Corundum (α-Al2O3), low viscosity and low vapor pressure are favorable factors for the production process of molten corundum materials and fused casting products. Various corundum materials and products can be produced using industrial alumina and a small amount of quartz sand (about 3%) as raw materials.
Corundum Material
The white molten block formed by melting, cooling and recrystallization of industrial alumina in an electric arc furnace is electric fused white corundum material. Pay attention to the degree of refining, so that the K and Na alkali metal vapors are completely removed, and dense corundum material can be obtained. The industrial alumina raw material is spread into a disc-shaped material layer of a certain thickness in the electric arc furnace. After the arc is started, the material is added and smelted at the same time. The smelting system is controlled to ensure that the furnace charge maintains a relatively stable temperature range of 1900~2000℃ during the smelting process. The alumina crystals in this area develop rapidly in the two-dimensional direction, and the corundum grains are plate-shaped, that is, plate-shaped corundum material is obtained.
Alumina is heated to 2200~2300℃ (200~300℃ higher than the melting point) in the electric arc furnace. At this time, the melt viscosity is low, and the volume expansion of alumina is more than 35%. Control the melt flow rate and use compressed air to blow the melt droplets. The surface of the droplets first cools and solidifies into balls, and the internal liquid continues to cool and shrink under the action of external force, forming a hollow shrinkage cavity, that is, a corundum hollow ball.
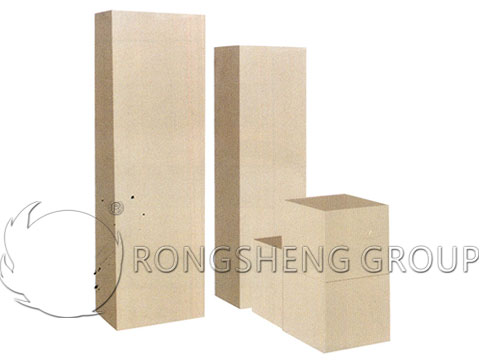
Alumina Fused Cast Bricks
Alumina fused cast bricks are divided into: α-Al2O3 bricks containing 95%~98% Al2O3, (α-β)-Al2O3 bricks containing 2%~5% to 53%~50% β-Al2O3, and β-Al2O3 bricks containing 5%~6% Na2O and β-Al2O3 greater than 97.5%. The fused cast α-Al2O3 refractory products have high strength, but low thermal shock resistance. The porosity and thermal shock resistance of β-Al2O3 bricks are enhanced, and the thermal shock resistance of (α-β)-Al2O3 bricks (Na2O 3.6%~4%) is very low, while the porosity is not high (3%~5%). The alumina batch melts when the arc is closed (1~2h). The unit power consumption is 15~18 GJ/t. The melt is cast in an equipped iron or graphite mold with a favorable insulation cap and vibrated for 5~8min. The formed skin is broken through several times in the favorable insulation cap and a new portion of the melt is poured. Later, the favorable insulation cap is removed, the mold is disassembled (after 12~15min after pouring), and the poured ingot is placed in a hot box and filled with alumina or dolomite powder. This type of ingot is annealed in a tunnel kiln for at least 8 days and nights. The limit of cooling rate is determined according to the resistance of the casting to cracking and edge and corner crushing. Adjust the cooling of the casting with a size of 600mmX300mm200mm, and the cooling time is 72h.
The total porosity of fused corundum refractory products is in the range of 27%~20%, of which 10%~12% is open. The reason for the relatively large porosity is carbon addition and gas saturated melt. When Al2O3 interacts with the carbon of the electrode, aluminum oxycarbide Al4O4C and Al2OC are formed. The low viscosity of Al2O3 melt itself crystallizes quickly and there is no time to exhaust, so a large number of small pores are formed with the casting. When castings cast with corundum crystallize, the porosity is successfully reduced significantly by slowing down the cooling of the melt. Reducing the carbon content, shortening the smelting time to a minimum and creating an oxidizing atmosphere in the furnace, by sucking air through the melt outlet and exhausting gas through the top. Careful management during smelting and using hollow electrodes can reduce the total porosity of the casting to 13%~8%.
Castings with a bulk density of less than 2.7g/cm3 have a structure with evacuated porosity. There are small shrinkage cavities in the center and upper part of the casting. When the bulk density is not less than 2.8g/cm, the shrinkage cavities are concentrated in the upper half of the product.
