Chrome corundum brick is a refractory brick product with chromium added to the corundum brick. It has good wear resistance, corrosion resistance, high-temperature resistance, impact resistance, and other properties. The price of chrome corundum bricks varies based on market demand as well as differences in chromium content. Generally, the price of chromium corundum bricks with a chromium content of 5% to 10% is about 13,000 yuan/ton, while the price of chromium corundum bricks with a chromium content of 30% to 50% is more than 20,000 yuan/ton. The price of chrome corundum bricks is closely related to market demand. When market demand is high, the price will rise accordingly, and when market demand is low, the price will fall. In addition, the difference in chromium content is also a key factor affecting the price of chromium corundum bricks. The higher the chromium content, the higher the price.
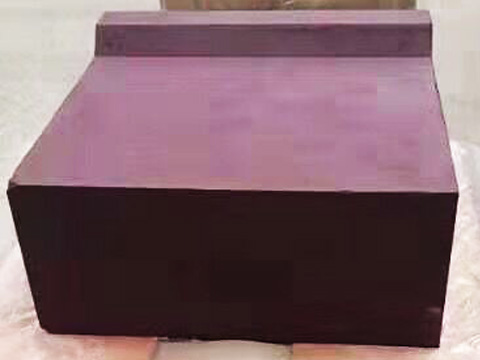
Factors Affecting the Price of Chrome Corundum Bricks
In actual production, the price of chrome corundum bricks is also affected by other factors. Such as production costs, production processes, sales channels, etc. Production costs include raw material procurement costs, production equipment costs, labor costs, etc., which also directly affect the price of chrome corundum bricks. In addition, the production process of chrome corundum bricks will also have an impact on its price. High-end production processes will make the price of chrome corundum bricks higher. At the same time, different sales channels will also lead to differences in the price of chrome corundum bricks. The price may be lower if purchased directly from the manufacturer than from an agent or dealer. Based on the above factors, the price of chrome corundum bricks is not only related to the chromium content, but also related to market demand, production cost, production technology and sales channels. The prices of chrome corundum bricks of different specifications and quality will be different. If you need to purchase chrome corundum bricks, it is recommended to choose a reliable brand and channel after comparing many aspects. In addition, according to the different parts used in different kilns, their shapes and sizes also affect the price of chrome corundum bricks.
Rongsheng refractory brick manufacturer provides chrome corundum refractory bricks for the following types of industrial furnaces. The use effect is good and the life of the furnace lining is extended. Rongsheng Manufacturer’s chrome corundum bricks have rich project cases. Contact us for a free quote on refractory lining solutions and chrome corundum bricks. Customized chrome corundum brick sizes and shapes, competitive prices and efficient solutions will definitely save you production costs.
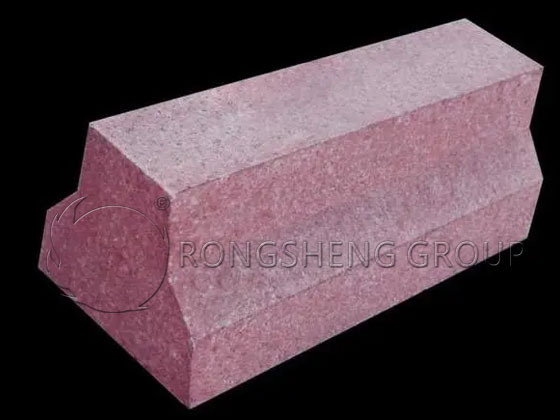
Application of Chrome Corundum Bricks in Cupola
Chrome corundum bricks are the best choice for cupola linings. The melting furnace temperature of the waist cupola is 1450~1500℃, the silicon burning loss is <8%, the manganese burning loss is <13%, the coke-to-iron ratio is 1:7~9, the iron oxide content is <6% and it also has the characteristics of good energy saving effect.
In practice, ordinary refractory bricks and refractory materials are used to build a cupola. After 50 kilograms of iron are started to be tapped, the temperature of the molten iron can reach over 1410°C immediately and reach 1450~1550°C in half an hour. However, when the furnace is turned on for 1 hour and 50 minutes, the temperature will drop again, to about 1410°C. When I opened the furnace the next day, I found that all the firing materials near the second row of air vents had been eroded away, and the waist-stuck furnace became a straight cupola furnace, thus losing its advantages. In order to maintain the advantages of the waisted cupola, the refractory material of the furnace lining must be solved.
After research and demonstration, this problem can be solved well by using chromium corundum bricks with excellent performance as furnace lining.
Chrome corundum brick is a product made by reducing Cr2O3 with pure aluminum. It is equivalent to a composite refractory material made by melting pure corundum (or white corundum) and adding more than 10% pure Cr2O3. Due to the high content of Cr2O3 and the combination with the corundum matrix, it is called chromium corundum brick. During the production process, chrome corundum bricks are smelted at temperatures above 2000°C, and their composition is relatively uniform because they have good thermal stability and high-temperature chemical stability.
Chrome corundum bricks are one of the key factors in improving the service life of furnace linings due to their high density. The chromium corundum bricks that are cooled and solidified after melting have small porosity. Therefore, the key parts of the furnace body are built with chromium corundum bricks, and the gaps between the bricks are filled with chromium corundum powder and binder.
