High-chromium corundum brick is a type of high-temperature refractory material with excellent properties such as high density, high strength, and good high-temperature wear resistance. It is widely used in high temperature and high wear environments such as gasification furnaces. However, at present, the service life of chromium corundum bricks in the gasifier barrel and dome is generally 8,000 to 20,000 hours. The service life of slag mouth and cone bottom high chromium corundum bricks is generally 3000 to 6000 hours. The mismatch in the service life of various parts greatly affects the overall service life of the gasification furnace and the rhythm of the entire production and increases the operating cost. Rongsheng Refractory Materials Manufacturer, based on years of experience in the production and sales of refractory materials, recommends that chromium corundum bricks for gasifiers in the petrochemical industry should be low silicon, low iron, low alkali, and high purity.
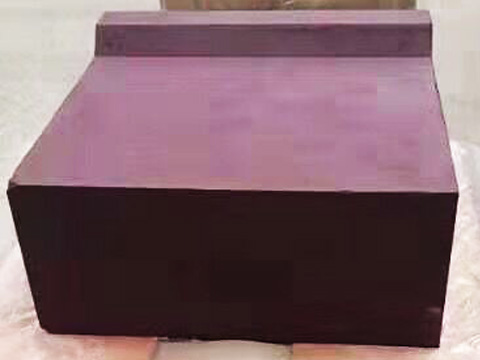
Chrome corundum bricks, high chromium bricks. In this context, it is of great significance to carry out relevant research to further improve the service life of chromium corundum bricks. First of all, we can start with the optimization of materials, look for more wear-resistant and high-temperature-resistant raw materials, improve the physical and chemical properties of chrome corundum bricks, and improve their overall performance. Secondly, we can start with the production process to improve the production process, improve production efficiency, reduce production costs, and at the same time ensure the quality and performance of the product. In addition, we can start from the structural design to optimize the structural design of high-chromium corundum bricks. Improve its load-bearing capacity and wear resistance, further extending its service life.
According to the actual situation of the gasifier, we can also start from the operation and maintenance aspects. Strengthen the management and maintenance of gasifiers, promptly discover and deal with problems with high-chromium corundum bricks, and extend their service life. For example, regular inspection and maintenance of high-chromium corundum bricks can be strengthened, and seriously aged high-chromium corundum bricks can be replaced in a timely manner. Avoid overall failure due to local damage. In addition, a series of measures can be taken during the operation of the gasifier. Such as controlling the temperature in the furnace, reducing impact, etc. Reduce the wear and aging rate of high-chromium corundum bricks and extend their service life.
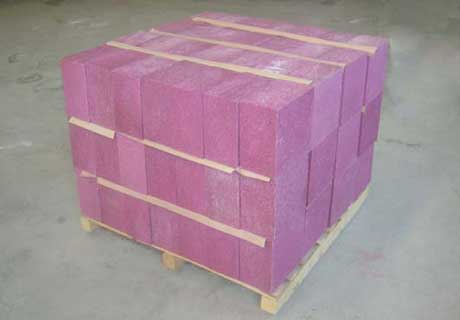
Working Conditions of Corundum Bricks for Gasifiers
Corundum bricks are made by calcining high-purity industrial alumina and then finely grinding it. Sometimes a small amount of MgO additive is added to improve its crystal structure. The pressed green body is calcined above 1850℃. Corundum bricks have strong slag resistance. It is stable to blast furnace ironmaking slag, fuel slag, and steel and iron melts.
Ablation Reaction of Corundum Bricks Used in Gasifiers by Reduction Reaction
Inside the furnace are strong reducing gases H2, CO, C, etc., with a high temperature of 1350°C and a high pressure of 8.53MPa.
The SiO2 content in the corundum brick is 0.2%, and the Fe3O4 content is 0.15%. Under high temperatures and high pressure, the gas in the furnace reacts with the silicon oxide and iron oxide in the bricks.
