Features and applications of anti-spalling high alumina bricks. Anti-stripping high alumina bricks were developed in cooperation with scientific research departments since the 1980s. It is widely used in the transition zone before and after the new dry process cement rotary kiln. At present, what are the advantages of anti-spalling high alumina bricks? The RS refractory bricks manufacturer will introduce starting from the development of anti-spalling high alumina bricks.
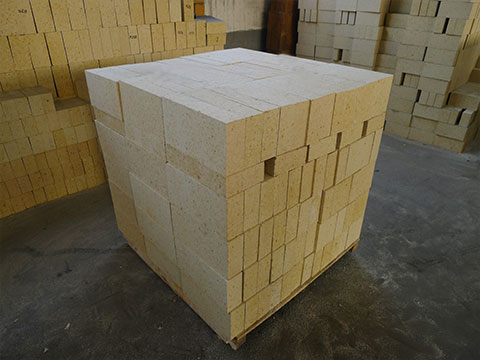
Development of Anti-Spalling High Alumina Bricks
The first generation of anti-spalling high alumina bricks is made of high alumina bauxite and zircon. It mainly uses the reaction of alumina and zircon during sintering to form mullite and zircon to improve the thermal shock resistance of the material. The key point of the process is to control the sintering temperature and the particle size of zircon. Produce a certain degree of oblique zircon, obtain higher compressive strength.
The first generation of anti-spalling bricks has been well used in large and medium-sized cement pre calcining furnaces, kiln tail smoke chambers, indoor decomposition zones, coolers, and other parts with low temperatures. However, the first generation of anti-stripping bricks sometimes have problems in the transition zone and cooling zone of the cement rotary kiln where the temperature is relatively high.
In the 1990s, scientific research departments once again cooperated and developed the second generation of anti-spalling high alumina bricks. It uses high alumina bauxite and zircon powder as additives, combined with resin. Give full play to the micro-crack “toughening” effect of zirconia, and improve the high-temperature resistance of spalling high alumina bricks.
Compared with the first-generation anti-stripping high alumina brick, the second-generation anti-spalling brick has the same thermal shock resistance. The high-temperature flexural strength, load softening temperature, and compressive strength of the second-generation anti-spalling brick are greatly improved compared with the first-generation anti-stripping high alumina brick. Especially in the transition zone of cement rotary kiln, the effect is greatly improved.
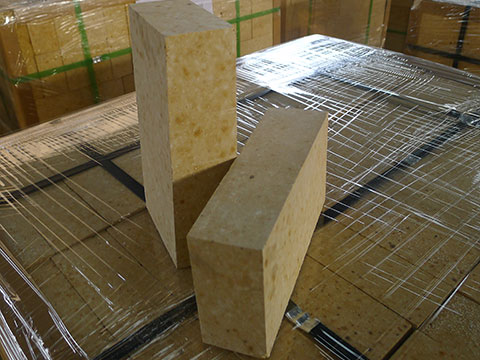
What are the Advantages of Anti-Spalling High Alumina Bricks?
There are many improvements in the use effect of anti-spalling high alumina bricks on the transition zone of cement rotary kilns. Compared with other refractory brick products, what are the advantages of anti-spalling high alumina bricks? The RS refractory brick manufacturer will explain the comparison between the anti-spalling high alumina brick and the high alumina brick, and the anti-stripping high alumina brick and the magnesia chrome brick.
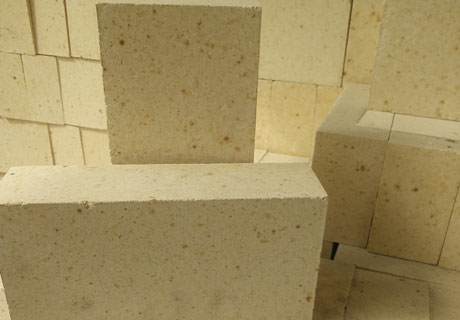
The Difference between Anti-Spalling High Alumina Brick and High Alumina Brick
The anti-stripping high alumina brick is compared with the high alumina brick. The anti-spalling high alumina brick is made of high alumina bauxite and zircon, with high strength, chemical corrosion resistance, low thermal expansion coefficient, and low thermal conductivity. High alumina bricks use high alumina bauxite as raw materials, and their chemical resistance is not as good as anti-stripping high alumina bricks. The main reason is that the anti-stripping high alumina brick has better thermal shock stability than the high alumina brick.