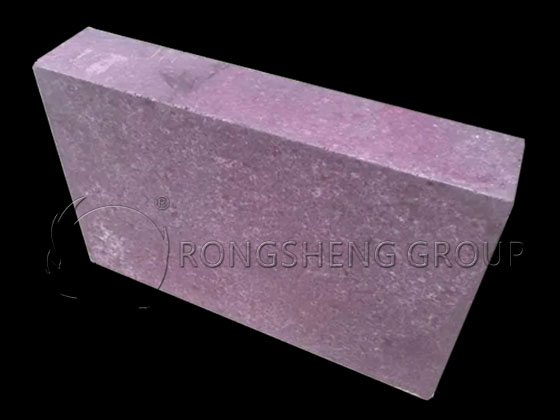
Application of Chrome Corundum Bricks for Heating Furnaces
Chrome corundum bricks are mainly used on the steel-pushing platform of side-exit steel heating furnaces. The use conditions of this part are harsh, including mechanical wear at high temperatures and chemical erosion. Years of practical experience have proven that general refractory materials such as clay, high alumina, and mullite are difficult to meet the use requirements. Only chromium corundum materials can meet such use conditions.
Chromium Corundum Bricks in Nickel-Iron Ore Furnaces
Chrome corundum bricks and magnesia-chromium bricks are commonly used refractory bricks for nickel-iron ore furnaces. In nickel-iron ore furnaces, which one is suitable as the refractory material for the furnace wall, chromium corundum bricks or magnesia-chromium bricks?
- Resistant to chemical attack
In the temperature range of 1400°C to 1600°C, the degree of erosion and penetration of nickel-iron slag into the two refractory materials is directly proportional to the temperature. The corrosion penetration rate of chromium corundum bricks with temperature is higher than that of magnesia chromium bricks. The increase in temperature will increase the penetration of slag into refractory materials.
The corrosion resistance of chromium corundum to nickel-iron slag is better than that of magnesia-chrome bricks. The corrosion effect of slag on chromium corundum is greatly affected by the composition of the slag. Arrangement of factors affecting slag corrosion: refractory type, FeO content, alkalinity, SiO2MgO. The factors affecting furnace lining penetration are arranged as refractory type, FeO content, and SiO2, and MgO alkalinity. Chrome corundum bricks have good corrosion resistance, while magnesia-chromium bricks have strong penetration resistance.
The ability of chromium corundum bricks to resist the erosion of nickel-iron slag is better than that of magnesia-chromium bricks, but its resistance to penetration is poor. In the selection of refractory materials for nickel-iron ore furnaces, the level of selected factors is related to the required index. The smaller the index of required erosion, the better. Therefore, chrome corundum bricks are more suitable for nickel-iron ore furnaces.
- Resist physical damage
After the infiltration of nickel-iron slag, the normal temperature compressive strength of chrome corundum bricks dropped by 65%, and the compressive strength dropped to 66.44Mpa. The compressive strength of new magnesia-chrome bricks is 45Mpa. In other words, the compressive strength of chromium corundum bricks after the nickel-iron ore hot furnace slag erosion experiment is still higher than the compressive strength of new magnesia-chrome bricks. The good wear resistance, erosion resistance, and impact resistance of refractory materials correspond to high compressive strength. Furthermore, the thermal conductivity of chrome corundum bricks at high temperatures is 1.8 times that of magnesia-chrome bricks. Therefore, from the perspective of resistance to physical damage of the “condensing” furnace lining, chromium corundum bricks are more suitable as furnace wall refractory materials for submerged arc furnaces than magnesia-chrome bricks.
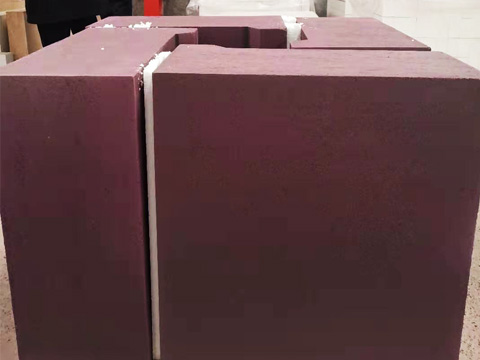
Why Choose Chromium Corundum Bricks for Hazardous Waste Incinerators?
Chrome corundum bricks have become key materials in hazardous waste disposal and incineration due to their excellent fire resistance, corrosion resistance, mechanical strength and chemical stability. It can cope with high-temperature environments, protect equipment from corrosion damage, improve equipment stability and reliability, and ensure the safety and efficiency of the incineration process.
In the process of hazardous waste (hazardous waste) disposal and incineration, the selection of chrome corundum bricks is particularly critical, thanks to its excellent fire resistance and corrosion resistance. During the incineration process, the high temperature and harmful gases released by hazardous wastes place extremely high demands on equipment materials, and chrome corundum bricks are an effective helper in meeting this challenge.
Due to its excellent fire resistance, chrome corundum bricks can easily cope with high-temperature environments of hundreds of degrees Celsius or even higher during the incineration process. Its excellent thermal stability ensures the stable operation of the equipment under high-temperature conditions, avoids equipment failure or damage caused by high temperature, and thus ensures the smooth progress of the incineration process.
Chrome corundum bricks are ideal for hazardous waste disposal and incineration processes due to their excellent fire resistance, corrosion resistance, mechanical strength and chemical stability. Its application not only improves the stability and reliability of the equipment but also provides a strong guarantee for the safe and efficient disposal of hazardous waste.
It is noteworthy that, if there are materials with high fluorine content in the materials of a hazardous waste incinerator, and the fluorine content in the materials is high, reaching 1-4%, F and Si in the refractory materials will easily react to form SiF4 gasification. Causes structural damage to the lining matrix and rapid erosion. Therefore, this kind of kiln lining material must strictly control the impurity content in the refractory material, especially the silica content must be low. Low silicon chromium corundum brick. The use of chromium corundum material with a Cr2O3 content of 9-15% can meet the normal operation needs of the rotary kiln.