Anti-flaking high-alumina bricks have strong high-temperature volume stability, excellent thermal shock resistance, wear resistance, and chemical corrosion resistance. Anti-stripping high-alumina bricks are mainly used in the transition zone of cement rotary kilns, calciner, tertiary air ducts, and other thermal equipment requiring thermal shock resistance. Anti-stripping high-alumina bricks are high-alumina bricks with anti-stripping properties produced based on high-alumina clinker and added with ZrO2 or other materials. Rongsheng refractory brick manufacturer specializes in providing high-quality anti-stripping high-alumina bricks and high-alumina bricks containing ZrO2.
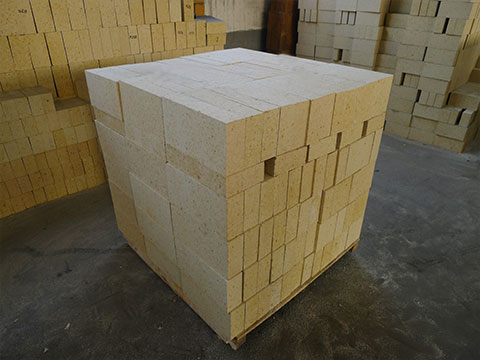
Why Do Cement Kilns Use Anti-Stripping High Alumina Bricks?
As the basic material in the refractory industry, high alumina bricks have the characteristics of high refractoriness, relatively high softening temperature under load (about 1500°C), and good erosion resistance. It is widely used in industrial kilns in various industries. However, due to the high content of the corundum phase in ordinary high alumina bricks, the crystallization of the corundum phase in the sintered product is relatively large. When encountering rapid cooling and rapid heating, it is prone to cracking and peeling. The number of thermal shock stability under 1100°C water cooling conditions can only reach 2-4 times at most. In the cement production system, high alumina bricks can only be used in the transition zone of the rotary kiln, the kiln tail, and the calciner preheater due to the limitation of the sintering temperature and the performance requirements for the refractory material to stick to the kiln skin.
In the cement rotary kiln, the gas containing sulfur, chlorine, and alkali components is discharged to the kiln tail along with the flue gas. The sulfochlor-alkali components in the flue gas are condensed at the kiln tail and then brought into the firing zone along with the materials. The sulfur-chlor-alkali components just circulate and precipitate in the transition zone area, forming an alkali cycle, causing the chlor-alkali components in the transition zone to exceed the standard. These chlor-alkali components will cause very serious erosion of refractory materials. The chlor-alkali components with low melting points penetrate into the refractory bricks, condense and deposit in the lower temperature part of the refractory bricks, and fill the pores of the refractory bricks, causing the refractory bricks to be dense and deteriorated. Because the thermal expansion coefficient of the metamorphic layer of refractory bricks is inconsistent with that of normal refractory bricks, structural spalling, and damage will occur when encountering rapid cooling and rapid heating. Therefore, the erosion of chlor-alkali components and poor thermal shock stability are the main reasons for the damage to refractory bricks in the transition zone area. The high-alumina brick has a high porosity. When it is used at the kiln tail, the alkali salt components in the flue gas will penetrate into the interior of the high-alumina brick after condensation at the kiln tail. The internal structure of the hot end of the high alumina brick is dense, and layered peeling occurs when it encounters rapid cooling and rapid heating. The peeling thickness can reach 40-100mm, resulting in final damage to the refractory brick. Under these conditions, anti-stripping high alumina bricks came into being.
