RS refractory brick manufacturer, dense zircon bricks for glass kiln for Sale. In recent years, the world’s glass industry furnaces have developed towards large-scale and energy-saving. Glass kiln’s high-density, low-porosity dense zircon bricks are a special variety suitable for the lining of the glass tank kiln for melting glass fiber. Generally, the production method is full powder, casting molding, and high-temperature firing.
The physical and chemical indicators of dense zircon bricks for glass-melting furnaces are divided into two grades: high-density ZS-G and dense ZS-Z. The physical and chemical indicators of Zircon Bricks used in glass kilns, the allowable deviation of brick size, and the appearance quality.
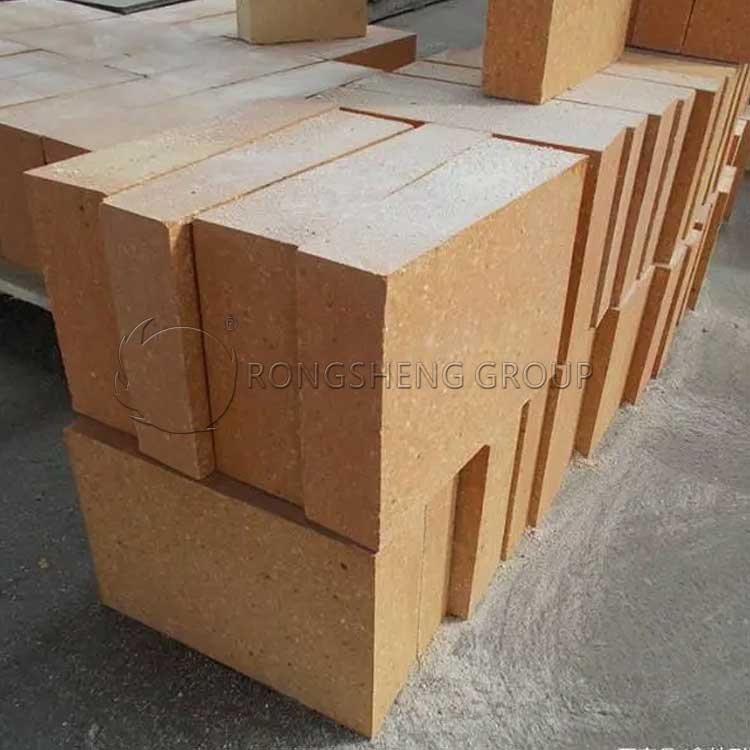
High-purity zircon raw materials, a small amount of high-efficiency admixtures, and appropriate firing temperatures are the key factors for producing high-density zircon bricks. The introduction of additives can ensure that the product can be fully sintered at a temperature far lower than the decomposition temperature of zircon. It can also reduce the reactivity, wettability, and permeability between the glass liquid and the bricks to varying degrees.
Zircon Bricks for Glass Melting Furnace
The molten glass and flame-flying materials in the glass-melting furnace will cause certain erosion and damage to the refractory materials, thereby affecting the service life of the glass-melting furnace. In addition, contamination of the glass liquid needs to be avoided and reduced. Therefore, the selection of refractory materials also has a great relationship with the life of the glass melting furnace and the quality of the glass.
Refractory materials for glass melting furnaces include shaped and unshaped refractory materials. Zircon bricks for glass melting furnaces are a commonly used refractory brick for glass kilns.
Zircon bricks for glass kilns use zircon as the main raw material, with binders and additives added. It is prepared according to the proportion, stirred, kneaded, shaped, dried, and then fired at high temperature. Zircon bricks are divided into high-density type and dense type according to the production process and physical and chemical indicators.
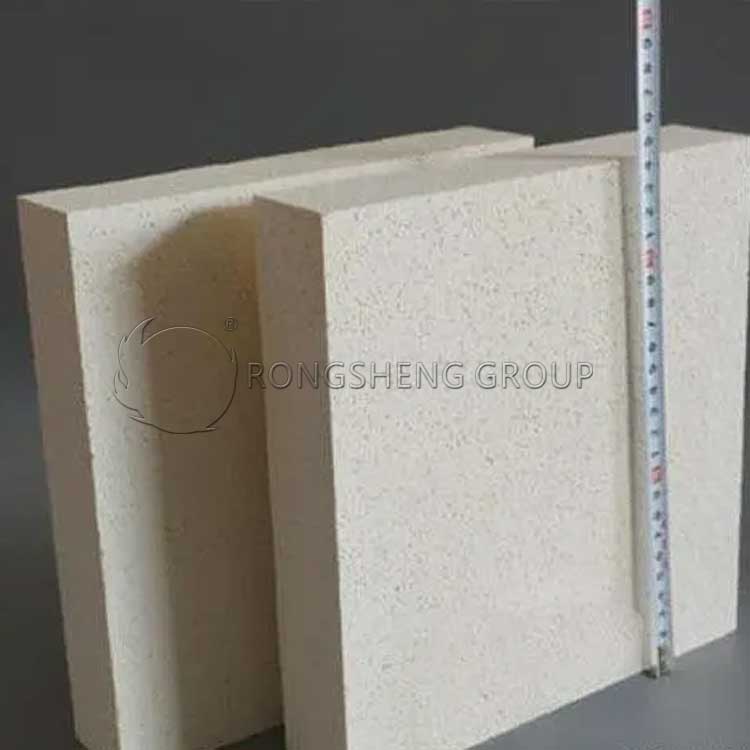
Performance of Dense Zircon Bricks for Glass Kilns
- High refractoriness and high charge softening temperature.