When the furnace is shut down and cooled down, silicon oxide and iron oxide are reduced, and the oxidation reaction is accompanied by a large volume expansion effect. This causes the internal stress of the corundum brick to continuously change and destroy the corundum brick. The porosity of corundum bricks increases, the strength decreases, and damage and peeling occur.
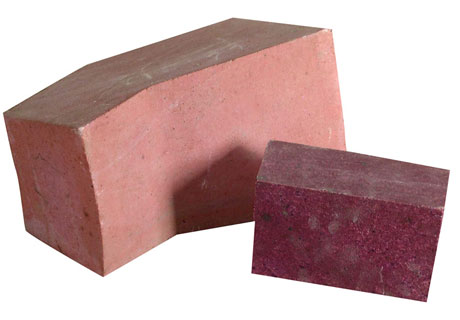
How to Improve the Service Life of Chrome Corundum Bricks for Gasifiers?
The main factors that affect the service life of chromium corundum bricks include the load of the gasifier, operating temperature, melting point of coal ash, ash and slag composition, and gasifier type.
Chrome Corundum Bricks on the Gasifier Barrel and Vault
The chromium corundum bricks on the gasification furnace barrel and vault, also known as high chromium bricks, have a service life of generally 8000 to 20000 hours. The service life of slag mouth and cone bottom high chromium bricks is generally 3000~6000h. The mismatch in the service life of various parts greatly affects the overall service life of the gasifier and the rhythm of the entire production, and increases operating costs. Therefore, it is of great significance to further improve the service life of high chromium bricks.
- (1) Increase the Cr2O3 content in the material and optimize its slag corrosion resistance. Since Cr2O3 material has good resistance to slag erosion and penetration, increasing the Cr2O3 content in chromium corundum bricks can effectively increase the service life of chromium corundum bricks. However, excessive Cr2O3 content will affect the sintering of the product and reduce the strength and thermal shock resistance of high chromium bricks. Therefore, while increasing the Cr2O3 content in high chromium bricks, attention must be paid to the reduction in strength and thermal shock resistance.
- (2) Increase the density of high-chromium bricks and reduce the apparent porosity on the brick surface. Increase the density of high chromium bricks, or use measures such as salt immersion and surface coating to fill the pores on the surface of high chromium bricks. It can effectively prevent the infiltration of slag and improve the service life of high chromium bricks.
- (3) Improve the strength of high-chromium bricks and increase their erosion resistance. High-chromium bricks are subject to strong erosion by high-speed airflow and entrained slag during use, and the erosion resistance and wear resistance of the bricks are directly related to their strength. By optimizing the particle gradation of the product, increasing the firing temperature of the product, adding new binders and burning accelerators, etc. All can achieve the purpose of improving the strength of high chromium bricks.
- (4) Use phase change toughening to improve the thermal shock resistance of high chromium bricks. High chromium bricks have poor thermal shock resistance and are prone to thermal shock cracks during the gasification furnace baking, feeding, and actual operation processes, which in turn accelerates the penetration and erosion of coal slag. The 3%~5% volume effect produced by the phase transition from tetragonal ZrO2 to monoclinic ZrO2 is utilized. Producing an appropriate amount of micro-cracks around ZrO2 particles can buffer the thermal stress generated inside the product due to temperature changes and improve the thermal shock resistance of the product.
- (5) According to the differences in the erosion rate and dominant damage mechanism of refractory bricks in different parts of the gasifier, certain properties of the refractory bricks in certain parts can be improved in a targeted manner. Comprehensive furnace-building technology is also adopted to extend the overall service life of the gasifier refractory materials.
To purchase high-quality chrome corundum brick refractory materials, please contact us. Rongsheng refractory brick manufacturer and sales manufacturer is a powerful manufacturer of refractory materials production and sales. Our products are of reliable quality and our after-sales service is guaranteed. Moreover, our professional technical team can customize refractory lining material solutions based on the actual working conditions of high-temperature industrial furnaces. For a quick quote, click here.