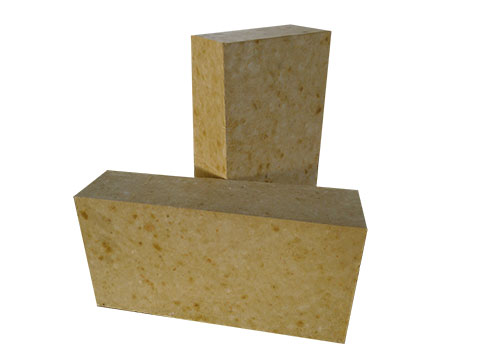
Anti-Stripping High Alumina Brick is a High Alumina Brick Containing ZrO2
Adding a certain amount of ZrSiO4 in the production of high alumina bricks can improve the overall thermal shock resistance of the material, that is, the anti-stripping performance we are talking about. High alumina bricks will be subjected to the start and stop of the kiln and temperature changes after normal production during use, which will inevitably cause a certain cold pressure impact on the high alumina bricks, causing cracks on the surface of the high alumina bricks and eventually delamination and peeling off. Therefore, a certain amount of ZrSiO4, which can strengthen and toughen raw materials, is added in the later production technology to improve the anti-stripping performance of high-alumina bricks.
The mechanism of ZrSiO4 improving high-alumina brick products is that a certain amount of t-ZrO2 is decomposed at high temperature, and t-ZrO2 then undergoes a phase transformation of m-ZrO2 under stress mutagenesis. And the phase itself and the cracks produced by the phase change. On the one hand, energy is absorbed due to the generation of new crack surfaces, and on the other hand, the volume expansion produced by phase change particles will also generate compressive stress on the main crack, hindering the expansion. Therefore, the spalling resistance of high alumina bricks can be improved.
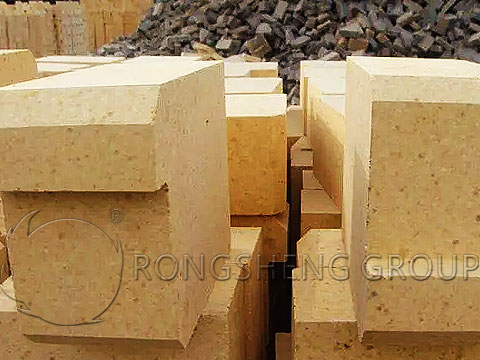
Application of Rongsheng Anti-stripping High Alumina Brick
Rongsheng refractory brick manufacturer’s anti-shedding high-alumina bricks have a regular appearance, smooth flow, accurate scale, and complete varieties. The refractory products of high alumina bricks for metallurgical cast steel are various funnel bricks suitable for various steel types (including stainless steel and various alloy steels) for flat cast steel. Cast pipe bricks, foundation bricks, straight flow steel bricks, single hole flow steel bricks, two and three-flow steel bricks, flow steel tail bricks, ingot mold bottom bricks, etc. The product has high refractoriness, good crack resistance, and strong corrosion resistance.
Production of ladle lining bricks, curved lining bricks, fired and unfired plug bricks, sprue bricks, seat bricks, and sleeve bricks of cast steel in ladles. Excellent raw materials and common technology make the product have good high-temperature physical and chemical properties, resistance to erosion, no deformation, and no shedding.
According to a certain ratio, the fired product is made by high-pressure molding. The product has strong anti-shedding ability and also has high potassium, sodium, sulfur, fluorine, and alkaline salt corrosion, low thermal conductivity, and other properties. It is an ideal material for the transition zone and decomposition zone of cement kiln. The vertical wall of the three-dimensional lime kiln is generally made of anti-shedding high-alumina bricks, and the special parts are made of phosphate ramming material or castable. Use high-strength clay bricks for non-critical parts.
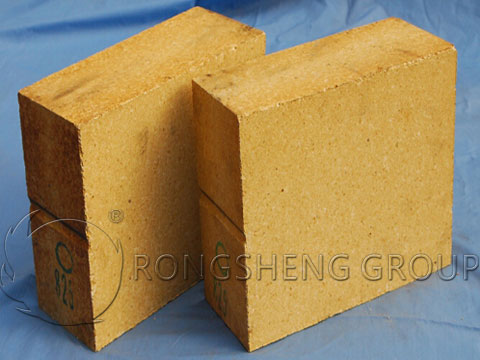
Anti-Stripping High Alumina Brick without ZrO2
Anti-stripping high-alumina bricks are high-alumina bricks with anti-stripping properties produced based on high-alumina clinker and added with ZrO2 or other materials. It can be divided into two categories, one is the anti-stripping high-alumina brick containing ZrO2, which is represented by GKBL-70 in the new national standard code. The other is anti-stripping high-alumina bricks that do not contain ZrO2, which are represented by KBL-70 in the new national standard code.