Anti-spalling high-alumina bricks have a strong anti-stripping ability, resistance to potassium, sodium, sulfur, chlorine, and alkaline salts, and low thermal conductivity. It is an ideal material for the cement kiln transition zone and decomposition zone. Its notable feature is its good thermal shock resistance and strong ability to adapt to the environment. It is mostly used in the preheating zone of the rotary kiln or in the calciner and the grate cooler.
There is also a difference in the firing temperature between high alumina bricks and anti-spalling high alumina bricks. The high-temperature firing temperature of anti-stripping high alumina bricks is 30-50℃ higher than that of high alumina bricks. The anti-falling high alumina brick has lower thermal conductivity and higher load softening temperature than high alumina brick.
High alumina bricks cannot enter the large cement rotary dry process kiln. Because its service life is too low, frequent repairs and shutdowns of the kiln cause considerable energy loss and economic loss. More importantly, it cannot overcome the inherent shortcomings of using it in harsh areas.
The refractoriness of high alumina refractory bricks is mainly affected by the content of Al2O3. The refractoriness increases with the increase of Al2O3 content. High alumina bricks are close to neutral refractory materials and can resist the erosion of acid slag and alkaline slag. Because it contains SiO2, the ability to resist alkali slag is weaker than that of acid slag.
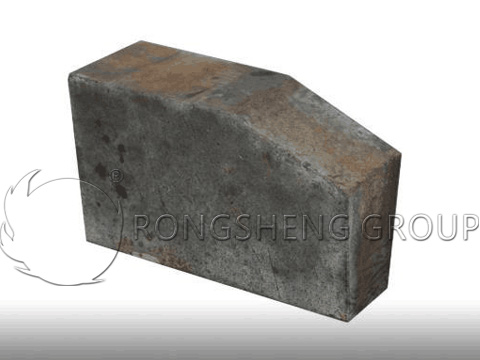
Several Characteristics of Anti-Spalling High Alumina Bricks Compared with Magnesia Chrome Bricks
The use of KBL-80 anti-spalling high alumina bricks and magnesia-chrome bricks in the wet short kiln firing zone has the following characteristics.
1) Good kiln skin hanging performance and kiln skin stability. The use of anti-stripping high alumina bricks is easy to hang the kiln skin, the thickness is 200mm, the kiln skin and the brick have a strong binding force, easy to hang, and not easy to fall, which is beneficial to the maintenance of the kiln skin. The temperature of the kiln body is basically around 300°C. This is mainly because the Al2O3 content in the anti-spalling high alumina brick is as high as 80%, and it reacts with the CaO in the clinker to form C3A. Adhere to the surface of the firebrick under high temperature and combine with the firebrick to form a firm whole, which enhances the bonding force between the kiln skin and the firebrick. This is also reflected in the kiln leather.
2) Good peeling resistance. When the kiln was shut down and the kiln skin was hit, the cross-section of the refractory bricks was inspected and no cracks were found in the refractory bricks. It overcomes the shortcomings that magnesia-chrome bricks always have 20-50mm thick faults on the surface of the fire bricks, which are torn off layer by layer as the kiln skin falls off. Ensure the fire brick has a long service life.
3) Strong chemical resistance. After stopping the kiln to play the kiln skin, it was found that the surface of the anti-flaking bricks was flat, the thickness of the metamorphic layer was 20-30mm, and a thin glazed film was formed on the brick surface to prevent the fire bricks from further erosion. Has strong resistance to chemical erosion.
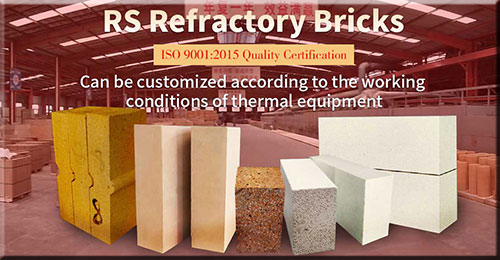
Rongsheng Anti-Spalling High Alumina Brick Manufacturer
Anti-flaking bricks can be used in the transition zone of the white ash-fired rotary kiln, and anti-flaking high alumina bricks can be used in the firing zone of the rotary kiln for scorching gemstones. There is also a small diameter rotary kiln for the smelting of non-ferrous metals, and some choose to use anti-spalling high alumina bricks. In summary, the high-temperature resistance and thermal shock resistance of the anti-spalling high alumina brick are much better than that of the high alumina brick. Compared with magnesia chrome bricks, it also has certain advantages in the use of certain parts of the rotary kiln. RS refractory brick manufacturers suggest that whether to use anti-stripping high alumina bricks, high alumina refractory bricks, or magnesia chrome bricks, should be determined according to the corrosion situation of the furnace and the working temperature. In this way, the service life of the kiln can be extended and production costs can be saved.