- Strong resistance to slag liquid erosion and acid resistance.
- High compressive strength.
- Good thermal shock resistance.
Where are dense zircon bricks for glass kilns mainly used? Zircon bricks are used as the working layer of the glass kiln wall and have high density. As the working layer of the pool wall, it has strong resistance to the erosion of glass liquid. What is the price of dense zircon bricks for glass kilns? The current price of zircon bricks on the market is around 24,000 yuan. Price information will change according to changes in various uncertain factors. The specific price can only be determined after contacting the zircon brick manufacturer.
How to Improve the Slag Resistance Performance of Zircon Bricks?
Zircon bricks have higher refractoriness and temperature reaching the softening point under load, a small thermal expansion rate, and are not easily dissolved by a chemical attack by slag. However, its resistance to penetration (wetting resistance) is poor, and slag can penetrate into the interior of the brick through the pores. At the same time, it reacts with the decomposed zircon particles to form a metamorphic layer, causing the brick structure to collapse. In order to improve the use effect of zircon bricks, the permeability of its slag must be reduced. Improvement methods:
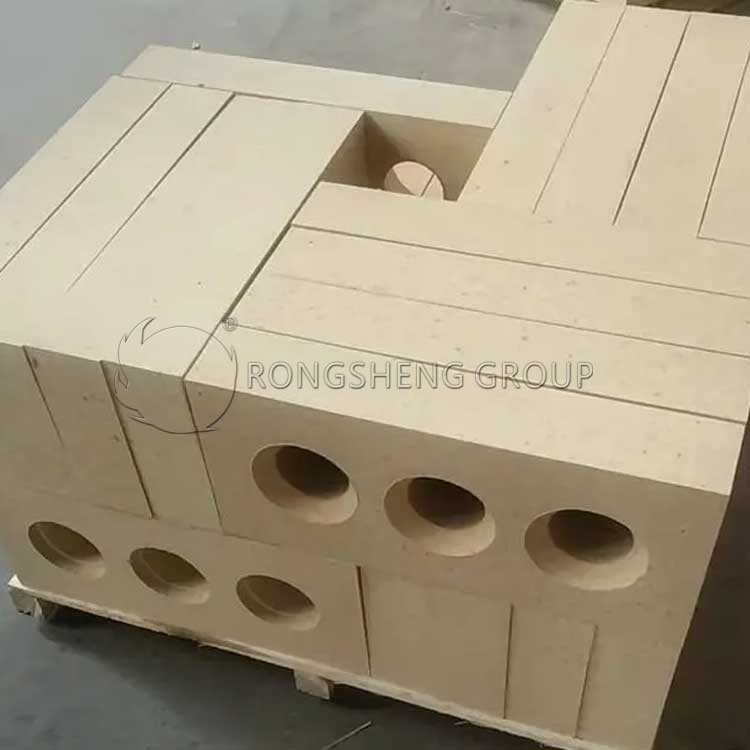
① By adjusting the particle composition and changing the molding method, products with low porosity and air permeability can be produced. However, the thermal shock stability of products made by this method will inevitably be reduced.
②Add certain additives to the brick to increase the viscosity of the product produced by the interaction between the brick and the slag.
Clay bonded zircon bricks, the type and amount of clay used largely affect the properties of the brick. Adding clay will reduce the refractoriness of the product because A1203 has a solvent effect on zircon. In the ZrO2-A1203-SiO2 ternary system, when the composition is ZrSi04 15%, A1203 15%, and SiO2 70%, a co-melting liquid phase is generated, and its melting point is 1610°C. As the firing temperature increases, the apparent porosity of clay-bonded zircon bricks decreases, the air permeability increases, and the amount of coarse pores increases. The compressive strength and high-temperature flexural strength are improved, the corrosion resistance of the product is improved, and the thickness of the permeable layer is increased.