Anti-flaking high-alumina bricks can resist high-temperature thermal load, the volume does not shrink and has a uniform expansion, and no creep and collapse occur. It has relatively high normal temperature strength and high-temperature hot state strength, and high load softening temperature. It has good thermal shock resistance, resists the influence of rapid temperature changes or uneven heating, and does not crack or peel off. The difference between the anti-stripping high-alumina bricks containing ZrO2 and the anti-stripping high-alumina bricks without ZrO2 lies in their different anti-stripping mechanisms. ZrO2-containing anti-flaking high-alumina bricks use ZrO2 with excellent corrosion resistance to resist the erosion of sulfur, chloride, and alkali by adding zircon materials. At the same time, at high temperatures, SiO2 contained in zircon will undergo crystal phase transformation, from cristobalite to a quartz phase, resulting in a certain volume expansion effect. Thereby, while reducing the erosion effect of preventing sulfochlor-alkali, it also prevents spalling during the hot and cold process. ZrO2-free anti-stripping high-alumina bricks are produced by adding andalusite on the basis of high-alumina bricks, and the andalusite in the product is used to produce irreversible micro-expansion effects during secondary mullite in cement kilns. When the product is cooled, it will not shrink, offset the shrinkage stress, and will not cause structural peeling.
Compared with the anti-stripping high-alumina bricks without ZrO2, the anti-stripping high-alumina bricks containing ZrO2 have better penetration and erosion resistance of sulfur, chlorine, and alkali components. So the anti-stripping performance is better. However, since ZrO2 is a rare material and expensive, the cost and price are relatively high. The anti-stripping high-alumina bricks containing ZrO2 are only used in the transition zone of the cement rotary kiln, and the anti-stripping high-alumina bricks without ZrO2 are mostly used in the calciner of the cement production line.
In cement kilns, due to the high price of anti-stripping high-alumina bricks containing ZrO2, there is no obvious price advantage compared with silica bricks. The market has been basically replaced by silica bricks. At present, the anti-flaking high-alumina bricks that do not contain ZrO2 are mostly used.
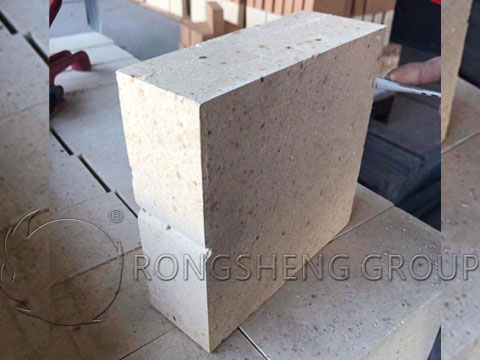
Rongsheng Refractory Bricks Manufacturer
Rongsheng Refractory Brick Manufacturer is a refractory brick manufacturer with rich production and sales experience. The refractory brick products of Rongsheng manufacturers have been sold to more than 80 countries around the world, such as South Africa, Chile, Egypt, Colombia, Uzbekistan, Italy, Indonesia, Ukraine, Hungary, Spain, Kenya, Syria, Zambia, Oman, Venezuela, India, Peru, the United States, Ethiopia, etc. Moreover, the service life of our refractory brick products in the rotary kiln is also improved compared with before. The anti-stripping high alumina bricks, silicon carbide mullite bricks, phosphate bricks, and other refractory bricks produced by our factory are all well-received and recognized by customers. Moreover, our newly developed insulation brick products have low thermal conductivity, almost zero shrinkage, and long service life. Applied to the rotary kiln, it can effectively reduce the temperature of the outer wall of the rotary kiln. Contact us for free details and a quote.