The refractory bricks used for lining the cement rotary kiln decomposition furnace and tertiary air duct are related to the size of the furnace. You can use high alumina bricks or sic mullite bricks, as well as high-strength alkali-resistant bricks.
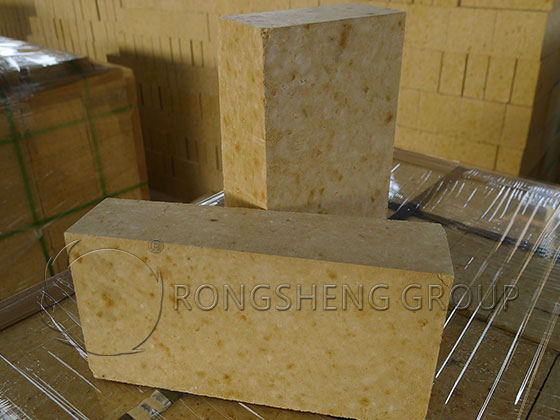
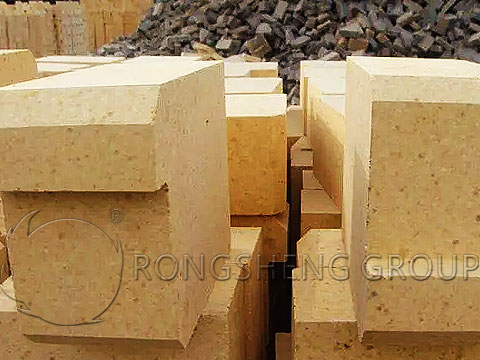
Refractory Bricks for Decomposition Furnace and Tertiary Air Duct of Cement Kiln
So, which kind of refractory brick is better to use in the decomposition furnace and tertiary air duct of the cement kiln? Generally speaking, silicon mullite bricks have the longest service life and better use effects. The 1550 sic mullite brick is used in the decomposition furnace of the cement rotary kiln, and the service life of the furnace lining is more than three years.
Of course, there are also Companies that use high alumina bricks and anti-flaking high alumina bricks. If high alumina bricks are used as a furnace lining, refractory bricks with an aluminum content of more than 70% must be used. However, peeling often occurs when used in these two areas. The service life of high alumina brick furnace lining is generally about one year. If anti-flaking high-alumina bricks are used, the use period will be relatively long, but the prices of the two bricks will be very different. Because zirconium is added to the raw material composition of anti-flaking high-alumina bricks, the price of zirconium is very high, which virtually increases the price of anti-flaking high-alumina bricks.
There are also high-strength alkali-resistant bricks. High-strength alkali-resistant bricks can still be used in the tertiary air ducts of cement rotary kilns because the alkali resistance of alkali-resistant bricks is more suitable for this part. However, it is more suitable to use anti-flaking high alumina bricks or 1550 sic mullite bricks for the decomposition furnace because of their long service life.
In the decomposition furnace and tertiary air duct of the cement kiln, if high-strength alkali-resistant bricks and high-aluminum bricks are used in these two parts, the service life of the high-strength alkali-resistant bricks will be longer than that of high alumina bricks. The reason is that the alkali resistance of high-strength alkali-resistant bricks will not cause the lining bricks to peel off, while the use of high-alumina bricks will often peel off under alkali erosion. As a result, the use time is short, resulting in frequent replacement, which increases the use cost.
At present, 1550 sic mullite bricks are mostly used in the tertiary air ducts and decomposition furnaces of cement rotary kilns. A certain proportion of silicon carbide is added to the sic mullite brick, which has strong wear resistance and corrosion resistance and can be used for more than three years. Avoid unnecessary trouble in terms of time and cost caused by replacing the lining multiple times. High alumina bricks cannot be selected because of the price difference between silicon molybdenum bricks and high alumina bricks. Repeated replacement of high alumina bricks will increase production costs.
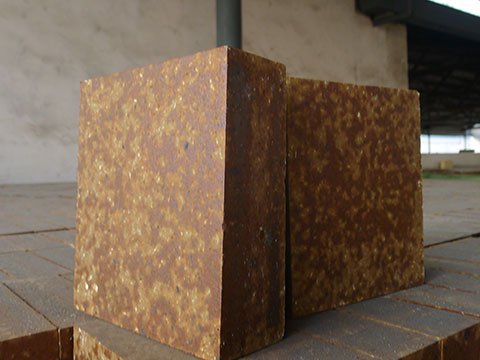
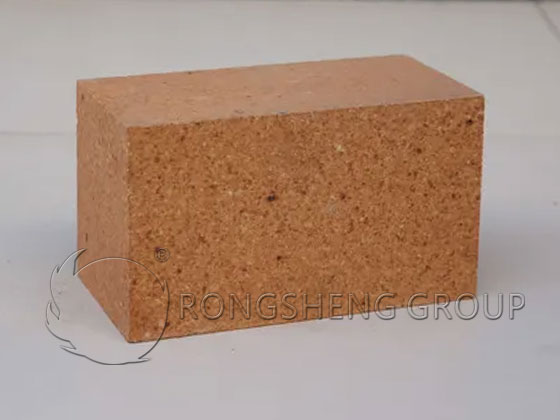
Application of Magnesia-Iron-Aluminum Spinel Bricks in Cement Rotary Kiln
Magnesia-iron-aluminum spinel bricks are prepared from synthetic iron-aluminum spinel and are used as lining materials for the cement rotary kiln firing zone. Good kiln skin performance and low thermal conductivity are very critical.