Molten corundum contains round corundum particles with an irregular structure of 0.03~0.4mm in size. The gaps between the particles are filled with glass phase (3%~5%). The pores are generally separated, with a round size of 0.01~0.3mm. The surface layer of the product is more porous, consisting of small crystals (0.1 mm) and larger pores (less than 1.4 mm).
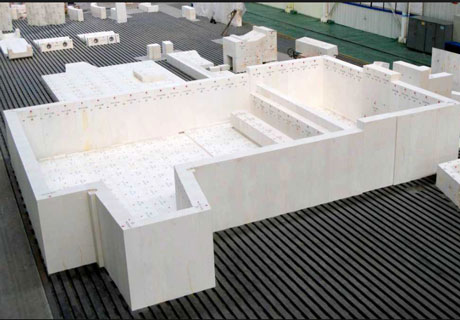
Cast Zirconium Corundum Products
In the Al2O3-ZrO2-SiO2 system, no ternary compounds and ternary solid solutions are found. The refractoriness of the ternary system with ZrO2 (badgezirconia) greater than 20%~30% exceeds 1750℃. The refractory materials of this system are named according to the ZrO2 content: AZS-33, AZS-36, AZS41, AZS-45. They are made by melt casting method. The structure of zirconium corundum products is fine-crystalline baddeleyite, corundum and silicate glass phase. The raw material for producing zirconium corundum refractory materials is industrial alumina (Al2O3 98%~99%, of which α-Al2O3 is less than 30%). Zircon concentrate, zircon contains ZrSiO4 93.6% (ZrO2 67. 2% and SiO2 33.8%), hafnium and other impurities from 0.5 to 4%. The refractoriness of iron-free zircon concentrate is 2200℃.
Characteristics of zircon corundum products: high compressive strength of 300~600MPa (normal temperature), maintaining structural strength at temperatures above 1700℃. Zircon corundum products have reduced thermal shock resistance compared with corundum due to polycrystalline transformation of ZrO2 in the range of 1100~1200℃.
Zircon corundum refractory materials, like many other molten refractory materials, are discharged (precipitated) from the liquid phase itself at high temperatures (beading process). For example, AZS-33 contains 25% glass phase, which precipitates at 1100~1200℃.
The method of adding a small amount of rare earth element oxides is implemented to reduce this effect. Adding B2O3 (not more than 0.25%) promotes the formation of borosilicate glass phase in refractory materials, which is very effective in improving thermal and chemical stability. In addition, B2O₃ promotes the dissolution of ZrO2 in the melt and increases its content in the liquid phase. In essence, zirconium dioxide increases the viscosity of the liquid phase and thus reduces the effect of water droplets. Water droplets are related to the oxidation of carbon present as impurities in the glass kiln bricks. The gaseous products of oxidation push the refractory glass phase onto the surface of the glass kiln bricks. Reducing the carbon content from the usual amount of 0.04%~0.08% to 0.01% has little effect on eliminating water droplets. Using an oxidation melting system can reduce carburization.
The following main reactions occur when melting the zirconium corundum batch. According to the reaction ZrSiO4 1540℃ – ZrO2+SiO2, zircon decomposes. During the melting of the batch, silicon dioxide is reduced (by carbon from the graphite electrode) to silicon SiO2+C → Si+CO2, which is re-oxidized Si+O2→SiO2 in the colder part above the electric furnace and precipitates as white flocs.
The reduction and subsequent oxidation of SiO2, and the infiltration of silicon monoxide react.
The unreacted part of SiO2 connects the impurities and additives in the silicate glass, and Fe2O3 and TiO2 are added when the melt crystallizes. When SiO2 is in excess, mullite is formed. The silicate phase in zirconium corundum products will reduce its corrosion resistance.
One of the main disadvantages of zirconium corundum refractory materials is its chemical and mineral heterogeneity.
The most dense and refractory ZrO2 crystallizes quickly and gathers in the dense layer at the bottom of the strip brick, and the lighter oxides gather on its upper part. Zirconia products have dense fine crystal bands, which are the best structure and improve their performance.
Zirconium corundum refractory materials are used as linings on the walls and roofs of glass melting furnaces. When the temperature of melting glass reaches up to 1600℃, the kiln wall can be used for 3 to 4 years. Mullite refractory materials are only used for 15 months under similar conditions.
After the 1970s, Japan developed fused-cast ZrO2 bricks with a ZrO2 content of about 94%. The microstructure is fine (50-150μm) baddeleyite crystals surrounded by glass phase. In order to obtain the appropriate viscosity, phosphate or B2O3 is used to modulate the liquid phase, and the glass is deformed to produce shrinkage-free products.