When not adding binding clay, change the amount of zircon powder in the ingredients. The test results of firing at 1500℃ show that as the amount of zircon fine powder increases, the air permeability decreases, the number of pores increases, and the corrosion resistance of the product changes. When the amount of zircon fine powder is 60%, the thickness of the permeable layer is the thinnest.
From the above, it can be seen that in order to adjust the corrosion resistance of the product, reduce the air permeability, improve the pore distribution, and produce zircon products with strong penetration resistance. In terms of technology, it is necessary to consider the appropriate firing temperature, add an appropriate amount of zircon fine powder, and use a small amount of bonded clay.
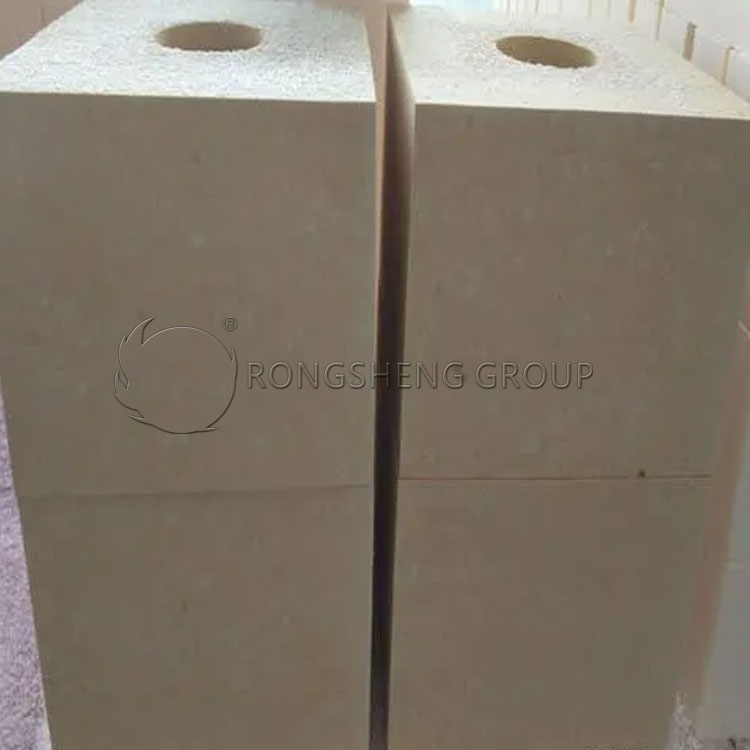
Applications of Sintered Zircon Bricks
Zircon bricks contain 67.23% zirconia and 32.77% silica. Cubic crystal system, usually in square columnar shape. Mohs hardness is 7.5, and the expansion coefficient at 20~1000℃ is 4.2×10-6/℃. The melting point is 2430℃. The bulk density is 3.60~4.3g/cm3. The apparent porosity is 0%~18%. Load softening temperature > 1550℃. It is prepared by semi-dry pressing and calcination at 1600°C. Mainly used for steel drum lining and sizing nozzles for continuous molten steel injection.
Refractory brick products are fired with zircon as the main raw material. Zircon is ZrO2-SiO2. The chemical formula of the compound in this system is ZrSiO4. The theoretical chemical composition of zircon is ZrO267.2% and SiO23.8%.
Zircon bricks have excellent properties, such as high-temperature resistance, good thermal shock resistance, slag erosion resistance, and molten glass erosion resistance. Zircon bricks work stably in an oxidizing atmosphere and will not chemically react with molten metal. Its physical properties and chemical composition.
The zircon in the original zircon ore of the raw material is symbiotic with quartz, ilmenite, garnet, monazite, and rutile. Therefore, zircon raw ore must be processed and made into zircon concentrate before it can be used in mines. The raw zircon ore is gravity-separated to remove quartz and gangue quartz minerals. Ilmenite, garnet, and monazite are removed by magnetic separation. Rutile is removed by flotation to obtain zircon concentrate. Zircon concentrate can be divided into three grades: 65, 63, and 60 according to the ZrO2 content.
When zircon is heated to a certain temperature, it can decompose into cryptocrystalline ZrO2 and amorphous SiO2. Due to the purity of the zircon and the impurities contained in it, the particle size and retention time of the raw materials, the decomposition temperature of zircon is also different. The decomposition temperature range is 1540~2000℃. Zircon was heated at 1600°C for 2 hours, and only a small amount of zircon was decomposed. After heating at 1750°C for 2 hours, the decomposition rate of zircon was 50%. When heated to 1900℃~2000℃, the decomposition rate can reach 100%. The presence of impurities such as Al 2O3 and CaO reduces the decomposition temperature of zircon. Therefore, when preparing zircon clinker, its pre-sintering temperature must be lower than the decomposition temperature of zircon (1540°C).