Magnesia-iron-aluminum spinel bricks contain iron and aluminum oxides, which can easily react with cement clinker to form C4AF (tetracalcium aluminoferrite). C4AF is a kiln skin bonding phase with very good performance.
Thermal conductivity is another very important indicator for measuring fired belt materials. In order to reduce the thermal conductivity of the material, the thermal conductivity of the magnesia-iron-aluminum spinel bricks is greatly reduced by controlling the crystal morphology, composition, and phase ratio of the complex spinel. This is very difficult to achieve for magnesia materials based on periclase, which is also the most prominent advantage of magnesia-iron-aluminum spinel bricks.
It can be seen from the photos of magnesia-chromium bricks and magnesia-iron-aluminum spinel bricks when the kiln was stopped that the magnesia-chrome bricks after the kiln was stopped have broken bricks, and the fractures are clear and obvious. For magnesia-iron-aluminum spinel bricks under the same conditions, the bonding of the kiln skin is still intact. It shows that the resistance of magnesia-iron-aluminum spinel bricks to sudden temperature changes is very stable, and the bond between the kiln skin and the bricks is also very intact. This also shows that under conditions of frequent temperature changes, magnesia-iron-aluminum spinel bricks show far better performance than magnesia-chrome bricks.
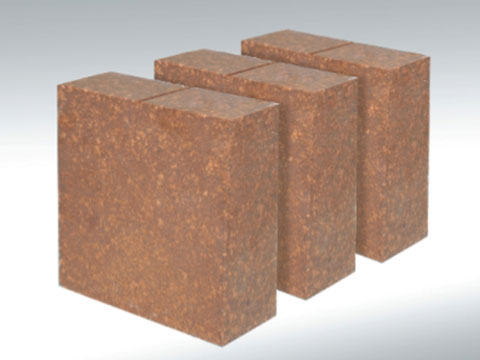
Application Advantages of Magnesia-Iron-Aluminum Spinel Bricks in Cement Kilns
According to the application summary of many companies, the outstanding characteristics of this magnesia-iron-aluminum spinel brick are as follows.
① The kiln skin forms quickly. ② The hanging kiln leather has good performance. ③ The kiln skin is stable and does not peel off when the kiln is stopped. ④ Good corrosion resistance, no alkali cracking or loosening. ⑤ The thermal conductivity is small and the rotary kiln shell temperature is low.
Problems and Improvement Measures of Magnesia Spinel Bricks Used in Cement Rotary Kilns
Magnesia spinel bricks were first used in cement kilns to deal with the chromium hazards caused by magnesia-chromium bricks. Magnesia spinel bricks not only have excellent thermal shock stability but also chemically react with cement clinker. A protective film is formed on the surface of the magnesia spinel brick, which can prevent the liquid phase from diffusing into the interior of the magnesia spinel brick. Therefore, the spalling resistance of magnesia spinel bricks is better than that of magnesia-chrome bricks.
However, to a certain extent, magnesia chrome bricks can be replaced by magnesia spinel bricks and used in cement rotary kilns. However, there are still some problems with magnesium spinel bricks.
- (1) The ability to hang the kiln skin is weak, and the refractory bricks will be severely chemically corroded, thus reducing the application time of the bricks.
- (2) The heat loss of the cement kiln body increases, and the heat consumption increases, resulting in a waste of materials.
- (3) Under high temperatures, a low melting point mineral phase is produced inside the magnesia spinel brick. Magnesium spinel bricks are susceptible to severe chemical attack and damage.
- (4) Magnesia spinel bricks can easily undergo a hydration reaction.
Therefore, in order to extend the service life of refractory bricks, improvements can be made from two aspects: its kiln hanging performance and peeling resistance. Among them, the methods to improve magnesia spinel bricks include the following measures:
- Add additives to magnesium spinel. For example: TiO2, Fe2O3, ZrO2, etc. The addition of additives is very beneficial to the firing of the material, the reduction of apparent porosity, the enhancement of chemical corrosion resistance, and the improvement of the ability to hang the kiln skin.
- Appropriately reduce the content of magnesium spinel. There are micro-cracks inside the brick, thereby reducing the thermal conductivity and improving the spalling resistance.
- Research has found that when the alumina content in refractory bricks is less than 10%, the bricks have better performance in hanging the kiln skin. Therefore, by reducing the alumina content in magnesia spinel bricks, the material’s ability to hang the kiln skin is improved.
In the application of cement rotary kiln, magnesium spinel bricks have high strength, excellent thermal shock stability, and strong resistance to chemical attack. It is mainly used in the upper and lower transition zones of cement rotary kilns and thermal kiln equipment that requires high-temperature resistance and thermal shock resistance.