical requirements, temperature changes, etc. After understanding these conditions, you can better choose the material and molding method of the burner brick. Three types of materials are generally used, namely silicon carbide burner bricks with better thermal shock resistance, mullite burner bricks, and corundum burner bricks with relatively high combustion ambient temperature. If the chemical atmosphere corrosion is serious, chrome corundum burner bricks should be used. When selecting materials, we should start from the reverse conditions of burner bricks and select materials from some vicious conditions that are not conducive to the use of burner bricks. The molding method can be pre-molded using refractory castables of different materials, or it can be produced through machine-made molding. However, machine-made molding needs to consider the size of the burner brick.
Most burner bricks are relatively large in size and relatively heavy in unit weight. The unit weight of some burner bricks can reach 300-500Kg, so the molding process needs to be considered in many aspects during production and manufacturing. In market applications, 80% are preformed with refractory castables and then go through drying and other processes to finally achieve the use effect.
Burner bricks need to have properties such as high-temperature resistance, corrosion resistance, and good thermal shock stability.
The burner brick is a refractory product for the burner part, which is arranged on the furnace wall burner. The gas burner brick is mainly used to heat the fuel to the ignition temperature in the burner brick, stabilize the combustion process, and organize the flame shape to meet the requirements of the heating process. On the one hand, air and gas burner bricks organize combustion, and on the other hand, they recover flue gas when not burning. The function of the burner brick is to heat the fuel in the burner brick to the ignition temperature, making it easy to ignite and burn quickly. Maintain a certain high temperature in the burner brick to stabilize the combustion process and avoid pulsation or combustion interruptions. Meet the requirements of the heating process to further mix fuel and air. Burner bricks are divided into chrome corundum burner bricks, corundum mullite burner bricks, high alumina mullite burner bricks, clay burner bricks, and silicon carbide burner bricks according to the materials used.
Since the flame of the burner brick burns directly in the burner, the burner brickworks in a high-temperature flame environment for a long time. Therefore, burner bricks are required to have properties such as high-temperature resistance, corrosion resistance, and good thermal shock stability. At the same time, it is also required to have good thermal insulation properties to improve the insulation effect of the furnace.
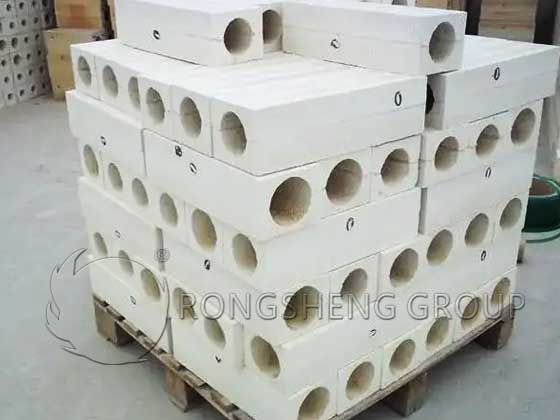
Existing burner bricks are made of refractory materials. Depending on the type of specific refractory materials, the burner bricks made have corresponding high-temperature resistance properties. However, some finished products do not have good thermal insulation properties, and some have certain thermal insulation effects, but the cost is higher. Overall, due to the temperature difference between the front and back, and inside and outside of the burner brick, various parts of the burner brick will be heated unevenly. Thermal stress is large, which can easily cause the burner brick to deform and even crack, affecting the life of the burner brick. Once the burner brick cracks, it will quickly cause the kiln body to deform and the kiln will not work properly. In addition, the burner is installed on the end face outside the burner brick. Since the burner brick body is made of refractory materials, its surface cannot achieve a high level of flatness. As a result, there will inevitably be a bonding gap between the burner and the burner brick installation end surface, which will also affect the thermal insulation effect of the furnace.
In order to solve the thermal insulation effect of the burner brick during use, the surrounding areas and inner holes of the burner brick are installed. Make a layer of refractory and heat-insulating layer, which is made of nano-ceramic high-temperature heat-insulating coating. Thermal insulation coating is composed of nano hollow ceramic beads, aluminum silicate fibers, and heat-reflective energy-saving materials. The air in the nanoscale hollow ceramic bead cavity will not produce thermal convection after being heated. The air layer between the ceramic beads no longer produces thermal convection after being heated, and the paint coating forms a thermal insulation shielding layer composed of static air and inorganic materials. With heat-reflective energy-saving materials as an auxiliary, the thermal conductivity of the paint coating is close to the vacuum thermal conductivity, with a low thermal conductivity of only 0.03W/m·K, and the thermal insulation suppression rate can reach about 90%. It has no flash point or ignition point and can be used for fire-resistant barbecue for a long time. There is no combustion at room temperature and high temperature, and no volatile toxic gases are produced.
The thickness of the nano-ceramic high-temperature thermal insulation coating applied to all parts of the burner brick is 1-8 mm. Different thicknesses can be used to achieve different insulation effects. The thickness of the refractory insulation layer of 1-8 mm can meet the heat insulation requirements of the furnace burner bricks, and different parts of the burner bricks have different layer thicknesses. To adapt to the working temperature of different parts of the burner brick, the bricks in the refractory insulation layer are heated relatively evenly, reducing the generation of thermal stress and extending the service life of the burner brick.
To purchase high-quality refractory brick products, corrosion-resistant burner bricks, and high-quality thermal insulation bricks, please contact RS refractory brick manufacturers. RS Refractory Materials Manufacturer is a powerful manufacturer and seller of refractory bricks. High-quality products and perfect customer service ensure the long life and high-quality operation of high-temperature industrial furnace linings.